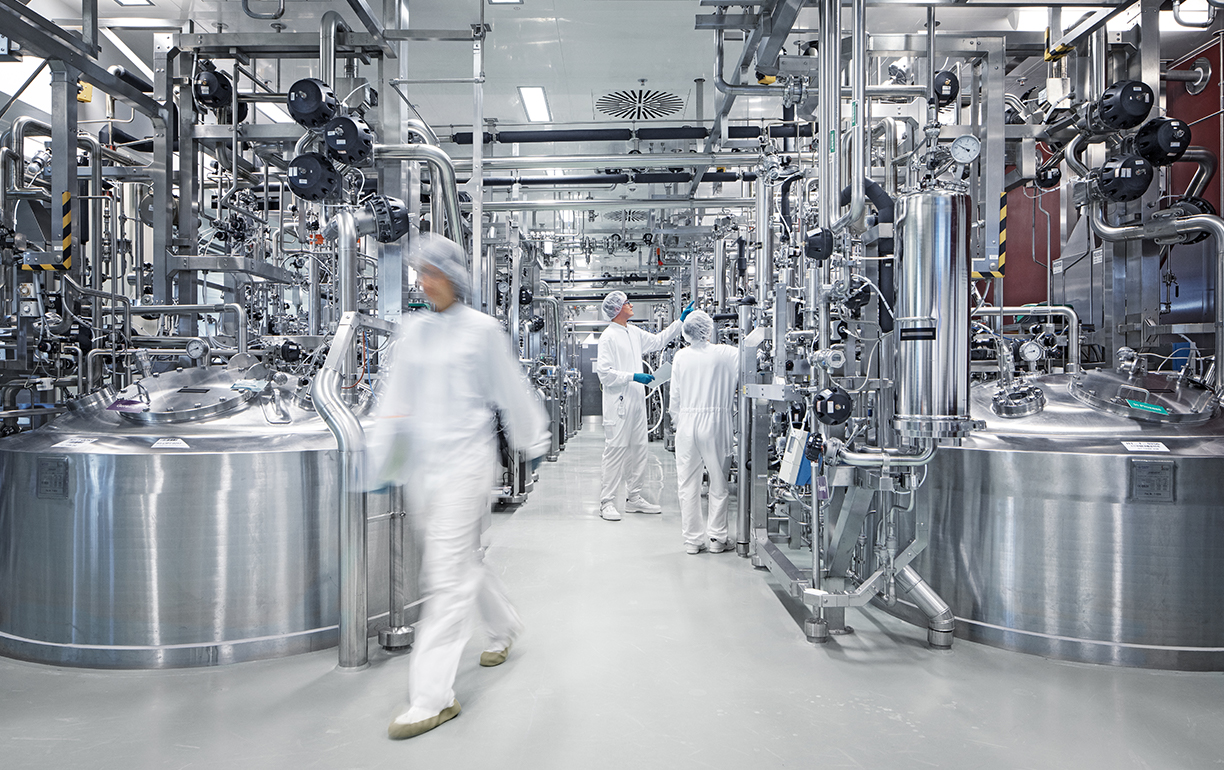
Arctic temperatures on board.
On Greenland's ice cap, the average temperature in winter is -33°C. Cold, but not cold enough. Biopharmaceuticals from Boehringer Ingelheim must be transported at -40°C all around the globe, but how do you manage this far away from the polar caps? va-Q-tec developed a container in cooperation with the pharmaceutical company that masters this extreme performance.
The production sites of Boehringer Ingelheim are spread across the planet like a spider's web. Biopharmaceutical raw materials are produced in California, Shanghai and Vienna. "Can you imagine? It is almost like brewing beer," jokes Horst Langhammer, Head of Supply Chain Management & Logistic Projects at Boehringer Ingelheim. "You bring the relevant substances together in a fermenter and after the fermentation process takes place, you separate them from the waste products and obtain highly concentrated active ingredients". After production is completed, the active ingredients must be cooled to -40°C. At this temperature, cell division and decay of the molecules no longer takes place - the pharmaceutics are in a kind of cryosleep. Biberach an der Riß is the only site in the world that has the special preparation facilities. Here the active ingredient is thawed, enriched with water and filled into syringes as anti-rheumatic drugs, for example.
The production sites of Boehringer Ingelheim are spread across the planet like a spider's web. Biopharmaceutical raw materials are produced in California, Shanghai and Vienna. "Can you imagine? It is almost like brewing beer," jokes Horst Langhammer, Head of Supply Chain Management & Logistic Projects at Boehringer Ingelheim. "You bring the relevant substances together in a fermenter and after the fermentation process takes place, you separate them from the waste products and obtain highly concentrated active ingredients". |
After production is completed, the active ingredients must be cooled to -40°C. At this temperature, cell division and decay of the molecules no longer takes place - the pharmaceutics are in a kind of cryosleep. Biberach an der Riß is the only site in the world that has the special preparation facilities. Here the active ingredient is thawed, enriched with water and filled into syringes as anti-rheumatic drugs, for example. |
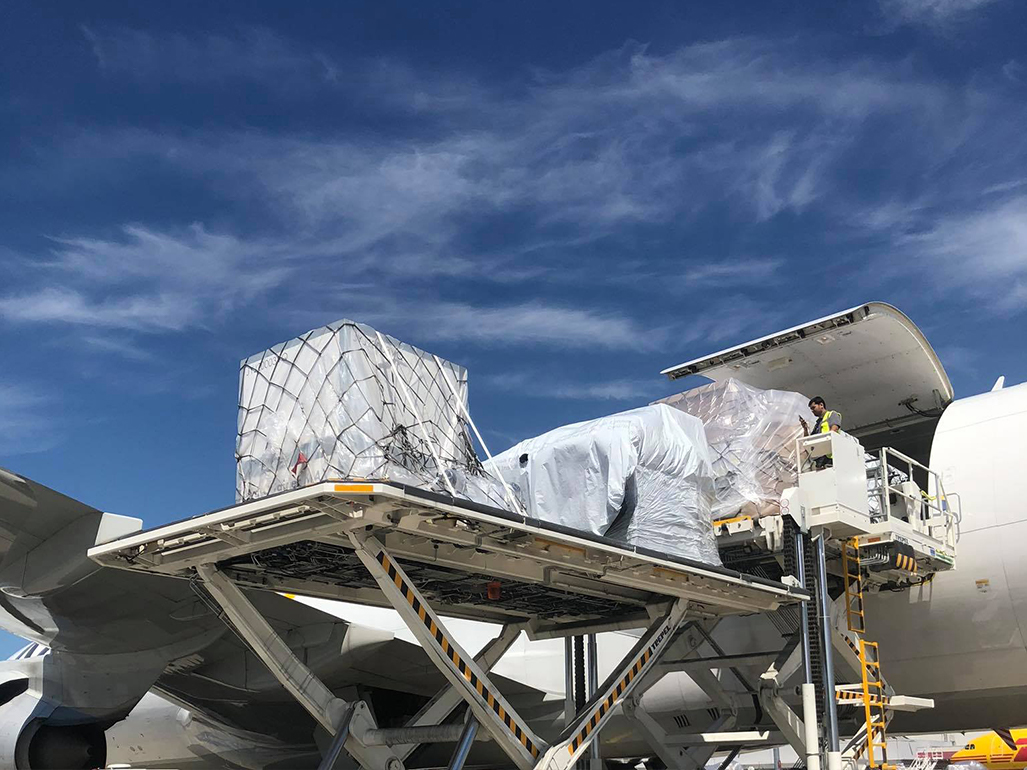
"Where is the airport of Biberach?"
The distance from North America or Asia to Upper Swabia is a challenge that the logistics team consisting of Boehringer Ingelheim, the forwarding agent DSV, the thermal packaging specialist va-Q-tec and Lufthansa Cargo is happy to take on.
Foreign colleagues have often asked Langhammer where the airport of Biberach is located. The expert for supply chain management can still smile about that. The city with just under 35,000 inhabitants does indeed have an airport, but only aircraft up to 5.7 tons are allowed to land there. A single shipment of frozen biopharmaceuticals would almost reach this weight. Transportation from the freighter hub in Frankfurt to Biberach is not a complicated task but keeping a cooling system active for a total of 80-90 hours at such low temperatures is the real challenge.
To overcome this test Boehringer Ingelheim turned to va-Q-tec, pioneer of highly efficient products and solutions in the field of thermal insulation and temperature-controlled logistics. Together, they developed a new type of container in record time - the va-Q-tainer MAXx - which can cool below -30°C over several days without power supply or the use of dry ice - thanks to special temperature storage elements. In addition to the necessary reliable temperature stability and the fastening of the tank inside, the height of the container was also important, in order to transport the pharmaceutical products safely and without further complications. The height of the container requires its transportation only on a freighter main deck position. Lufthansa Cargo connects Los Angeles several times a week with a B777F directly to Frankfurt. The reliable connections were one of the decisive factors in choosing Lufthansa Cargo.
Foreign colleagues have often asked Langhammer where the airport of Biberach is located. The expert for supply chain management can still smile about that. The city with just under 35,000 inhabitants does indeed have an airport, but only aircraft up to 5.7 tons are allowed to land there. A single shipment of frozen biopharmaceuticals would almost reach this weight. Transportation from the freighter hub in Frankfurt to Biberach is not a complicated task but keeping a cooling system active for a total of 80-90 hours at such low temperatures is the real challenge. To overcome this test Boehringer Ingelheim turned to va-Q-tec, pioneer of highly efficient products and solutions in the field of thermal insulation and temperature-controlled logistics. |
Together, they developed a new type of container in record time - the va-Q-tainer MAXx - which can cool below -30°C over several days without power supply or the use of dry ice - thanks to special temperature storage elements. In addition to the necessary reliable temperature stability and the fastening of the tank inside, the height of the container was also important, in order to transport the pharmaceutical products safely and without further complications. The height of the container requires its transportation only on a freighter main deck position. Lufthansa Cargo connects Los Angeles several times a week with a B777F directly to Frankfurt. The reliable connections were one of the decisive factors in choosing Lufthansa Cargo. |
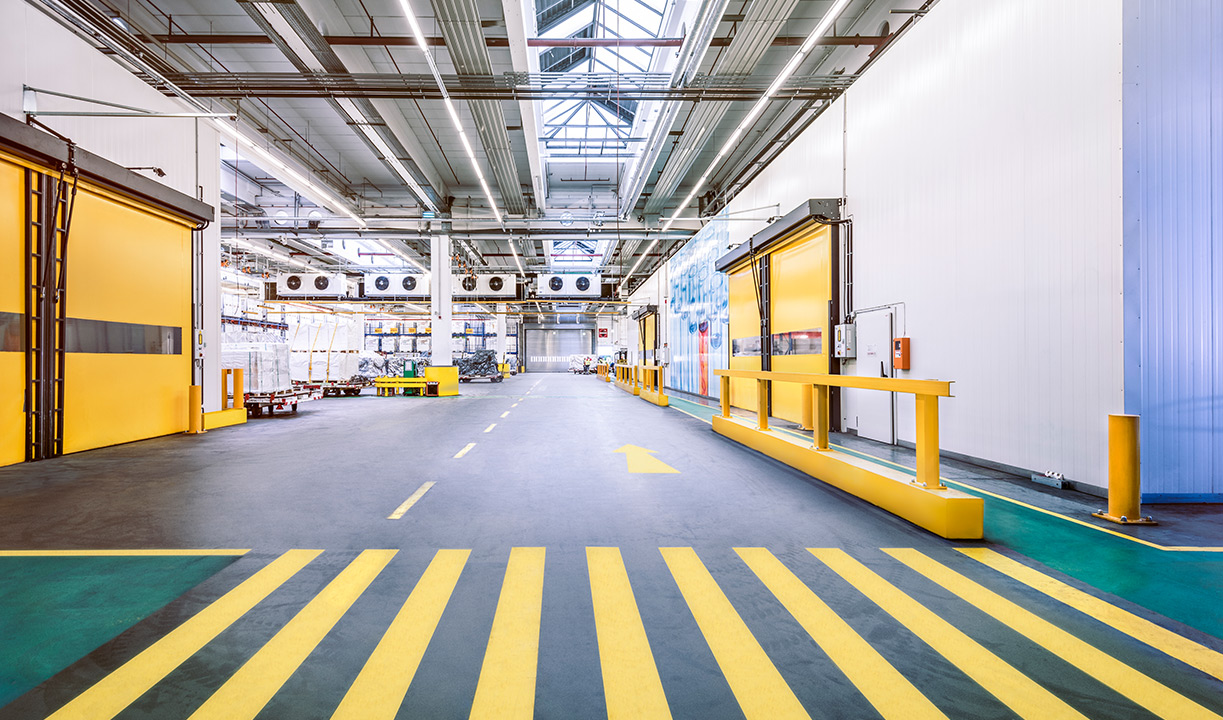
Opened in 2011, the Pharma Hub at Frankfurt Airport offers over 8,000 square meters of space for precise temperature control, handling by proven experts and short transport routes thanks to its direct location next to the apron.
Experts for temperature sensitive transports.
Boehringer Ingelheim relies on DSV for the end-to-end organization of the transport. "For such transports, we work together with global logistics service providers who have expertise in this field," says Horst Langhammer. One of those experts is Bernhard Woerner, Global Account Director, Health Care at DSV. The logistics provider has been handling transports in the pharmaceutical industry since 2006. "The challenge is precise timing on the ground. The tank is delivered and filled just-in-time in Fremont, California. It is placed in the perfectly prepared container and goes straight on its long journey in a refrigerated truck. The truck brings the shipment to the airport in Los Angeles, but waits until the plane has taken off in case of unexpected delays or cancellations. Once it arrives in Frankfurt, the va-Q-tainer MAXx passes through the Lufthansa Cargo Pharma Hub and then again onto a refrigerated truck to be transported directly to Biberach," Woerner explains. "The apron times must always be kept to a minimum. Handling on the ground is crucial. Lufthansa Cargo has a clear strategic advantage with the Pharma Hub in Frankfurt".
Experts for temperature sensitive transports.
Boehringer Ingelheim relies on DSV for the end-to-end organization of the transport. "For such transports, we work together with global logistics service providers who have expertise in this field," says Horst Langhammer. One of those experts is Bernhard Woerner, Global Account Director, Health Care at DSV. The logistics provider has been handling transports in the pharmaceutical industry since 2006. "The challenge is precise timing on the ground. The tank is delivered and filled just-in-time in Fremont, California. |
It is placed in the perfectly prepared container and goes straight on its long journey in a refrigerated truck. The truck brings the shipment to the airport in Los Angeles, but waits until the plane has taken off in case of unexpected delays or cancellations. Once it arrives in Frankfurt, the va-Q-tainer MAXx passes through the Lufthansa Cargo Pharma Hub and then again onto a refrigerated truck to be transported directly to Biberach," Woerner explains. "The apron times must always be kept to a minimum. Handling on the ground is crucial. Lufthansa Cargo has a clear strategic advantage with the Pharma Hub in Frankfurt". |
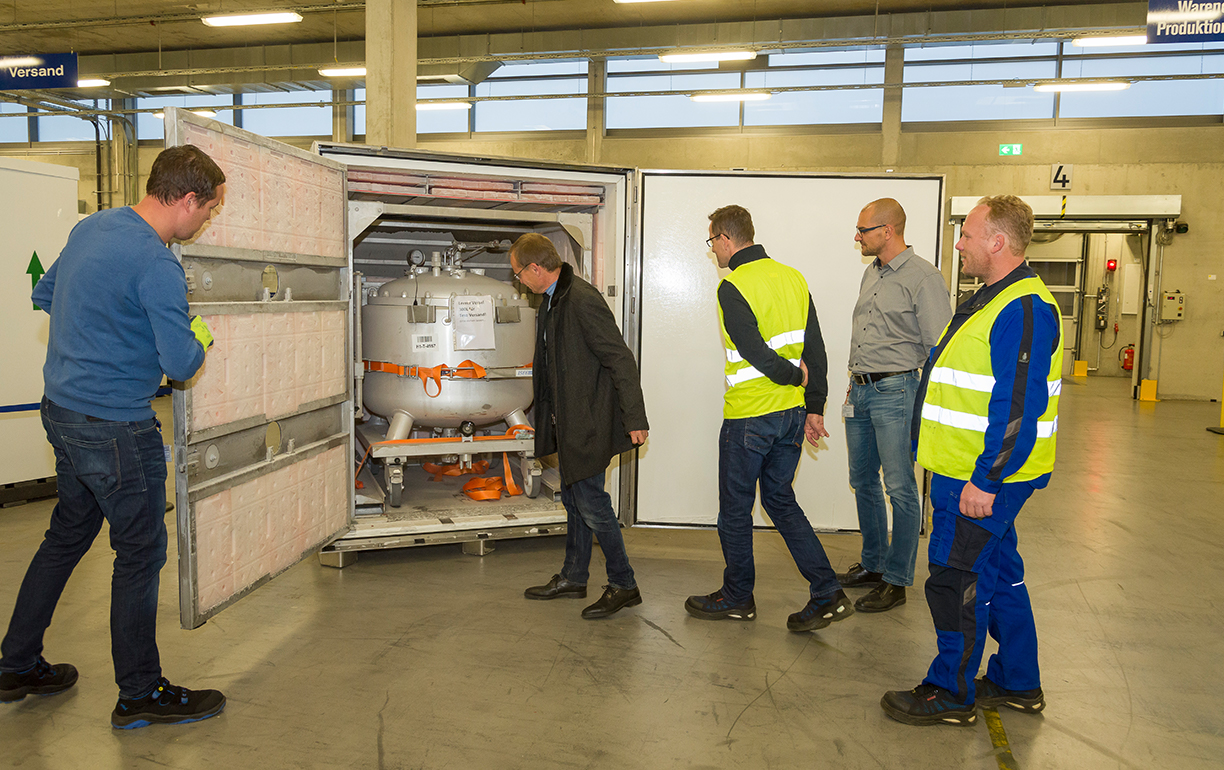
In record time to the container of the future.
The project was not launched until April 2019 and the first test shipment already took off from Los Angeles to Frankfurt in November 2019 - at that time with an empty tank. Another six months later, the active ingredients are now be shipped regularly every two weeks.
"The container is equipped with rechargeable batteries containing a special cooling liquid - so-called Phase Change Material," explains Fabian Eschenbach, Head of the Healthcare & Logistics Division at va-Q-tec. "With these we can guarantee temperatures between -40 and +25°C dry ice free for up to 120 hours even under extreme conditions. With dry ice even -60°C or lower are possible".
Inside the va-Q-tainer MAXx there is space for a universal transport rack to fix the tanks, which was developed, designed and built together by va-Q-tec and a team of Boehringer Ingelheim. It can be adjusted individually for each tank size and reduces the workload when loading the containers with the tanks by 90%. Of course, the container can also be used without this rack releasing some usable space.
Currently there are no providers with a comparable solution. At best, there are self-built products, which of course do not have the decisive standardization, qualification and the simple and cost-efficient handling. Some additional tests must be completed with Boehringer Ingelheim in order for the va-Q-tec containers to be released for other customers as of January 2021.
"The container is equipped with rechargeable batteries containing a special cooling liquid - so-called Phase Change Material," explains Fabian Eschenbach, Head of the Healthcare & Logistics Division at va-Q-tec. "With these we can guarantee temperatures between -40 and +25°C dry ice free for up to 120 hours even under extreme conditions. With dry ice even -60°C or lower are possible". Inside the va-Q-tainer MAXx there is space for a universal transport rack to fix the tanks, which was developed, designed and built together by va-Q-tec and a team of Boehringer Ingelheim. |
It can be adjusted individually for each tank size and reduces the workload when loading the containers with the tanks by 90%. Of course, the container can also be used without this rack releasing some usable space. Currently there are no providers with a comparable solution. At best, there are self-built products, which of course do not have the decisive standardization, qualification and the simple and cost-efficient handling. Some additional tests must be completed with Boehringer Ingelheim in order for the va-Q-tec containers to be released for other customers as of January 2021. |
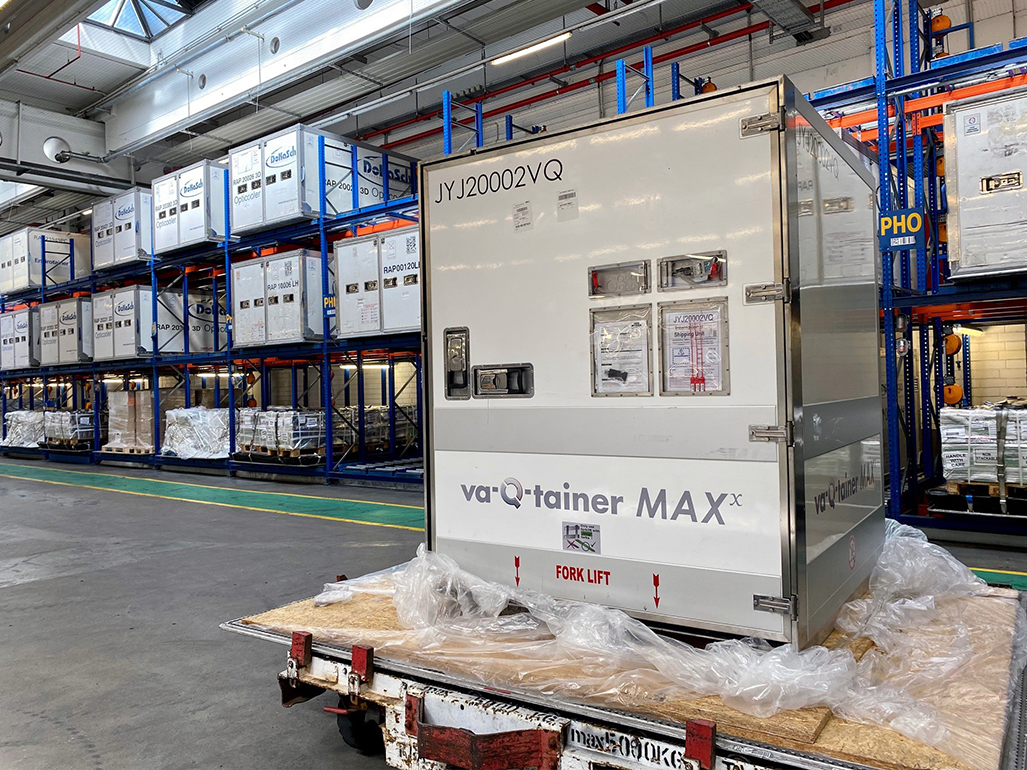
"The container is also a great development for logistics companies. Until now, we had to carry out such transports packed in boxes that were filled with dry ice. These consignments had to be declared as dangerous goods and were highly sensitive to transport damage and loss of active ingredients," explains Mr. Woerner. The damage can be enormous - and not only economically, it could run into millions. In the worst case, patients may not receive their medication or clinical studies could have been postponed. Transporting these products without dry ice has other advantages as well: "From a sustainability perspective, dry ice is no longer state of the art," Woerner explains.
Keeping cool in the crisis.
When the project was in the starting phase, nobody knew about the Corona virus. Since Lufthansa Cargo's freighters continued to fly throughout the crisis, the project could be continued without any delays. "The support provided by our Account Manager Michael Butz was excellent, especially in the turbulent times of crisis. This once again confirmed that we made the right choice," summarizes Bernhard Woerner of DSV.
The Lufthansa Cargo employee himself is also enthusiastic about the project "Being a small part of the wheel in such an innovation is the highlight of our work", and passes the praise on to his colleagues. "All colleagues involved in Germany and the USA contribute their share of service and speed to the success of this project".
Keeping cool in the crisis.
When the project was in the starting phase, nobody knew about the Corona virus. Since Lufthansa Cargo's freighters continued to fly throughout the crisis, the project could be continued without any delays. "The support provided by our Account Manager Michael Butz was excellent, especially in the turbulent times of crisis. This once again confirmed that we made the right choice," summarizes Bernhard Woerner of DSV. |
The Lufthansa Cargo employee himself is also enthusiastic about the project "Being a small part of the wheel in such an innovation is the highlight of our work", and passes the praise on to his colleagues. "All colleagues involved in Germany and the USA contribute their share of service and speed to the success of this project". |
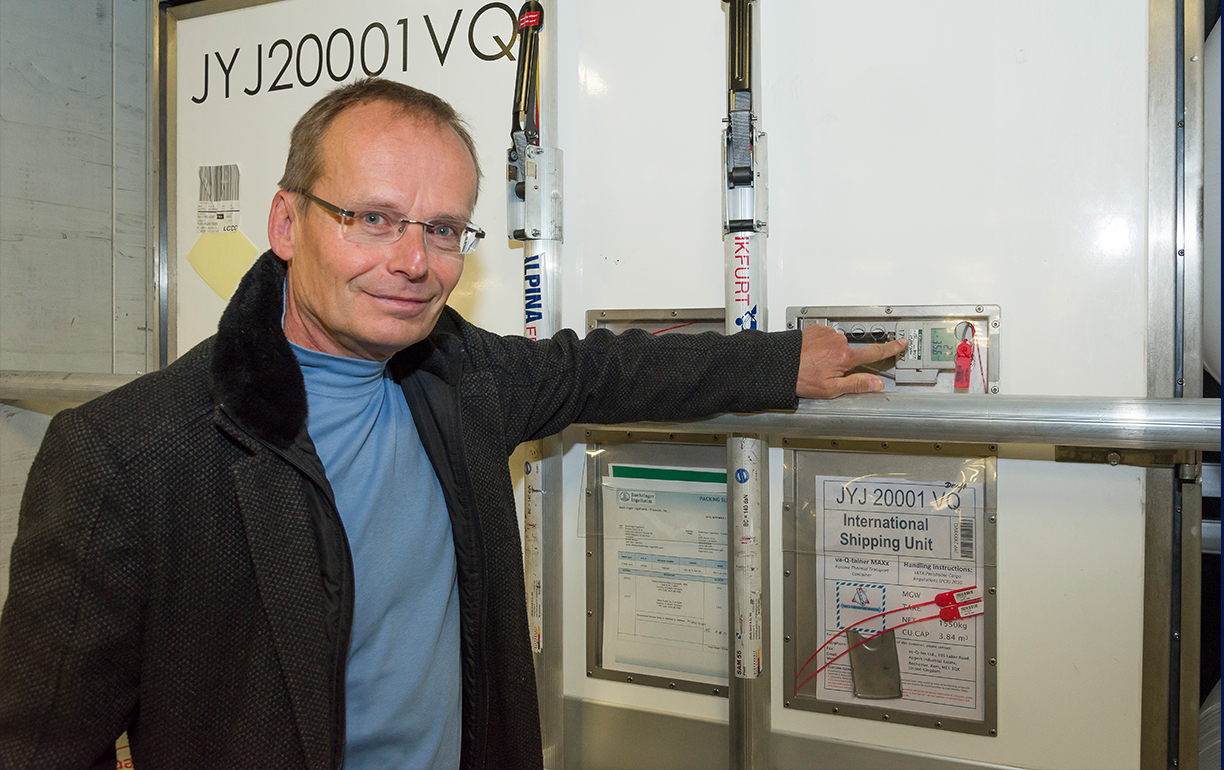
Horst Langhammer is obviously satisfied: After arrival in Biberach, the temperature inside the container is still around minus -36°C.
Photos: Boehringer Ingelheim and Lufthansa Cargo
Photos: Boehringer Ingelheim and Lufthansa Cargo