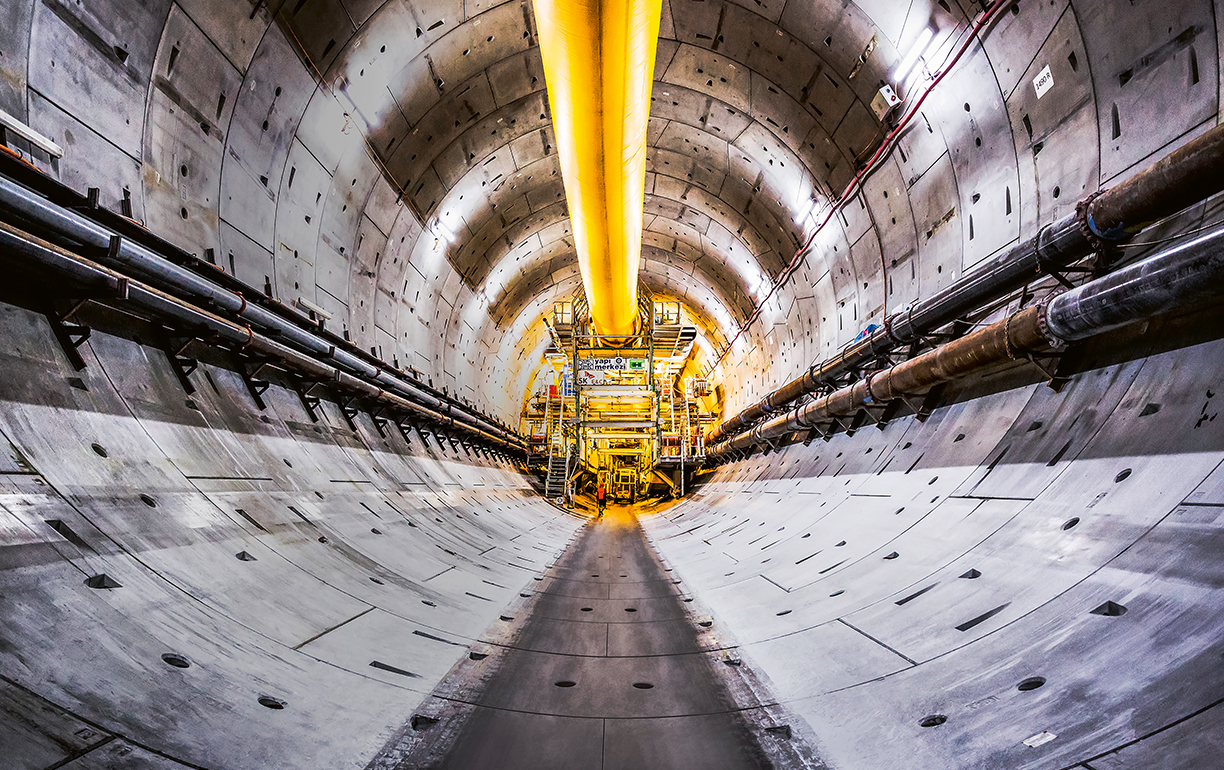
Tunneling a way through.
Shorter travel times and stimulus for the economy – tunnels can improve living conditions for people in many regions of the world. This engineering feat is possible thanks to the machines of market leader Herrenknecht – a company that is dependent, surprisingly often, on a reliable airfreight partner.
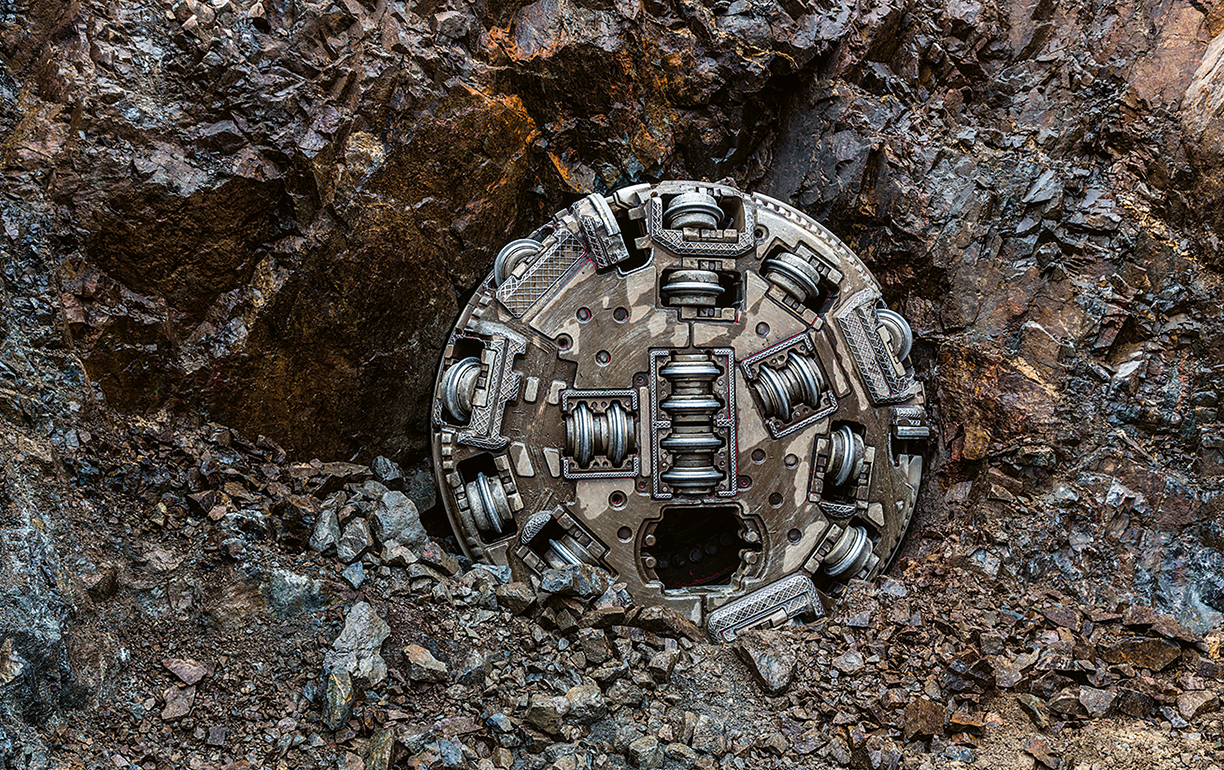
Until recently, the driving from the Istanbul Chamber of Commerce on the Golden Horn to the port on the Asian side meant one and a half hours of stop and go traffic. From the end of December, it only takes 15 minutes. Just before the turn of the year, the twin-deck Eurasia Tunnel was opened for traffic in the metropolitan area with a population of 14-million. The engineering master plan 106 meters below the sea provides lasting relief for the chronically clogged-up bridges above the Bosphorus Strait.
Train journeys between Zurich and Milan have similarly been significantly shortened since December: you can now board a train in the city on the Limmat River in the morning and go shopping at Milan at midday. In addition, trains no longer need to cross the Gotthard Pass at a snail’s pace. To that end, four Herrenknecht hard rock machines bored more than 85 kilometers of the two main tunnels each spanning 57 kilometers.
Regions come together, people reach their workplaces quicker, trade is supported and the environment is protected. Whether the Bosphorus or the Alpine massif: today, geographical barriers can be overcome in many cases thanks to modern tunnel structures. In that respect, small as well as huge tunnel boring machines from Herrenknecht play a key role worldwide. A rotating cutting wheel, equipped with socalled cutting knives and disc cutters, swiftly works its way through the underground ahead. The excavated earth is removed via conveyors or pumped off via slurry lines. Depending on the type of machine, protection provided by the shield chamber means precast concrete segments can be additionally transported through the completed part of the tunnel and assembled by the erector to form a new tunnel ring. The tunnel carcass is therefore extended ring by ring. No challenge seems to be too big for the founder and Chairman of the Board of Management, Martin Herrenknecht, and his team of engineers, machine operators, geologists and more than 90 other professionals. For example, at the Bosphorus crossing, the huge boring machine needed to withstand a water pressure of eleven bar. A particular challenge involved developing a cutting wheel that allows for the safe replacement of extraction tools from inside the cutting wheel, including under enormous pressure. |
The solution comprised cutting wheel arms that are accessible under atmospheric conditions and a transfer system developed for the tools by Herrenknecht. At the Gotthard Pass, unstable mountain layers caused difficulties for the tunnel builders. Nevertheless, the commissioned companies completed the task of excavating the tunnel one year ahead of schedule because the four huge cutting wheels called Sissi, Heidi, Gabi 1 and Gabi 2 were not only extremely reliable in terms of drift, they also notched up a speed record of 56 meters a day eating their way through the underground. In total, the gripper machines, which are several hundred meters long, excavated 13.5 million cubic meters of material from the Alpine massif. That is five times the volume of the Pyramid of Cheops. Herrenknecht can look back on 3,100 completed projects in 80 countries. 5,000 employees worldwide now work for the company that was established in 1977. New motorway and metro tunnels are just as much a part of the area of application as expansion of the supply and disposal infrastructure for waste water, drinking water, electricity, oil and gas. |
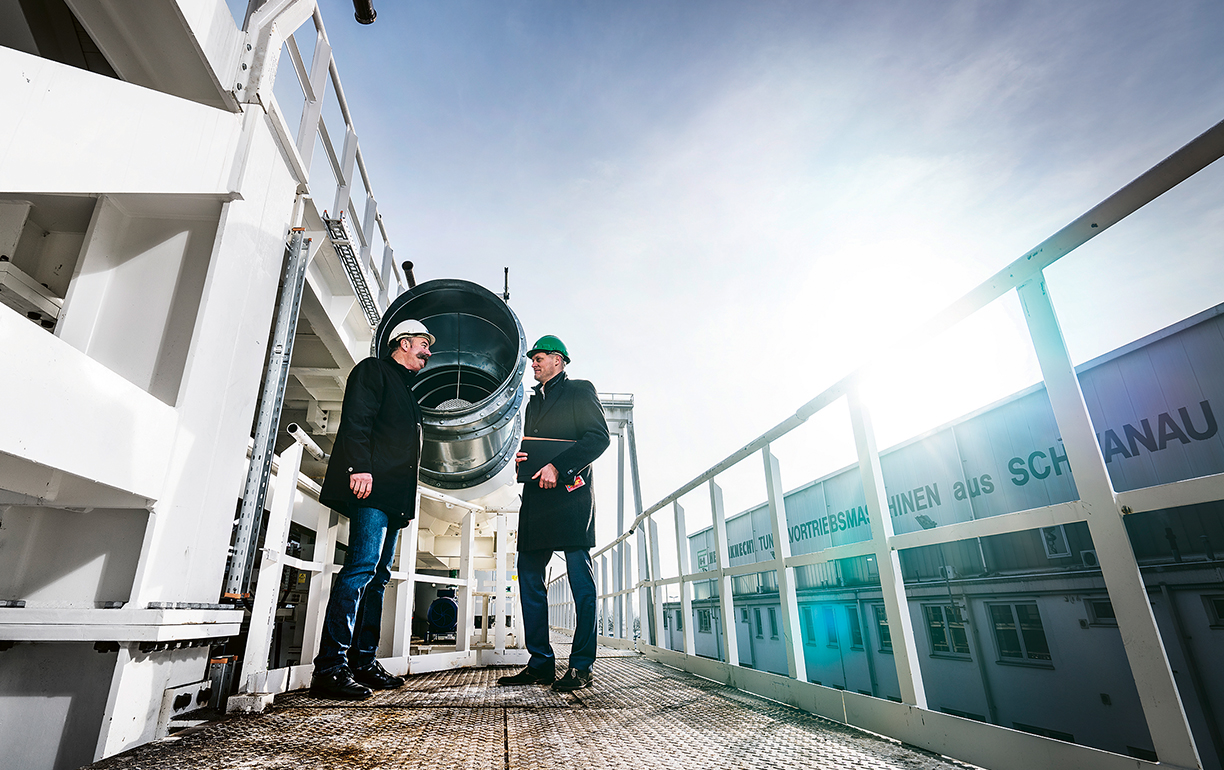
Herrenknecht’s drift machines pass beneath mountains, rivers, straits and densely populated areas, as is demonstrated by the company’s recent major projects. In Doha, Qatar, 21 Herrenknecht boring machines realized a project in a class of their own: only 26 months of construction were required for the 111-kilometer metro lines. The Crossrail project in London – a new rail line crossing the dynamic metropolitan area – also looks set to be completed in record time. Six earth pressure balance shields and two mixshields are boring their way precisely and safely amid sewers, gas pipelines and underground railway lines. As a result, Herrenknecht has created the foundation for a new, fast rail link for 200 million passengers annually between Heathrow in the west and Abbey Wood in the east.
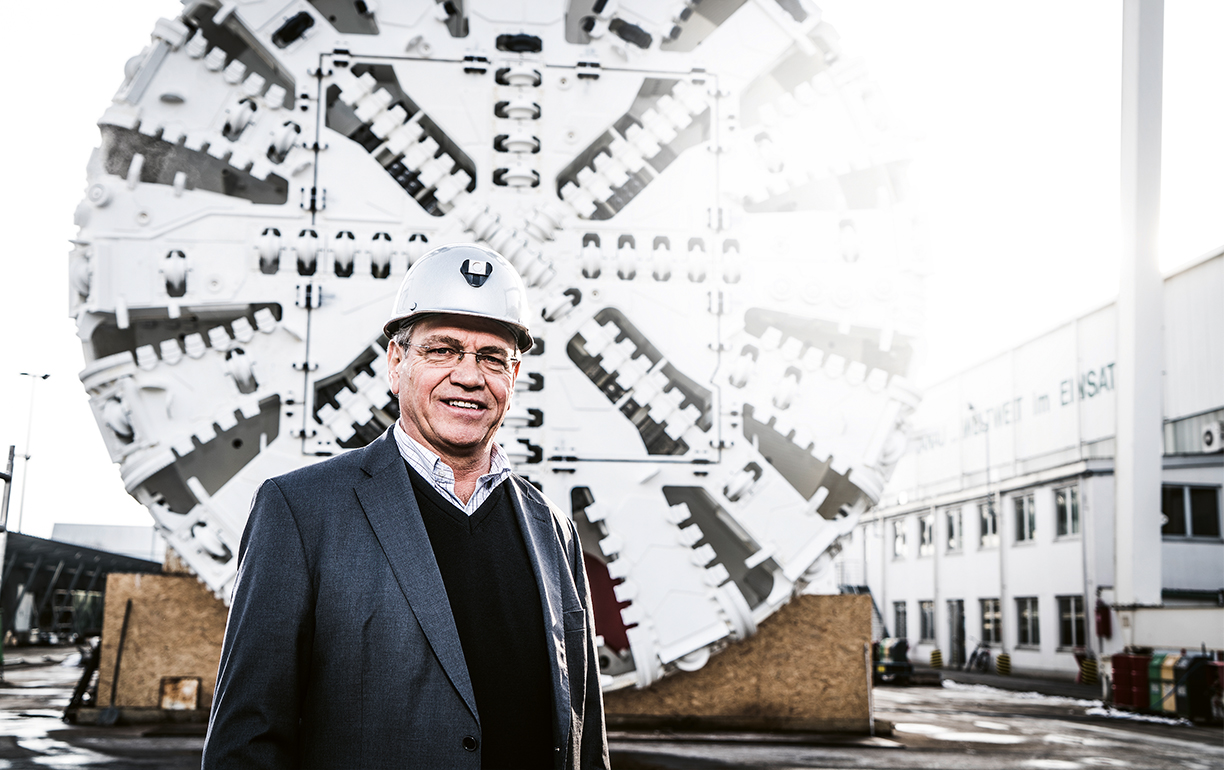
Modules transported to the construction site
Herrenknecht tunnel boring machines (TBMs) are normally unique, in particular if large diameters are required. Design, production and assembly of the giants which, in part, are several hundred meters long and made up of many thousands of individual parts, can therefore take up to one year. Of course, following comprehensive tests and acceptance by the customer, the high-tech equipment needs to be brought to the location where it is to be used. It embarks on the journey after being dismantled to create the largest possible parts. “Transport and logistics requirements need to be taken into consideration early on during the development phase,” explains Josef Gruseck, member of the Herrenknecht management.
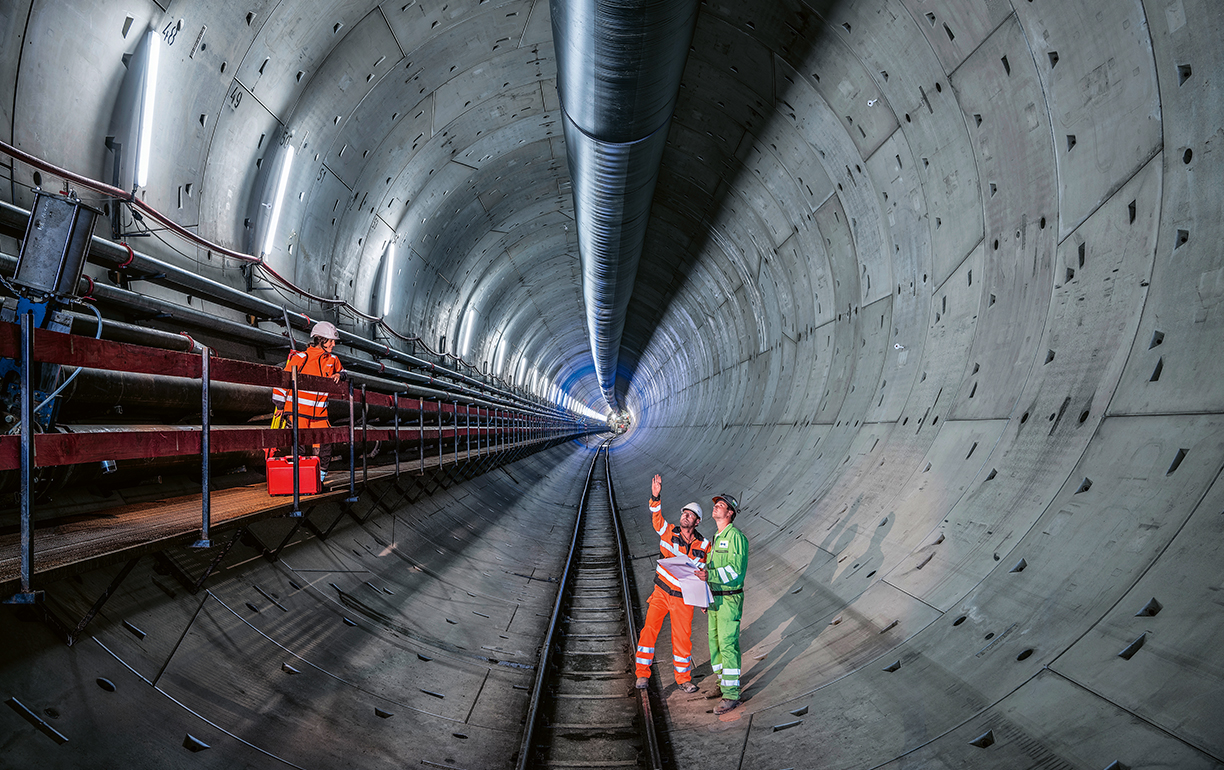
2,000 tons of freight each year
“In some cases, a TBM shield can be produced as a whole because it only has a few kilometers to travel on the truck as a single, major item. In other cases, the same component may need to be dismantled because of its size, the transport route and the construction site environment to reach the location where it is to be used. We construct the TBMs such that the construction site and transport-related size and weight requirements are met. Therefore, our transport experts have a seat at the table with the engineers on each major project from the outset.”
Trucks, container vessels and airplanes – Herrenknecht knows how to make the most of each carrier. “Airfreight is an integral part of our logistics – about 2,000 tons on average each year,” says Gruseck.
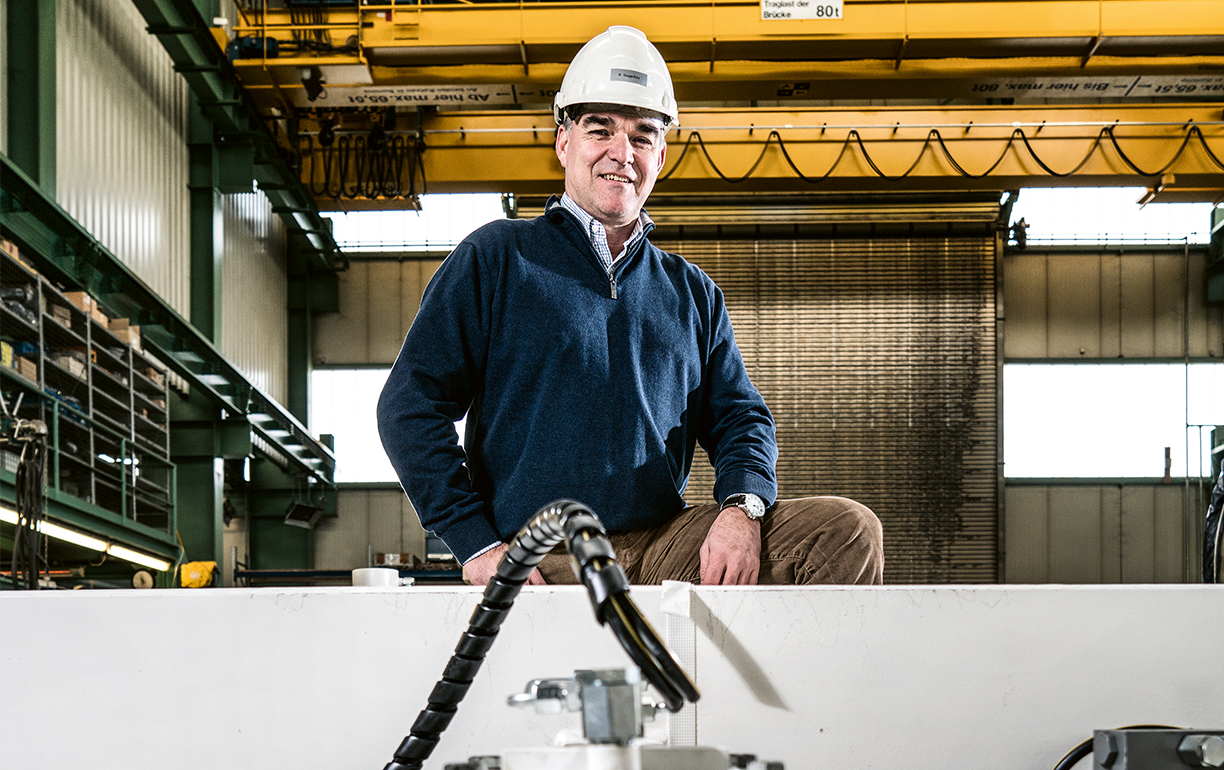
“In terms of procurement, it is just as important as transportation, in particular when supplying spare parts to the construction sites. TBMs are highly complex systems whose productive capacity is also conditional on the supply of wear-and-tear parts in line with requirements and on time.” Rainer Siegenführ, Shipping Head at Herrenknecht in Schwanau explains: “We ensure that parts that are immediately required arrive on site as quickly as possible. Thanks to service locations worldwide, we have proximity to our customers but still need to react quickly.” This may entail the most varied of parts from one-gram lightweight O rings to 32-ton main bearings.
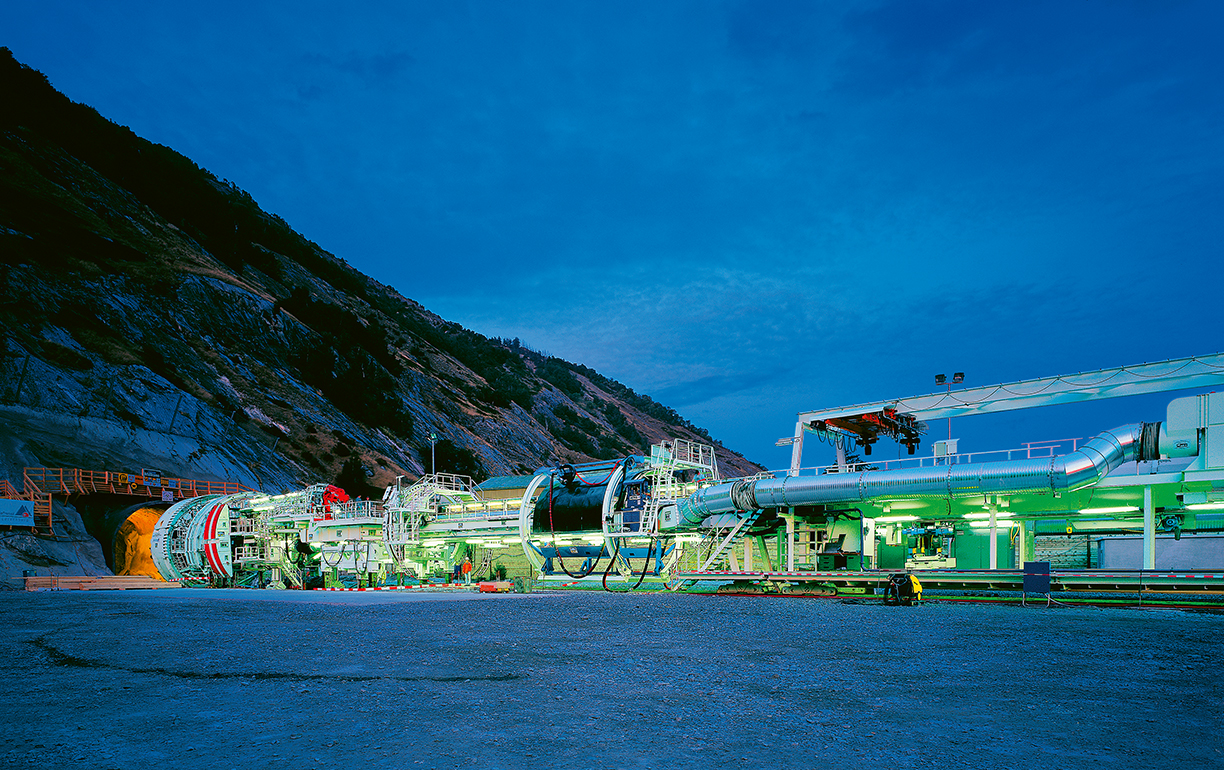
Perfect service via td.Pro
For transporting hazardous goods, Herrenknecht relies on Lufthansa Cargo – “Because of the quality and reliability in processing hazardous goods consignments,” says Peter Buss, who has a wealth of experience in the forwarding sector. He has been at Herrenknecht for 15 years now and specializes in the airfreight sector. In addition to the service locations, Herrenknecht operates local production and assembly locations – for example in Guangzhou in southern China – which maintain continual and lively contact with the headquarters in Germany.
Various core components are manufactured at the headquarters in Germany and shipped to the locations. Depending on the construction site location, Herrenknecht ships between 60 percent and 80 percent of airfreight via the carrier Streck Transport from Freiburg and Lufthansa Cargo. “Most of the consignments are sent via td.Pro,” says Peter Buss.
“We also attach importance to maintaining direct contact at all times with the decision makers at the forwarding agent and the carrier, and that is the case with Streck and Lufthansa Cargo.” Michael Engelhart, Sales Manager at Lufthansa Cargo in Baden-Wuerttemberg, and Alex Witzigmann from Streck, deal with all Herrenknecht matters. “We all come from the region, speak a common language and share a point of view: it is only time to knock off work once a transport operation has been successfully completed,” says Witzigmann. “Herrenknecht is a fascinating customer,” says Engelhart. “Whether underground railway construction in China or laying pipes in Brazil: you are always part of something really big.”
|
Quality and reliability are not the only arguments in favor of a transport operation via Lufthansa Cargo. “In many cases, it is simply more economical to fly a component,” says Josef Gruseck. And the customer’s requirements always have the highest priority, whether small pipeline construction sites or highly complex mega projects such as the metro construction in Doha involving 21 tunnel boring machines and several international construction joint ventures. “In general, our machines are expected to be extremely reliable. On occasion things need to move very quickly.”
|
Photos:
Herrenknecht and Matthias Aletsee
Pioneers from Germany
Pioneers from Germany
Herrenknecht is the only company that supplies modern tunnel boring machines for all construction ground types and diameters from ten centimeters to 19 meters. The product range comprises machines for the construction of traffic tunnels as well as supply and disposal tunnels such as pipelines and sewers. Herrenknecht provides integrated overall solutions with project-specific equipment and service packages. In addition to tunnel boring machines, the company supplies separation systems, conveyors, navigation systems, rolling stock systems and entire tubbing factories. The company furthermore develops systems for the sinking of vertical shafts in great depths and for excavating inclined shafts. The portfolio also includes boring machines that penetrate the earth to a depth of 8,000 meters. In 2015, the Herrenknecht Group generated turnover of almost 1.3 billion euros. It employs approximately 5,000 employees and is represented worldwide with 76 subsidiaries and holding companies.