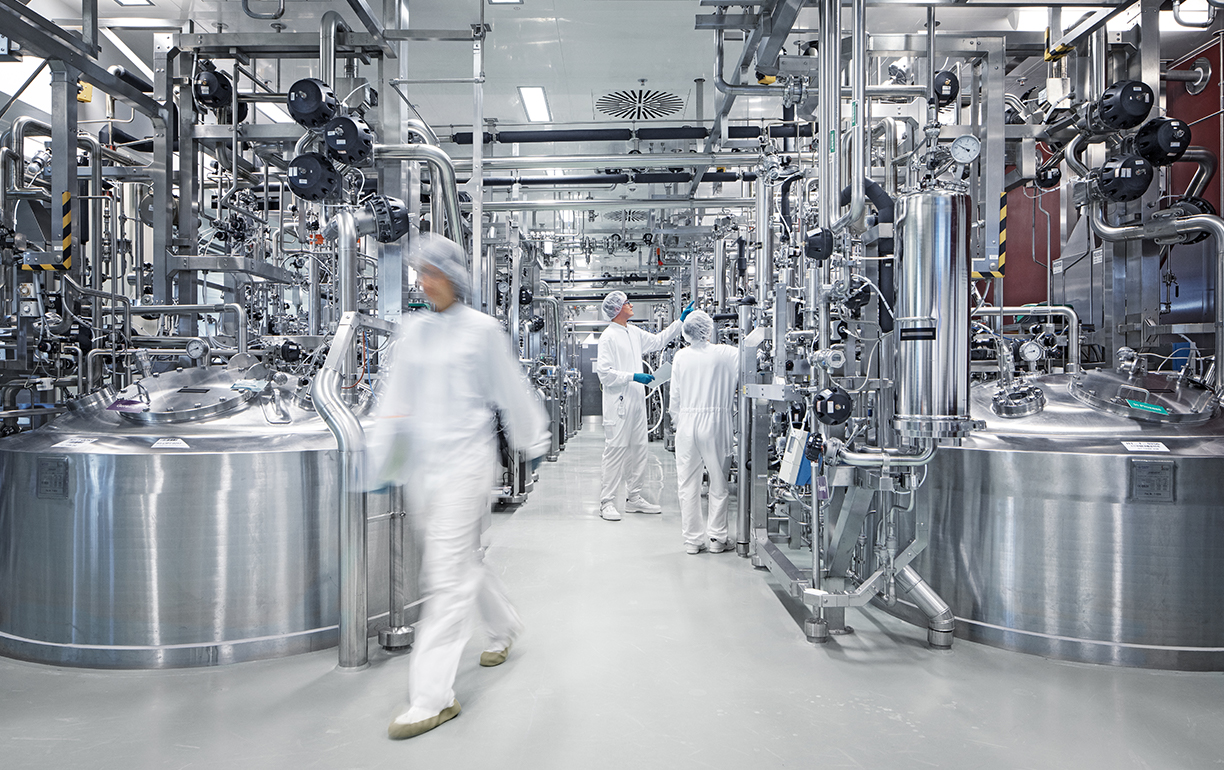
Arktische Temperaturen an Bord.
Auf der Eiskappe Grönlands herrscht im Winter eine Durchschnittstemperatur von -33°C. Kalt, aber nicht kalt genug. Biopharmazie von Boehringer Ingelheim muss bei -40°C transportiert werden und das gleich einmal um den Globus. Doch wie schafft man das fernab der Polkappen? va-Q-tec entwickelte in Zusammenarbeit mit dem Pharmakonzern einen Container, der diese Extremleistung meistert.
Wie ein Spinnennetz verteilen sich die Produktionsstandorte von Boehringer Ingelheim über den Planeten. In Kalifornien, Shanghai und Wien werden biopharmazeutische Rohstoffe hergestellt. „Das kann man sich fast wie Bierbrauen vorstellen“, scherzt Horst Langhammer, Head of Supply Chain Management & Logistic Projects bei Boehringer Ingelheim. „Man bringt die entsprechenden Stoffe in einem Fermenter zusammen und nach dem Gärungsprozess trennt man sie von den Abfallprodukten und erhält hochkonzentrierte Wirkstoffe.“ Nach der Herstellung müssen die Wirkstoffe auf -40°C gekühlt werden. Bei dieser Temperatur findet keine Zellteilung und kein Verfall der Moleküle mehr statt – die Pharmazie befindet sich in einer Art Kryoschlaf. Biberach an der Riß ist der einzige Standort weltweit, der über die speziellen Aufbereitungsanlagen verfügt. Darin wird der Wirkstoff aufgetaut, mit Wasser angereichert und beispielsweise als Antirheumatika in Spritzen abgefüllt.
Wie ein Spinnennetz verteilen sich die Produktionsstandorte von Boehringer Ingelheim über den Planeten. In Kalifornien, Shanghai und Wien werden biopharmazeutische Rohstoffe hergestellt. „Das kann man sich fast wie Bierbrauen vorstellen“, scherzt Horst Langhammer, Head of Supply Chain Management & Logistic Projects bei Boehringer Ingelheim. „Man bringt die entsprechenden Stoffe in einem Fermenter zusammen und nach dem Gärungsprozess trennt man sie von den Abfallprodukten und erhält hochkonzentrierte Wirkstoffe.“ |
Nach der Herstellung müssen die Wirkstoffe auf -40°C gekühlt werden. Bei dieser Temperatur findet keine Zellteilung und kein Verfall der Moleküle mehr statt – die Pharmazie befindet sich in einer Art Kryoschlaf. Biberach an der Riß ist der einzige Standort weltweit, der über die speziellen Aufbereitungsanlagen verfügt. Darin wird der Wirkstoff aufgetaut, mit Wasser angereichert und beispielsweise als Antirheumatika in Spritzen abgefüllt. |
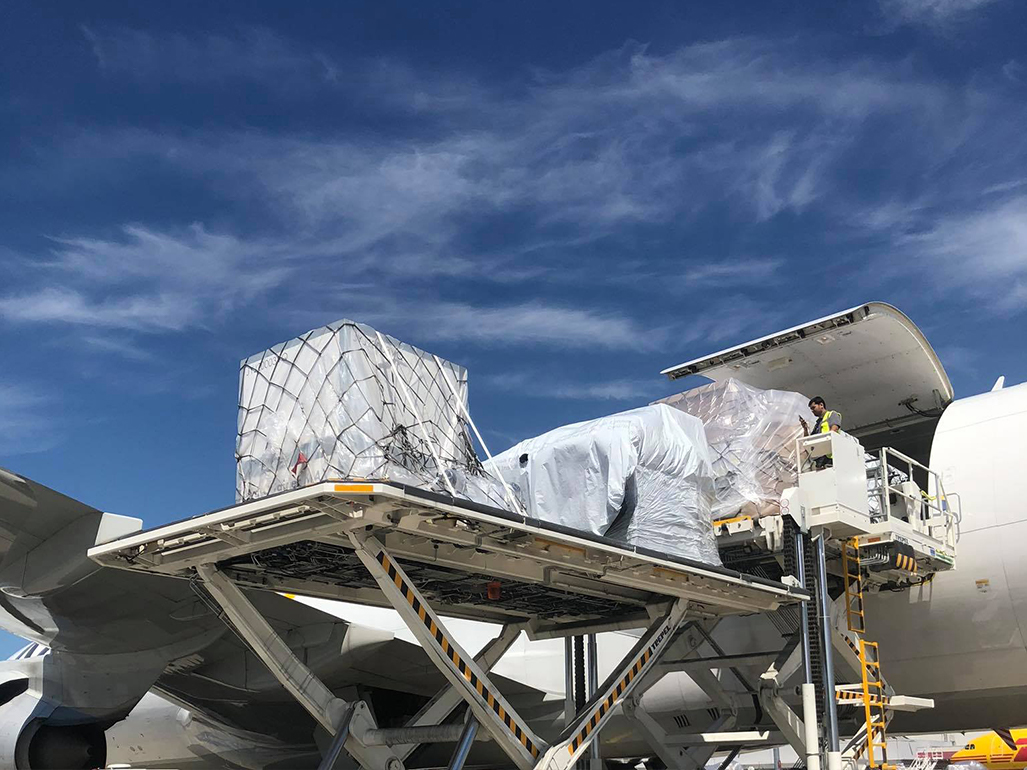
"Where is the airport of Biberach?"
Der Weg aus Amerika oder Asien nach Oberschwaben ist eine Herausforderung, der sich das logistische Team bestehend aus Boehringer Ingelheim, dem Logistiker DSV, Thermoverpackungs-Spezialist va-Q-tec und Lufthansa Cargo gerne stellt.
Langhammer wurde schon häufig von Ortsfremden an den ausländischen Standorten gefragt, wo denn der Flughafen von Biberach sei. Darüber kann der Experte für Supply Chain Management immer noch schmunzeln. Die Stadt mit knapp 35.000 Einwohnern hat tatsächlich einen Flugplatz, auf dem aber nur Flugzeuge bis 5,7t landen dürfen. Eine einzige Sendung der tiefgefrorenen Biopharmazie würde dieses Gewicht schon fast erreichen. Doch der Weg vom Frachter-Drehkreuz in Frankfurt nach Biberach stellt eines der kleinsten Probleme dar. Die Kühlung über insgesamt 80-90 Stunden auf solch niedrigen Temperaturen gestaltet sich schwieriger.
Um diese Herausforderung zu meistern wandte sich Boehringer Ingelheim an va-Q-tec, Pionier hocheffizienter Produkte und Lösungen im Bereich der thermischen Isolation und der temperatur-kontrollierten Logistik. Gemeinsam wurde in Rekordzeit ein neuer Containertyp – der va-Q-tainer MAXx – entwickelt, der die Kühlung von unter -30 °C durch spezielle Temperaturspeicherelemente über mehrere Tage hinweg ohne Stromzufuhr oder die Verwendung von Trockeneis leisten kann. Neben der notwendigen zuverlässigen Temperaturstabilität und der Befestigung des Tanks im Inneren war beispielsweise auch die Höhe des Containers wichtig, um die Pharmazie sicher und ohne aufwendiges Handling zu transportieren. Aufgrund der Höhe des Containers kommt nur ein Transport auf dem Maindeck eines Frachters in Frage. Lufthansa Cargo verbindet Los Angeles mehrmals pro Woche mit einer B777F direkt mit Frankfurt. Die zuverlässigen Verbindungen waren einer der ausschlaggebenden Punkte Lufthansa Cargo zu wählen.
Langhammer wurde schon häufig von Ortsfremden an den ausländischen Standorten gefragt, wo denn der Flughafen von Biberach sei. Darüber kann der Experte für Supply Chain Management immer noch schmunzeln. Die Stadt mit knapp 35.000 Einwohnern hat tatsächlich einen Flugplatz, auf dem aber nur Flugzeuge bis 5,7t landen dürfen. Eine einzige Sendung der tiefgefrorenen Biopharmazie würde dieses Gewicht schon fast erreichen. Doch der Weg vom Frachter-Drehkreuz in Frankfurt nach Biberach stellt eines der kleinsten Probleme dar. Die Kühlung über insgesamt 80-90 Stunden auf solch niedrigen Temperaturen gestaltet sich schwieriger. Um diese Herausforderung zu meistern wandte sich Boehringer Ingelheim an va-Q-tec, Pionier hocheffizienter Produkte und Lösungen im Bereich der thermischen Isolation und der temperatur-kontrollierten Logistik. |
Gemeinsam wurde in Rekordzeit ein neuer Containertyp – der va-Q-tainer MAXx – entwickelt, der die Kühlung von unter -30 °C durch spezielle Temperaturspeicherelemente über mehrere Tage hinweg ohne Stromzufuhr oder die Verwendung von Trockeneis leisten kann. Neben der notwendigen zuverlässigen Temperaturstabilität und der Befestigung des Tanks im Inneren war beispielsweise auch die Höhe des Containers wichtig, um die Pharmazie sicher und ohne aufwendiges Handling zu transportieren. Aufgrund der Höhe des Containers kommt nur ein Transport auf dem Maindeck eines Frachters in Frage. Lufthansa Cargo verbindet Los Angeles mehrmals pro Woche mit einer B777F direkt mit Frankfurt. Die zuverlässigen Verbindungen waren einer der ausschlaggebenden Punkte Lufthansa Cargo zu wählen. |
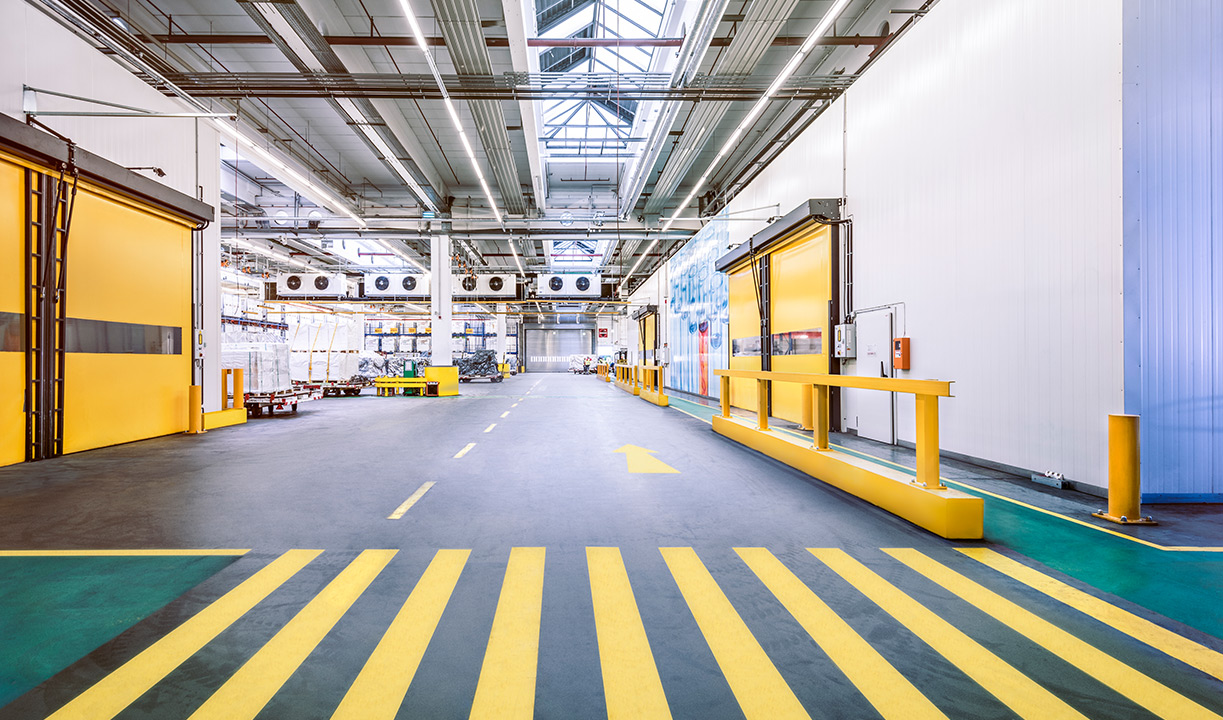
Der 2011 eröffnete Pharma Hub am Flughafen Frankfurt bietet auf über 8000qm Fläche präzise Temperaturkontrolle, Abfertigung durch ausgewiesene Experten und durch die direkte Lage am Vorfeld kurze Transportwege.
Experten für temperatursensitive Transporte.
Bei der End-to-End Organisation des Transports verlässt sich Boehringer Ingelheim auf DSV. „Bei solchen Transporten arbeiten wir mit globalen Logistikdienstleistern zusammen, die Expertise auf diesem Feld haben“, erzählt Horst Langhammer. Einer dieser Experten ist Bernhard Woerner, Global Account Director, Health Care bei DSV. Seit 2006 kümmert sich der Logistiker um Transporte in der Pharmabranche. „Die Herausforderung ist die genaue Taktung am Boden. Der Tank wird just-in-time in Fremont, Kalifornien, angeliefert und befüllt. Er kommt in den optimal vorbereiteten Container und geht direkt in einem Kühltruck auf die große Reise. Dieser bringt die Sendung an den Flughafen in Los Angeles, aber bleibt stehen bis das Flugzeug abgeflogen ist, falls es zu unerwarteten Verspätungen oder Ausfällen kommt. In Frankfurt angekommen, geht der va-Q-tainer MAXx durch den Lufthansa Cargo Pharma Hub und dann erneut auf einen Kühltruck, um direkt nach Biberach transportiert zu werden“, erzählt Woerner. „Die Vorfeld-Zeiten müssen immer entsprechend kurzgehalten werden. Die Abfertigung am Boden ist entscheidend. Lufthansa Cargo hat mit dem Pharma Hub in Frankfurt einen klaren strategischen Vorteil.“
Experten für temperatursensitive Transporte.
Bei der End-to-End Organisation des Transports verlässt sich Boehringer Ingelheim auf DSV. „Bei solchen Transporten arbeiten wir mit globalen Logistikdienstleistern zusammen, die Expertise auf diesem Feld haben“, erzählt Horst Langhammer. Einer dieser Experten ist Bernhard Woerner, Global Account Director, Health Care bei DSV. Seit 2006 kümmert sich der Logistiker um Transporte in der Pharmabranche. „Die Herausforderung ist die genaue Taktung am Boden. Der Tank wird just-in-time in Fremont, Kalifornien, angeliefert und befüllt. Er kommt in den optimal vorbereiteten Container und geht direkt in einem Kühltruck auf die große Reise. |
Dieser bringt die Sendung an den Flughafen in Los Angeles, aber bleibt stehen bis das Flugzeug abgeflogen ist, falls es zu unerwarteten Verspätungen oder Ausfällen kommt. In Frankfurt angekommen, geht der va-Q-tainer MAXx durch den Lufthansa Cargo Pharma Hub und dann erneut auf einen Kühltruck, um direkt nach Biberach transportiert zu werden“, erzählt Woerner. „Die Vorfeld-Zeiten müssen immer entsprechend kurzgehalten werden. Die Abfertigung am Boden ist entscheidend. Lufthansa Cargo hat mit dem Pharma Hub in Frankfurt einen klaren strategischen Vorteil.“ |
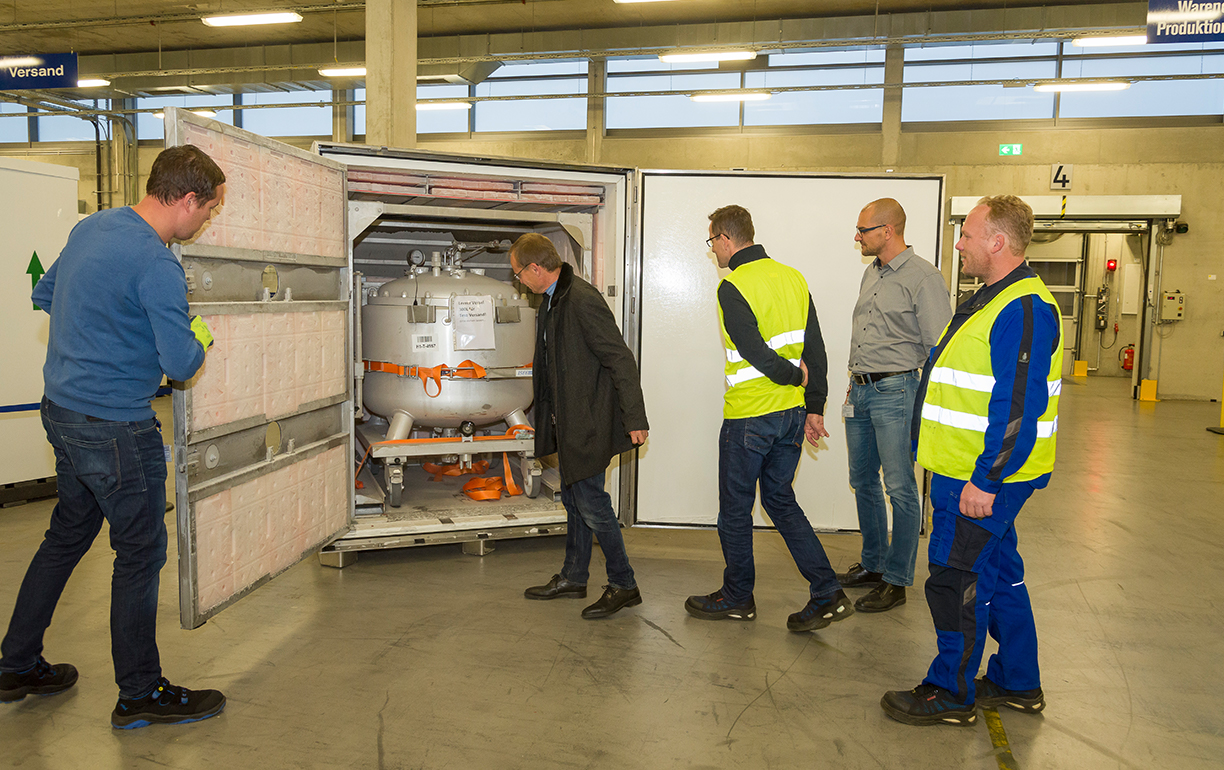
In Rekordzeit zum Zukunfts-Container.
Erst im April 2019 fiel der Startschuss zum Projekt und bereits im November 2019 hob die erste Testsendung von Los Angeles nach Frankfurt ab – damals noch mit einem leeren Tank. Noch einmal ein halbes Jahr später und die Wirkstoffe treten diesen Weg nun regelmäßig alle zwei Wochen an.
„Der Container ist mit Akkus bestückt, die eine spezielle Kühlflüssigkeit enthalten – sogenanntem Phase Change Material,“ erläutert Fabian Eschenbach, Leiter des Geschäftsbereichs Healthcare & Logistics bei va-Q-tec. „Mit diesen können wir Temperaturen zwischen -40 und +25°C trockeneisfrei über eine Dauer von bis zu 120 Stunden auch unter extremen Bedingungen gewährleisten. Mit Trockeneis sind sogar -60°C oder tiefer möglich.“
Im Inneren des va-Q-tainer MAXx findet ein universelles Transportgestell zur Fixierung der Tanks Platz, das gemeinsam von va-Q-tec und einem Team von Boehringer Ingelheim entwickelt, konstruiert und gebaut wurde. Es lässt sich individuell für jede Tankgröße einstellen und reduziert den Arbeitsaufwand beim Beladen der Container mit den Tanks um 90%. Natürlich kann der Container auch ohne dieses Gestell genutzt werden und bietet dann mehr Platz.
Aktuell gibt es keine Anbieter mit einer vergleichbaren Lösung. Es gibt allenfalls Selbstbauten, die natürlich nicht über die entscheidende Standardisierung, Qualifizierung und das einfache sowie kosteneffiziente Handling verfügen. Nach den abgeschlossenen Tests mit Boehringer Ingelheim wird der Container von va-Q-tec voraussichtlich ab Januar 2021 auch für andere Kunden zu Verfügung stehen.
„Der Container ist mit Akkus bestückt, die eine spezielle Kühlflüssigkeit enthalten – sogenanntem Phase Change Material,“ erläutert Fabian Eschenbach, Leiter des Geschäftsbereichs Healthcare & Logistics bei va-Q-tec. „Mit diesen können wir Temperaturen zwischen -40 und +25°C trockeneisfrei über eine Dauer von bis zu 120 Stunden auch unter extremen Bedingungen gewährleisten. Mit Trockeneis sind sogar -60°C oder tiefer möglich.“ Im Inneren des va-Q-tainer MAXx findet ein universelles Transportgestell zur Fixierung der Tanks Platz, das gemeinsam von va-Q-tec und einem Team von Boehringer Ingelheim entwickelt, konstruiert und gebaut wurde. |
Es lässt sich individuell für jede Tankgröße einstellen und reduziert den Arbeitsaufwand beim Beladen der Container mit den Tanks um 90%. Natürlich kann der Container auch ohne dieses Gestell genutzt werden und bietet dann mehr Platz. Aktuell gibt es keine Anbieter mit einer vergleichbaren Lösung. Es gibt allenfalls Selbstbauten, die natürlich nicht über die entscheidende Standardisierung, Qualifizierung und das einfache sowie kosteneffiziente Handling verfügen. Nach den abgeschlossenen Tests mit Boehringer Ingelheim wird der Container von va-Q-tec voraussichtlich ab Januar 2021 auch für andere Kunden zu Verfügung stehen. |
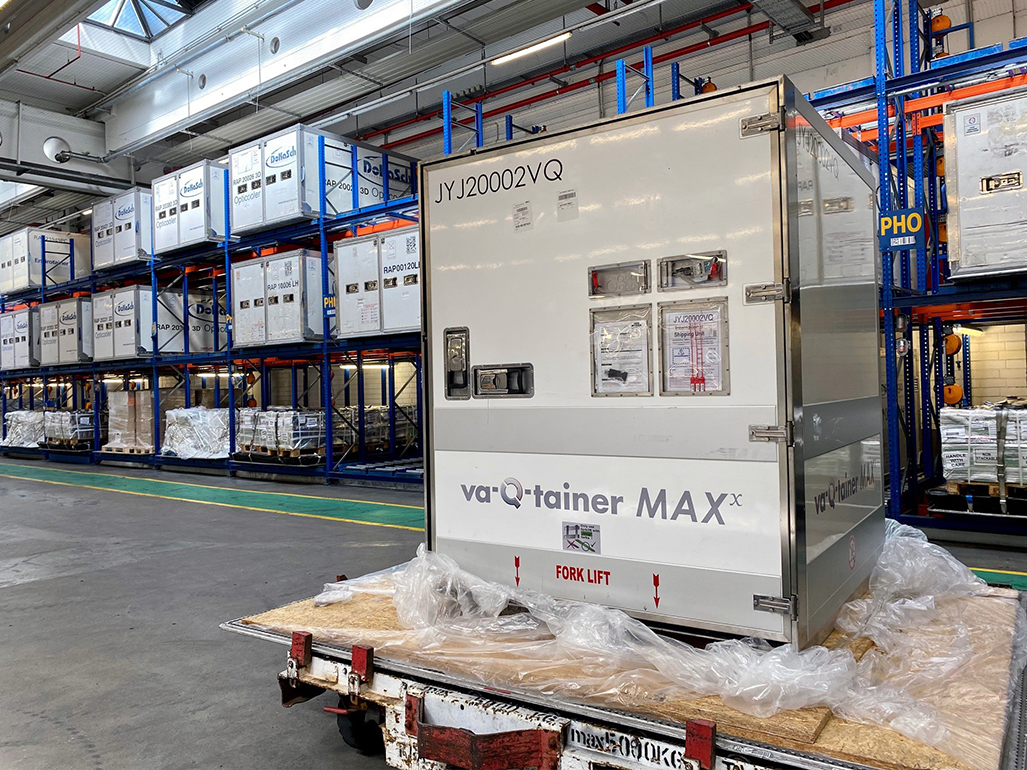
„Der Container ist auch für Logistiker eine tolle Entwicklung. Bisher mussten wir solche Transporte mit Transportboxen durchführen, die mit Trockeneis bestückt waren. Diese Sendungen müssen dann aber als Gefahrgut deklariert werden, haben eine hohe Anfälligkeit für Transportschäden und Wirkstoffverluste“, erläutert Herr Woerner. Die Schäden können gewaltig sein – nicht nur wirtschaftlich gehen diese dann in die Millionenhöhe. Im schlimmsten Fall erhalten Patienten nicht ihre Medikamente oder klinische Studien müssen verschoben werden. Der Verzicht auf Trockeneis hat noch weitere Pluspunkte: „Aus Sicht der Nachhaltigkeit ist Trockeneis nicht mehr der neueste Stand der Dinge“, führt Woerner aus.
Einen kühlen Kopf in der Krise bewahren.
Als das Projekt in den Startlöchern stand, kannte noch keiner das Corona-Virus. Da die Frachter von Lufthansa Cargo in der Krise durchgehend weiterfliegen, konnte das Projekt ohne Verzug fortgeführt werden. „Die Betreuung durch unseren Account Manager Michael Butz war auch gerade in der turbulenten Krisenzeit ausgezeichnet. Das hat uns noch einmal bestätigt die richtige Wahl getroffen zu haben“, resümiert auch Bernhard Woerner von DSV.
Auch der Lufthansa Cargo Mitarbeiter selbst ist vom Projekt begeistert „Bei so einer Innovation ein kleiner Teil des Rads zu sein, sind die Höhepunkte unserer Arbeit“, und gibt das Lob an seine Kollegen weiter. „Alle involvierten Kolleginnen und Kollegen in Deutschland und in den USA tragen ihren Teil an Service und Geschwindigkeit zum Gelingen des Transports bei.“
Einen kühlen Kopf in der Krise bewahren.
Als das Projekt in den Startlöchern stand, kannte noch keiner das Corona-Virus. Da die Frachter von Lufthansa Cargo in der Krise durchgehend weiterfliegen, konnte das Projekt ohne Verzug fortgeführt werden. „Die Betreuung durch unseren Account Manager Michael Butz war auch gerade in der turbulenten Krisenzeit ausgezeichnet. Das hat uns noch einmal bestätigt die richtige Wahl getroffen zu haben“, resümiert auch Bernhard Woerner von DSV. |
Auch der Lufthansa Cargo Mitarbeiter selbst ist vom Projekt begeistert „Bei so einer Innovation ein kleiner Teil des Rads zu sein, sind die Höhepunkte unserer Arbeit“, und gibt das Lob an seine Kollegen weiter. „Alle involvierten Kolleginnen und Kollegen in Deutschland und in den USA tragen ihren Teil an Service und Geschwindigkeit zum Gelingen des Transports bei.“ |
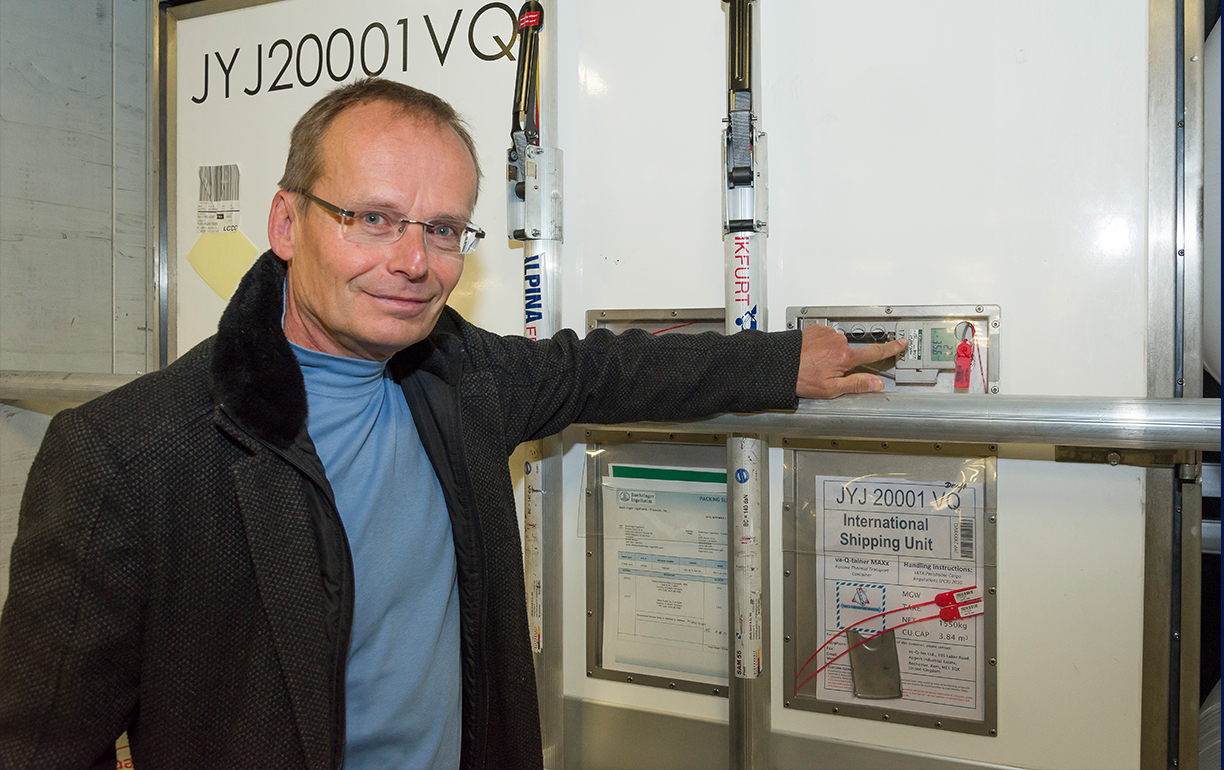
Horst Langhammer ist sichtlich zufrieden: Nach der Ankunft in Biberach liegt die Temperatur im Inneren des Containers immer noch bei etwa minus 36 Grad.
Fotos: Boehringer Ingelheim und Lufthansa Cargo
Fotos: Boehringer Ingelheim und Lufthansa Cargo