It’s not all waste at Lufthansa Cargo
Waste separation and recycling in FRA: In 2022, the percentage of our waste in Frankfurt that was returned to material recycling was 38%. That is around 1% more than in the prior year and is to be increased to 40% by 2025. And we are all working together to achieve this percentage.
Directly opposite the P53 is the Lufthansa Cargo waste disposal area – the largest in the Lufthansa Group. Here afterwards, 99% of waste is recycled for material and energy recovery (energy as a by-product or main product). That means the work done here for the environment is all the more important. The more effectively waste is separated, the higher the recycling rate and therefore the better the conservation of valuable resources. Every day, mesh pallets containing waste are brought to the disposal area from the buildings, where the waste is sorted again, partly compacted, and then put into our disposal company’s large containers.
Approximately 800 tonnes of waste wood is accrued every year, which is equivalent to eight fully loaded Boeing 777 freighters. Once it has been pulverized, this waste wood is mainly sent by our disposal company for energy recovery. Another major item is waste paper, which totals around 100 tonnes. This ends up back in paper processing via our disposal company. Some 500 tonnes of waste film is fed into a plastic press and then granulated and sold by our disposal company. New plastic is made from this waste product. You can find out more about plastic film below.
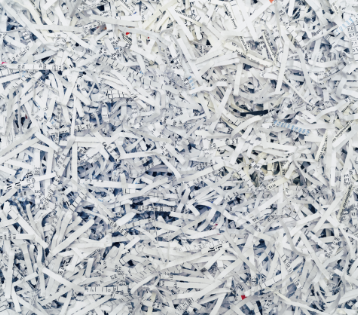
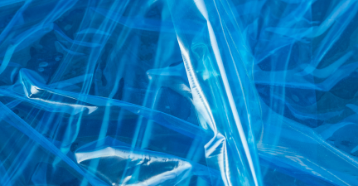
Plastic and loading equipment
Every year, Lufthansa Cargo requires more than 500 tonnes of plastic film to protect its freight on pallets around the world. Some 25 kg of film travels inside each freighter. We are therefore working hard to explore how we as a company can use less plastic film – particularly when it comes to our loading equipment – and procure a more environmentally friendly product as well, while helping to ensure that it is disposed of correctly worldwide.
Ready for tomorrow
Plastic poses a problem for people and the environment in many ways. Raw materials from fossil sources are wasted on short-lived plastic products and the amount of plastic waste ending up in the environment, in landfills, and in the world’s oceans is rising sharply. The production of many single-use plastic products was finally banned in the EU in July 2021. Further-reaching measures are highly likely in the future, which is why we are already setting out now to take action as an industry pioneer.
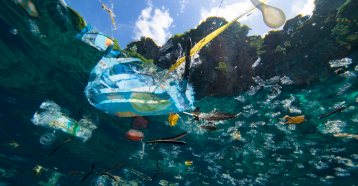
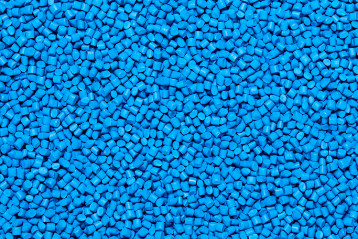
Bioplastic foil as interim solution
Our plastic strategy comprises many aspects, which we are constantly working on. We have already established that the single ideal green solution does not exist. We need to weigh up opportunities and risks, try out various options, and learn from our experiences. Our local sourcing activities led us to “bioplastic film” – and we learned that not all bioplastic films are the same. There is an important difference between bio-based (based on sustainable raw materials) and biodegradable (which is naturally more degradable than conventional film).
Our disposal company in Frankfurt, where over 400 tonnes of waste film are accrued every year, has informed us that some types of “bioplastic film” disrupt the material recycling process. At the moment, our waste film is used to produce granulate in Frankfurt, and then begins a new cycle of use.
Bioplastic films of this kind are viewed very critically by some scientists, who recommend that bioplastic films should only be used in areas where collection from the environment is difficult or not possible at all (such as agriculture). It is currently unclear which direction the regulations will take or in which sectors tougher requirements will be stipulated.
Beware when recycling
To date, we have relied on the fact that our used film is collected separately by handling providers at all our facilities worldwide and disposed of correctly by the airport operator. In reality, we are not entirely sure what happens to it in each location.
That is why we have enlisted the support of a master’s student at Commercial and Production Western Europe to find out whether our film is actually recycled around the world or at least being used for energy recovery. Our film is made of polyethylene (PE), has a chemical composition of 100% hydrogen and carbon, is fully recyclable, but also burns without residue to produce carbon dioxide and water, and is a welcome energy source for incinerators. Until we have certainty on this matter, we want to use a “more biodegradable bioplastic film” as it is less harmful to the environment at the moment. However, the prerequisite is that they do not interfere with material recycling.
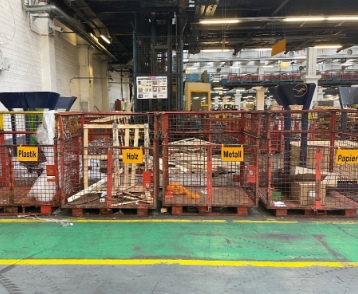
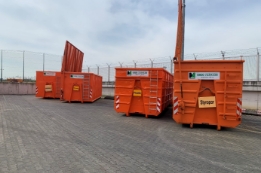
Four fields of action on the subject of plastic
- The top priority (also according to the generally accepted waste hierarchy) is that no plastics find their way into the environment. In order to rule this out and to ensure that waste is separated and disposed of in the most sustainable way everywhere, we have set ourselves the goal of increasing the global recycling rate of our foil to 100% by 2025. Therefore we are working on placing more responsibility on our ground handling agents (GHA). We have already formulated requirements in our supplier evaluations. The next step is to include them in new contracts.
- Together with Global Handling Processes, we have adopted the reuse principle and expressly permitted reuse in our Cargo Handling Manual. It is now up to our individual facilities, working together with their GHA, to look at where they can implement this principle. In Munich, for example, bottom film that is still intact is already simply left on the dolly.
- Our medium-term goal is to achieve a closed loop with high environmental standards. That is why, with the support of Infrastructure LCAG, our Frankfurt team is conducting a trial in which it returns some of our waste film to our manufacturer Verpa, who will feed it back into the production process. Since May 2022, we use a foil of this kind made of 10% recyclates. The manufacturer intends to continuously increase this percentage.
- In the long term, the requirement for our foil is that the remaining share is made from sustainable raw materials.