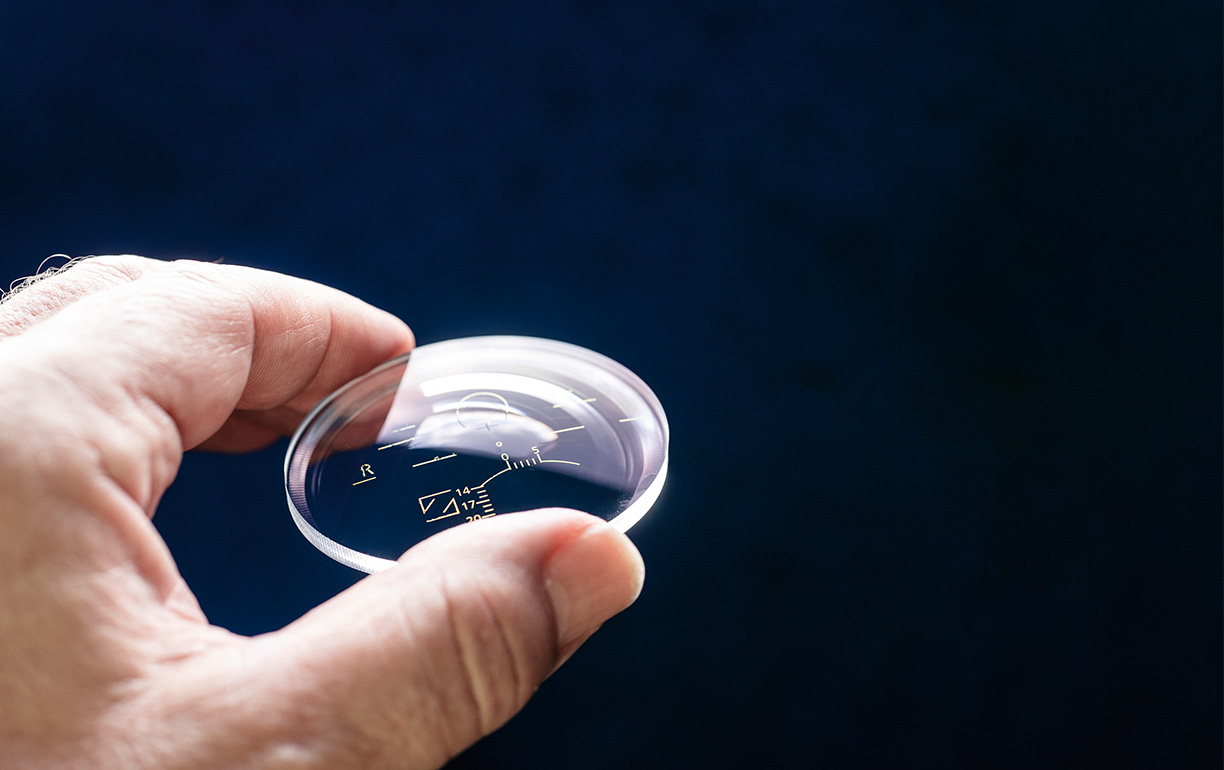
Crystal clear.
Serdar Katilmis is keeping a very close eye on four cartons. The contents of the boxes will provide hundreds of people with better vision: they are spectacle lenses made by Zeiss Vision Care. They just arrived in Frankfurt from overseas in the belly of a Lufthansa Boeing 747-8. In just a few hours they will continue their journey on an Airbus A320neo bound for Milan – and from there they will go to opticians all over Italy by courier.
Serdar Katilmis is making sure that the transit in Frankfurt runs like clockwork. “I just checked the goods for damage and reviewed the information in the AWB, and everything is fine!” To do that he did not need glasses. But he did drive an apron vehicle owned by time:matters, the Lufthansa Cargo subsidiary for high-performance and special speed logistics. Zeiss has been making extensive use of the services of this company since 2016.
As one of the world’s leading manufacturers, Zeiss sells more than 100 million spectacle lenses each year. A considerable proportion of these are prescription lenses. They are manufactured according to precise specifications provided by ophthalmologists or opticians, and often also according to the wishes of the individual buyers. “For these lenses, the range of different products is potentially infinite. Ultimately each is a unique product, which means we are working with a batch size of one,” says Jürgen Schwenk, Head of Global Logistics & Distribution. The lenses are manufactured in Zeiss-owned, highly automated plants in Germany and around the globe.
This is where Serdar Katilmis and his colleagues at the time:matters Courier Terminal at Frankfurt Airport enter the picture: time:matters makes sure that the lenses arriving from three different overseas factories reach Frankfurt quickly – and then go to opticians located all over Europe just as fast. Even the most complex products arrive at their destination within just a few days after an order was placed. Before Zeiss decided to work with these speed specialists, it used to take an extra day on average.
As one of the world’s leading manufacturers, Zeiss sells more than 100 million spectacle lenses each year. A considerable proportion of these are prescription lenses. They are manufactured according to precise specifications provided by ophthalmologists or opticians, and often also according to the wishes of the individual buyers. “For these lenses, the range of different products is potentially infinite. Ultimately each is a unique product, which means we are working with a batch size of one,” says Jürgen Schwenk, Head of Global Logistics & Distribution. The lenses are manufactured in Zeiss-owned, highly automated plants in Germany and around the globe. |
This is where Serdar Katilmis and his colleagues at the time:matters Courier Terminal at Frankfurt Airport enter the picture: time:matters makes sure that the lenses arriving from three different overseas factories reach Frankfurt quickly – and then go to opticians located all over Europe just as fast. Even the most complex products arrive at their destination within just a few days after an order was placed. Before Zeiss decided to work with these speed specialists, it used to take an extra day on average. |
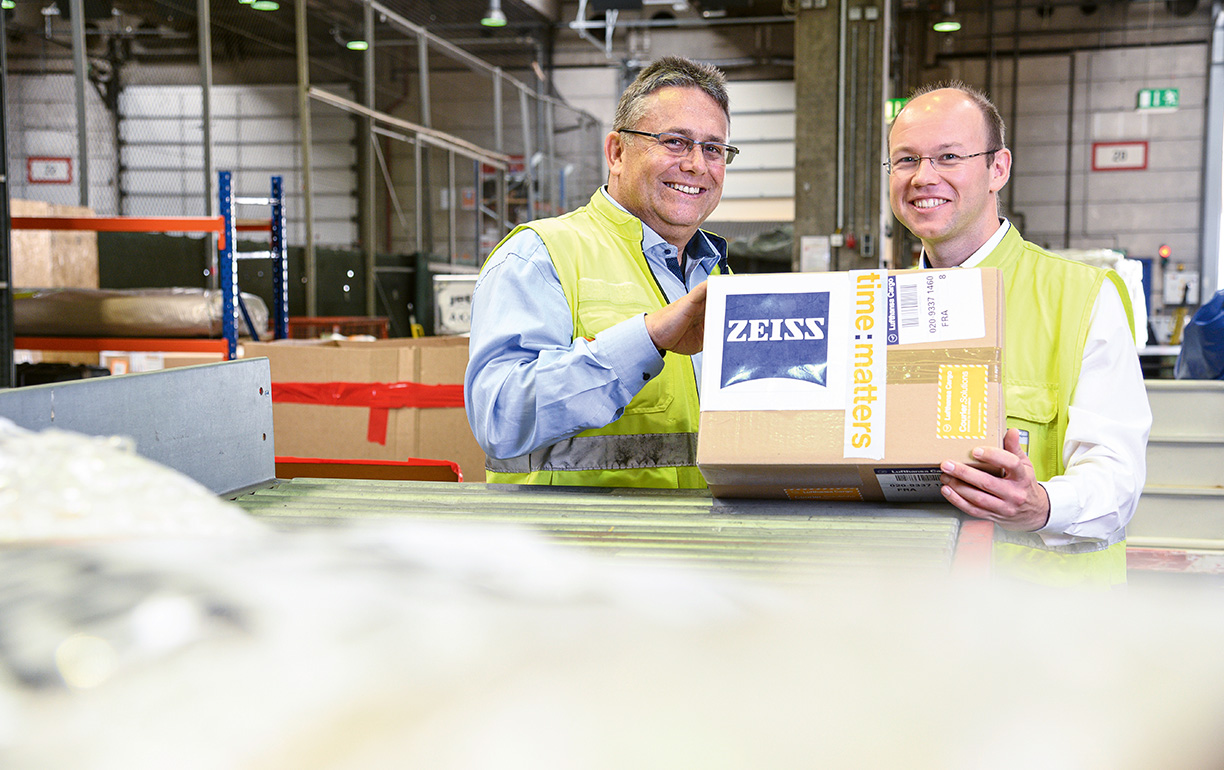
Direct access to the apron.
This saving makes an enormous difference for Zeiss: “In this new era of online shopping with same-day delivery, the time customers are prepared to wait for their new glasses is getting shorter and shorter,” explains Jürgen Schwenk. “You could be manufacturing the best lenses in the world, but if they do not arrive at the optician’s quickly enough, he will not place another order with you.” There are limits to how much the actual production time can be reduced. This is why it is important to speed up the supply chain.
How does time:matters do that? By making use of the dense worldwide network of routes maintained by Lufthansa Cargo and 20 other partner airlines to which the Zeiss prescription lens manufacturing plants are linked. All Zeiss shipments are sent directly to Frankfurt – for example via Bangalore, Hong Kong and Los Angeles.
The transports use the global time:matters service Sameday Air, in combination with the Lufthansa Cargo express product “Courier.Solutions.” This not only meets the requirements in terms of speed, but also as regards access to the required capacities. “The shipments are assigned a high loading priority,” says Christian Schenk, who is the primary contact for Zeiss as Global Key Account Manager at time:matters. “This means that the freight will be available at our hub in Frankfurt 60 minutes after arrival, and will be accepted for loading 90 minutes prior to departure.”
Loading and transportation on the apron is carried out by trained ground-handling staff who work for time:matters exclusively. “These colleagues can spot Zeiss shipments from a distance, and they know exactly what matters,” says Schenk. The merchandise is broken down, built up as well as re-secured at the time:matters Courier Terminal, which has direct access to the apron. These shipments are neither consolidated nor loaded at the same time as other freight.
Operations at the Courier Terminal are ongoing as long as aircraft land and take off again: from 5:30 a.m. to 11 p.m., including weekends. During this period, a total of four employees are responsible for monitoring activities out on the apron. Whenever they identify a shipment that requires particularly rapid handling, they make sure that it is loaded “tail to tail”: from aircraft to aircraft. Sometimes they can manage it in less than 60 minutes. At the destination airports as well as at the airports of origin, time:matters works closely with transport and courier service providers – and with customs agents along the entire supply chain. This means that, in addition to the actual airport-to-airport transport, customs clearance as well pickup and delivery of shipments can also be offered on request.
How does time:matters do that? By making use of the dense worldwide network of routes maintained by Lufthansa Cargo and 20 other partner airlines to which the Zeiss prescription lens manufacturing plants are linked. All Zeiss shipments are sent directly to Frankfurt – for example via Bangalore, Hong Kong and Los Angeles. The transports use the global time:matters service Sameday Air, in combination with the Lufthansa Cargo express product “Courier.Solutions.” This not only meets the requirements in terms of speed, but also as regards access to the required capacities. “The shipments are assigned a high loading priority,” says Christian Schenk, who is the primary contact for Zeiss as Global Key Account Manager at time:matters. “This means that the freight will be available at our hub in Frankfurt 60 minutes after arrival, and will be accepted for loading 90 minutes prior to departure.” Loading and transportation on the apron is carried out by trained ground-handling staff who work for time:matters exclusively. “These colleagues can spot Zeiss shipments from a distance, and they know exactly what matters,” says Schenk. |
The merchandise is broken down, built up as well as re-secured at the time:matters Courier Terminal, which has direct access to the apron. These shipments are neither consolidated nor loaded at the same time as other freight. Operations at the Courier Terminal are ongoing as long as aircraft land and take off again: from 5:30 a.m. to 11 p.m., including weekends. During this period, a total of four employees are responsible for monitoring activities out on the apron. Whenever they identify a shipment that requires particularly rapid handling, they make sure that it is loaded “tail to tail”: from aircraft to aircraft. Sometimes they can manage it in less than 60 minutes. At the destination airports as well as at the airports of origin, time:matters works closely with transport and courier service providers – and with customs agents along the entire supply chain. This means that, in addition to the actual airport-to-airport transport, customs clearance as well pickup and delivery of shipments can also be offered on request. |

Reliability matters, too.
“What is just as important to us as speed is reliability,” says Jürgen Schwenk, the head logistician for Zeiss Vision Care. If the boxes whose transit Serdar Katilmis supervised this morning do not make it onto the plane to Milan, then a number of Italian opticians will be left without the firmly promised lenses – and will instead be facing their disappointed customers. And so the employee drives the car onto to apron right on time for the loading of the Airbus A320neo and makes sure everything runs smoothly.
But he does not stop there: as the ground-handling guy lays the shipment onto the conveyor leading into the belly of the passenger jet, Katilmis take a photograph of the shipment. “I then mail the photograph to the Courier Terminal, as confirmation for the customer.” The people at Zeiss appreciate this level of service – and they are planning to make even greater use of it in the future. Besides Italy, the target markets currently are Germany, France, the UK and Spain, but in the next few months the Benelux countries, Portugal, Scandinavia and several Eastern European countries will also be added.
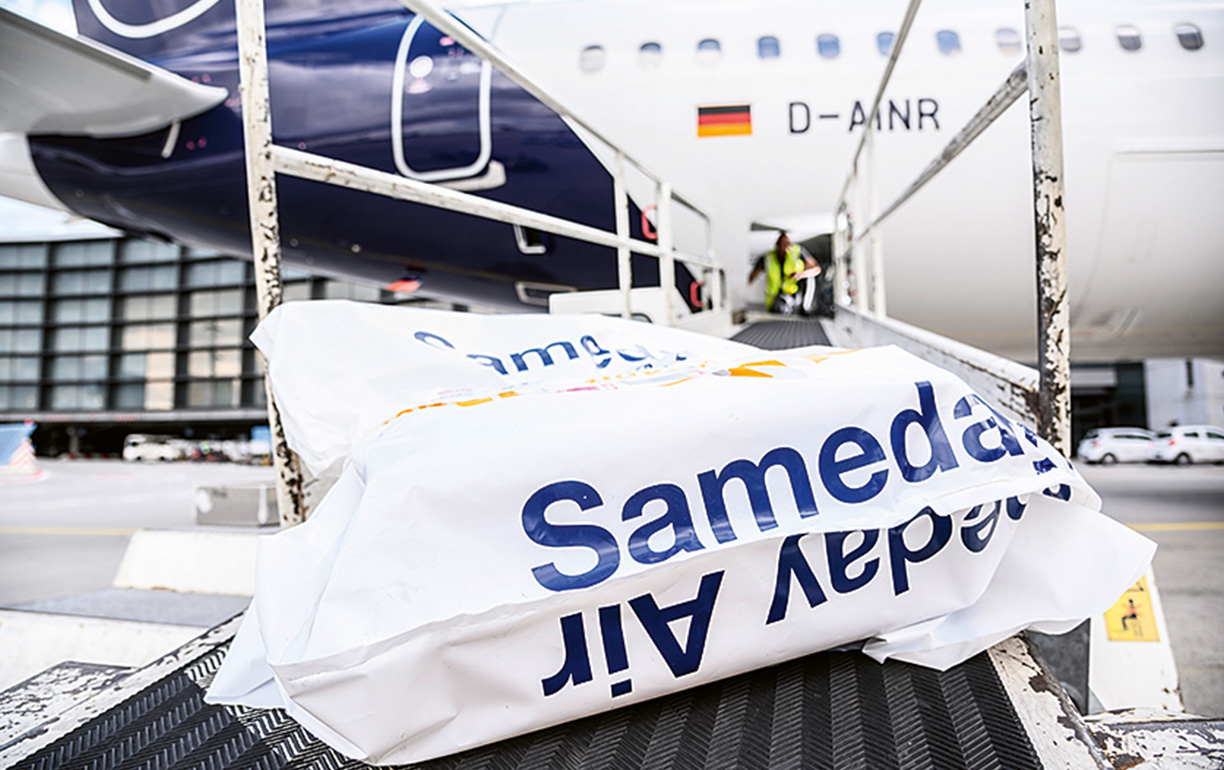
Sameday Air network.
The Sameday Air product allows time:matters to offer customers same-day shipping for time-critical consignments. The European hubs in Frankfurt, Munich, Vienna and Brussels serve more than 100 stations on the entire continent as well as in Israel. There are another 16 stations in the United States and in Mexico. Not only that: this summer the Sameday Air network was extended to Asia for the first time. It now also includes seven stations in China: Shanghai, Shenyang, Beijing, Nanjing, Qingdao, Chengdu and Guangzhou. Customers in China are looked after by the separately established company time:matters Shanghai International Freight Forwarding Ltd. The other Asian stations are Tokyo (NRT), Singapore and the Thai capital Bangkok.
www.zeiss.com/vision-care
www.time-matters.com
Photos: Stefan Wildhirt