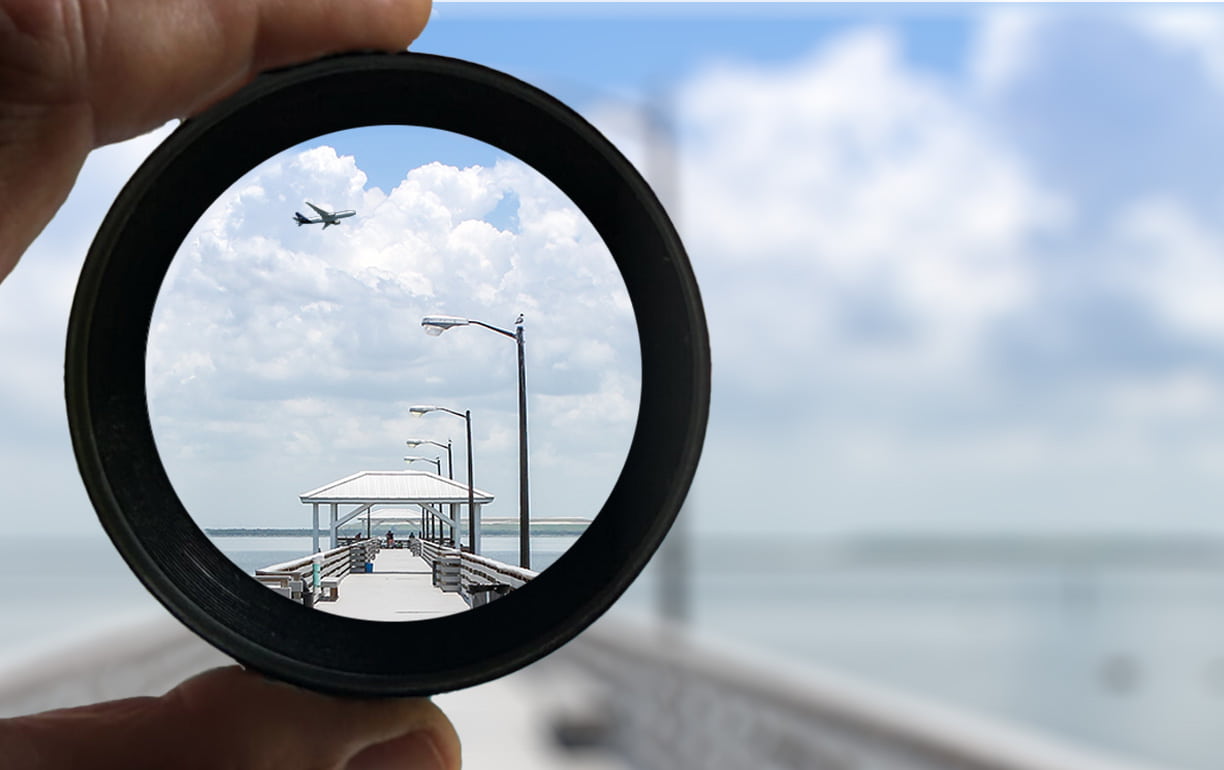
Restoring sight across oceans: How the Lions World Vision Institute and Lufthansa Cargo deliver the gift of sight
Every day, somewhere in the world, someone opens their eyes to a new beginning—thanks to a gift they never expected to receive. Behind that moment of clarity is a global network of compassion, precision, and logistics. At the heart of this network is the Lions World Vision Institute (LWVI) and its Ocular Distribution Manager Lady Salinas.
This is the story of how corneal tissue travels across oceans and continents, how lives are transformed, and logistic teams around the world are all connected by a single, powerful mission – so the world can see.
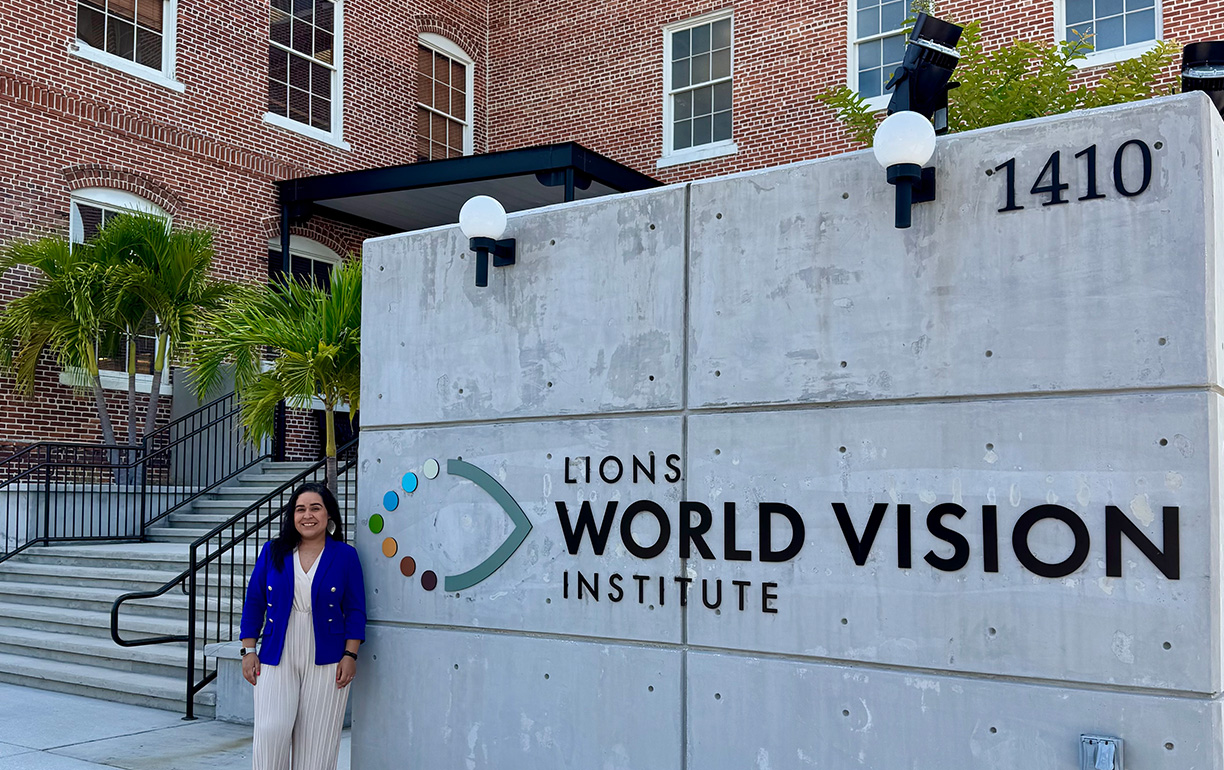
A mission of sight
Lady Salinas and her team’s day often begins before sunrise. The inbox of the Ocular Distribution Manager is filled with updates from around the world – surgeons requesting tissue, donor families confirming consent, and logistics teams coordinating shipments. “Every shipment is a story,” Lady says. “A donor’s legacy, a recipient’s hope, and a team’s commitment to making it happen.”
Lady Salinas oversees the placement of corneal tissue in over 70 countries and 25 U.S. states. Her role is part logistics, part diplomacy, and all heart. “Every day presents a new opportunity to make a difference,” she says. “What fascinates me most is guiding our coordinators in quickly fulfilling the overwhelming demand for these special gifts and honoring the wishes of countless donors.”
The Lions World Vision Institute has a global network of eye banks, medical professionals, researchers, and community-based initiatives. It restores vision to more than 20,000 men, women, and children annually who suffer from corneal blindness or low vision. Their work spans continents, cultures, and time zones – but it all begins with a single, selfless act: donation.
From loss to legacy
One of the donors is Andrew Dorsey. Andrew was just 27 when he passed away. Known for his kindness and compassion, Andrew had a way of making everyone feel like they belonged. His mother, Shebna, found comfort in knowing that Andrew’s generosity would live on through organ, eye, and tissue donation.
“Andrew would have given someone his arm if he thought it would help,” she says with a bittersweet smile. His corneas were donated through LWVI, restoring sight to two individuals living with blinding eye diseases. Today, Shebna continues to advocate for donation, spreading Andrew’s legacy and encouraging others to be “Dorsey Strong.”
The donation process is a race against time: Once a donor passes, the process begins immediately. The Donor Services Department of LWVI is notified by the hospital. An ocular technician is dispatched to recover the corneal tissue, often within hours. Eye and tissue donation allows up to 24 hours, best within 12 hours of death and corneas must be transplanted within 14 days of recovery, and every hour counts.
From loss to legacy
One of the donors is Andrew Dorsey. Andrew was just 27 when he passed away. Known for his kindness and compassion, Andrew had a way of making everyone feel like they belonged. His mother, Shebna, found comfort in knowing that Andrew’s generosity would live on through organ, eye, and tissue donation. “Andrew would have given someone his arm if he thought it would help,” she says with a bittersweet smile. His corneas were donated through LWVI, restoring sight to two individuals living with blinding eye diseases. |
Today, Shebna continues to advocate for donation, spreading Andrew’s legacy and encouraging others to be “Dorsey Strong.” The donation process is a race against time: Once a donor passes, the process begins immediately. The Donor Services Department of LWVI is notified by the hospital. An ocular technician is dispatched to recover the corneal tissue, often within hours. Eye and tissue donation allows up to 24 hours, best within 12 hours of death and corneas must be transplanted within 14 days of recovery, and every hour counts.
|

The recovered tissue is brought to LWVI’s facility, where it undergoes a rigorous evaluation. Technicians assess the graft’s health, clarity, and suitability for transplant. Meanwhile, the Donor Eligibility Team gathers medical records, interviews family members, and completes risk assessments to ensure the tissue is safe for use. Though the timing can be difficult, many families find comfort in knowing their loved one’s legacy lives on through the healing power of donation. These donations can restore sight to up to two people and heal over 75 others through corneas, skin, bone, heart valves, and more.
Once cleared, the tissue is released for transplant. Now, the Distribution Team steps in to fulfill the request from a surgeon on behalf of their patient and coordinate with the technicians in the Ocular Processing Lab to prepare the cornea for specific surgical procedures. This is where Lady Salinas and her team shine – matching tissue with patients around the world, often in remote or underserved communities.
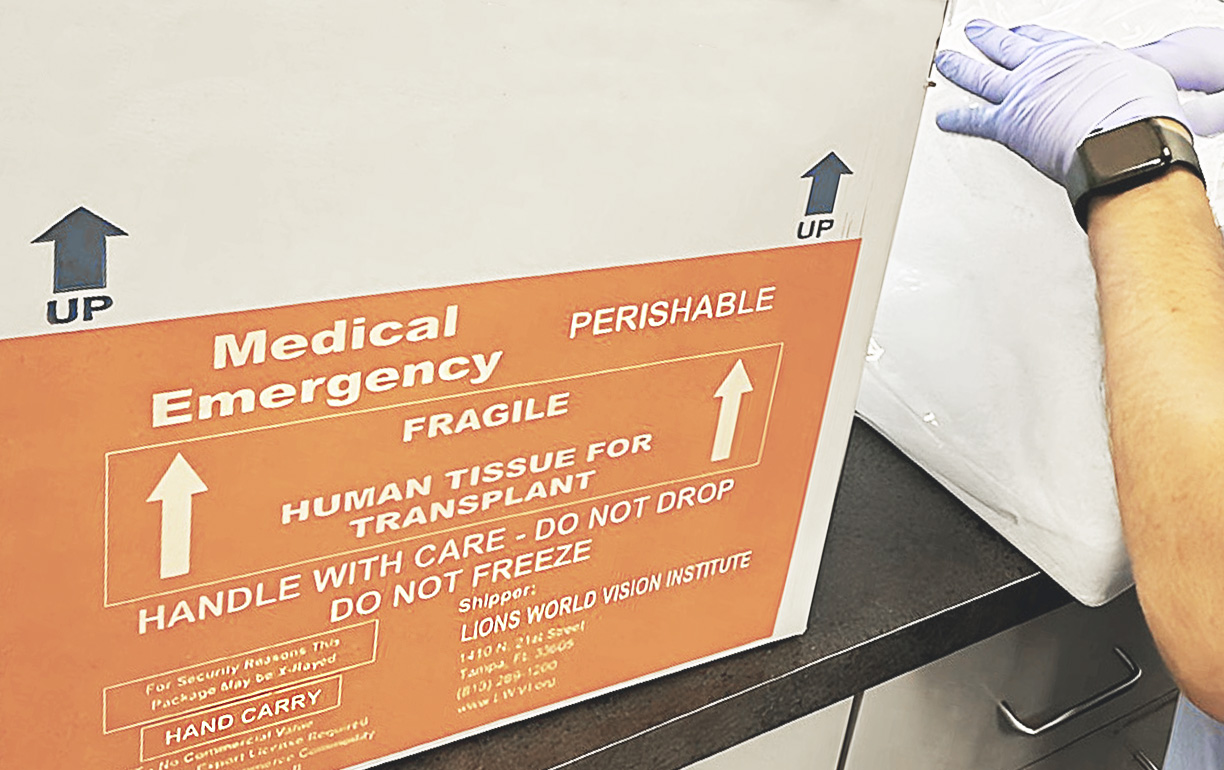
Precision logistics
When a recipient is identified and surgery is scheduled, the next challenge is getting the tissue there – fast, safely, and under strict conditions. The tissue is packed in a validated cooler with a 90-hour lifespan and has to be transported within the temperature range of 2-8C°. The cooler is delivered directly from Lions World Vision Institute, who is a known shipper, to Lufthansa Cargo’s facility.
Lufthansa Cargo’s role begins the moment a booking is made, and the carrier has become an indispensable partner for the Lions World Vision Institute. “Lufthansa Cargo is our number one courier,” Lady Salinas says. “Their dedication and reliable service make them stand out. They understand the sensitivity of our shipments and treat them with the utmost care.”
The Lufthansa Cargo team ensures:
• Priority handling: Human corneal tissue is booked as LHO (Living Human Organ) and classified as time-critical cargo flown with Lufthansa Cargos Speed td.Flash. Customers receive an immediate booking confirmation within the scope of our Capacity Guarantee enabling a guaranteed access to capacity on short notice. The shipment receives the highest priority and fastest handling times at every stage of the journey. In Frankfurt for example, our Valuables team send special handling colleagues directly to the aircraft to handle the transfers.
• Real-time tracking: The coordinators receive live updates on the shipment’s location and estimated arrival time, allowing the involved medical professionals to schedule surgeries with precision. The 24/7 td.Flash Tracking Support Service is there for questions on current shipments.
• Rapid rebooking: In the rare event of a delay, Lufthansa Cargo provides immediate notifications and prioritizes the rebooking of the shipment on the next available flight – often within hours.
Most shipments go out of Tampa, Florida, where the Lions World Vision Institute has its headquarters, and which is connected daily and directly to Lufthansa Cargo’s main hub in Frankfurt. But there are more options from Florida like Orlando to Munich, or Miami to Brussels. From there, the journey continues to one of 350 global stations like Narita, Riyadh or Yaounde before reaching its final destination, sometimes the smallest communities around the world.
Yaounde in Cameroon was also the destination of a special donation. It might sound very remote for some, but Lufthansa Cargo connects Yaounde Nsimalen Airport, as well as the Cameroon city Douala several times a week via Brussels Airlines with Brussel, one of their five hubs in Europe. And no matter the region, trained staff handle medical shipments with care and urgency. Whether it’s a rural clinic in Africa or a major hospital in Southeast Asia, Lufthansa Cargo ensures that the gift of sight arrives on time and intact.
Lufthansa Cargo’s role begins the moment a booking is made, and the carrier has become an indispensable partner for the Lions World Vision Institute. “Lufthansa Cargo is our number one courier,” Lady Salinas says. “Their dedication and reliable service make them stand out. They understand the sensitivity of our shipments and treat them with the utmost care.” The Lufthansa Cargo team ensures:
|
Most shipments go out of Tampa, Florida, where the Lions World Vision Institute has its headquarters, and which is connected daily and directly to Lufthansa Cargo’s main hub in Frankfurt. But there are more options from Florida like Orlando to Munich, or Miami to Brussels. From there, the journey continues to one of 350 global stations like Narita, Riyadh or Yaounde before reaching its final destination, sometimes the smallest communities around the world. Yaounde in Cameroon was also the destination of a special donation. It might sound very remote for some, but Lufthansa Cargo connects Yaounde Nsimalen Airport, as well as the Cameroon city Douala several times a week via Brussels Airlines with Brussel, one of their five hubs in Europe. And no matter the region, trained staff handle medical shipments with care and urgency. Whether it’s a rural clinic in Africa or a major hospital in Southeast Asia, Lufthansa Cargo ensures that the gift of sight arrives on time and intact.
|
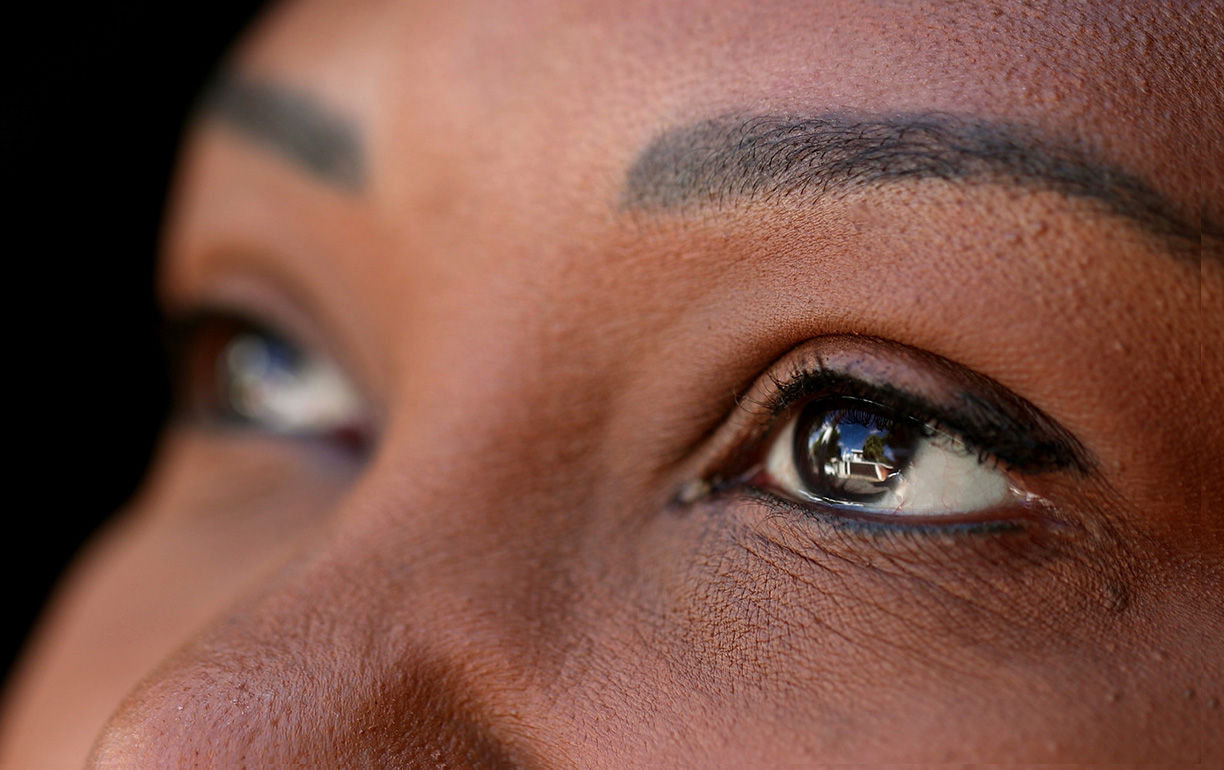
Vision restored
On the receiving end of the journey there are people like Anne Ngo Moug. The mother from Cameroon, began losing vision in one eye shortly after giving birth. The thought of not being able to watch her children grow up was devastating. Anne was connected with the Lions World Vision Institute to help restore her vision. The international team of LWVI worked tirelessly with ophthalmologists to find a surgeon connected with their network and together, the Lions World Vision Institute was able to donate a cornea free of charge to help the new mother see again.
Anne recounts that she couldn’t believe how fast the cornea was ready for transplant after Lions World Vision Institute connected her with the surgeon in Kenya. “I couldn’t believe how fast the cornea was ready,” Anne recalls. “Before the surgery, I could barely see the letters on a page. Now, I can read even the smallest print.” Shortly after her surgery, Anne discovered she was pregnant again. “Hope is a strong word,” she says. “I experienced hope in your gift to me that my household will never forget.”
The Lions World Vision Institute has helped more than 500,000 men, women and children around the world receiving the life-transformative gift of sight. During their long-lasting partnership Lufthansa Cargo has transported more than 10,000 for the Lions World Vision Institute and shipments can contain up to 20 different corneas. From pediatric patients in India to elderly farmers in Honduras, the impact is profound and far-reaching. Together Lions World Vision Institute and Lufthansa Cargo, are not just transporting corneas; they are delivering hope, and the chance to see a brighter future.
As Lady Salinas puts it, “It’s truly a privilege to be part of this mission. Together, we are transforming lives so the world can see.”
The Lions World Vision Institute has helped more than 500,000 men, women and children around the world receiving the life-transformative gift of sight. During their long-lasting partnership Lufthansa Cargo has transported more than 10,000 for the Lions World Vision Institute and shipments can contain up to 20 different corneas. |
From pediatric patients in India to elderly farmers in Honduras, the impact is profound and far-reaching. Together Lions World Vision Institute and Lufthansa Cargo, are not just transporting corneas; they are delivering hope, and the chance to see a brighter future. As Lady Salinas puts it, “It’s truly a privilege to be part of this mission. Together, we are transforming lives so the world can see.”
|
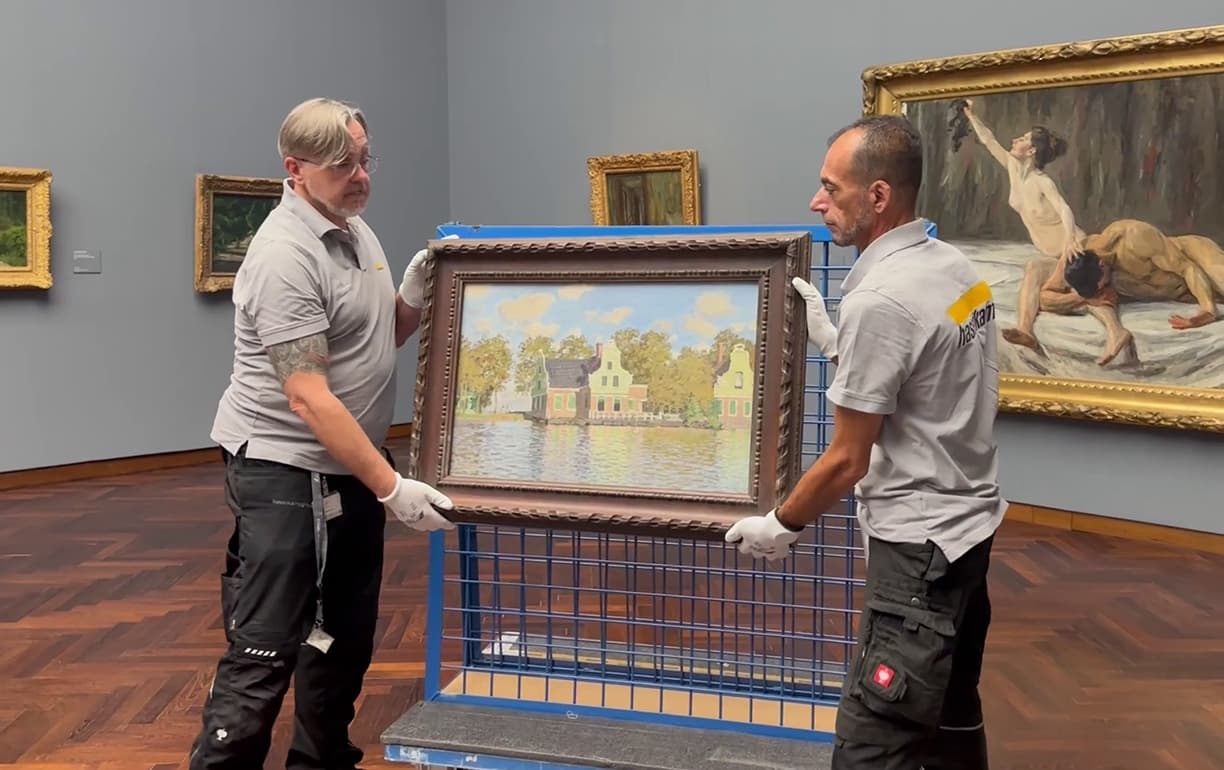
A masterpiece on tour: Monet travels to Japan
A painting by the famous artist Claude Monet is going on a long journey to Japan from the Städel Museum in Frankfurt am Main – via Frankfurt Airport, of course.
You can watch on this project on the YouTube channel of Lufthansa Cargo.
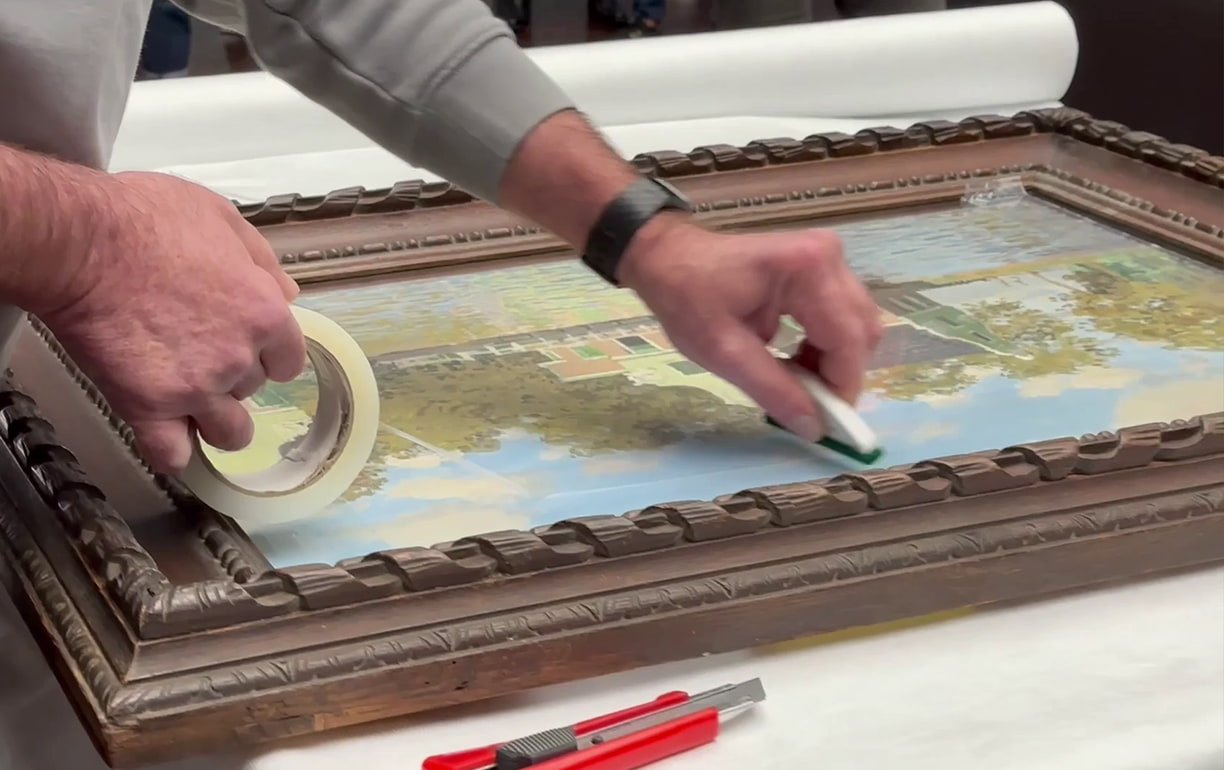
Transporting the priceless painting first requires careful packaging on site, which requires a great deal of sensitivity. “First, we tape the painting to protect the glass surface. Then we wrap it in acid-free packaging material and place it in a special crate for transporting paintings,” explains Mr. Simon Leps, Art Logistics Expert from Hasenkamp Logistik GmbH.
The painting will be loaned to museums in Tokyo and Osaka as part of a worldwide art exchange. This is also made possible by the proximity to the airport. “Houses by the Bank of the River Zaan” is the title of the painting, which is described as idyllic and carefree. An idyll that needs special protection when traveling. "The box is specially insulated with several layers. It is fireproof and designed to maintain the climate over a relatively long period of time," says Simon Leps from Hasenkamp.
The painting will be loaned to museums in Tokyo and Osaka as part of a worldwide art exchange. This is also made possible by the proximity to the airport. “Houses by the Bank of the River Zaan” is the title of the painting, which is described as idyllic and carefree. |
An idyll that needs special protection when traveling. "The box is specially insulated with several layers. It is fireproof and designed to maintain the climate over a relatively long period of time," says Simon Leps from Hasenkamp.
|
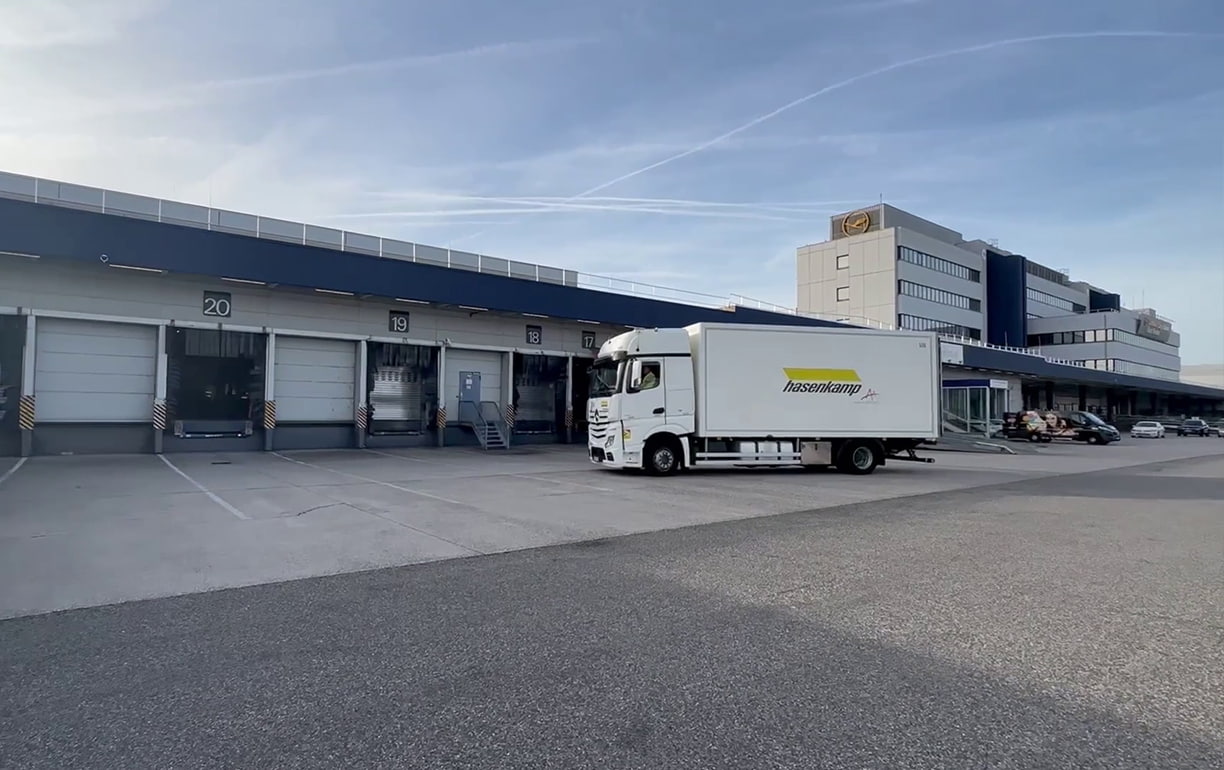
The next step is to transport the Monet to Lufthansa Cargo at Frankfurt Airport. There, the so-called Art Cube is available for storing paintings and works of art from around the world. The 155-square-meter space features the highest security measures, combined with optimal handling processes and its own art handling staff. The modern technical facilities, including a ventilation system with heating and cooling function, which enables targeted temperature control via a VRV air-conditioning control system, ensures that the works of art can be stored under optimal climatic conditions, regardless of the outside temperature. Access to the special storage facility is controlled and monitored by sensitive security technology.
“Monet's journey has a special meaning for our company, because Fraport has been supporting the Städel Museum and many other art institutions for many years,” says Alexandra Zimpelmann, Head of Political Communication, Sponsoring and Regional Funding from Fraport AG. ”Monet's journey allows us to understand how international art is. At the same time, we see how valuable art is for the attractiveness of a region. And that is why we are happy to support and sponsor many cultural institutions here in the region and, of course, the Städel.”
The painting is successfully palletized at Lufthansa Cargo. That evening, the Monet, along with several other works of art, is loaded onto the aircraft and begins its journey overseas. The “Houses by the Bank of the River Zaan” will return to Germany and the Städel Museum before the end of this year. Until then, we wish Monet a safe journey and a pleasant stay.
“Monet's journey has a special meaning for our company, because Fraport has been supporting the Städel Museum and many other art institutions for many years,” says Alexandra Zimpelmann, Head of Political Communication, Sponsoring and Regional Funding from Fraport AG. ”Monet's journey allows us to understand how international art is. At the same time, we see how valuable art is for the attractiveness of a region. And that is why we are happy to support and sponsor many cultural institutions here in the region and, of course, the Städel.” |
The painting is successfully palletized at Lufthansa Cargo. That evening, the Monet, along with several other works of art, is loaded onto the aircraft and begins its journey overseas. The “Houses by the Bank of the River Zaan” will return to Germany and the Städel Museum before the end of this year. Until then, we wish Monet a safe journey and a pleasant stay.
|
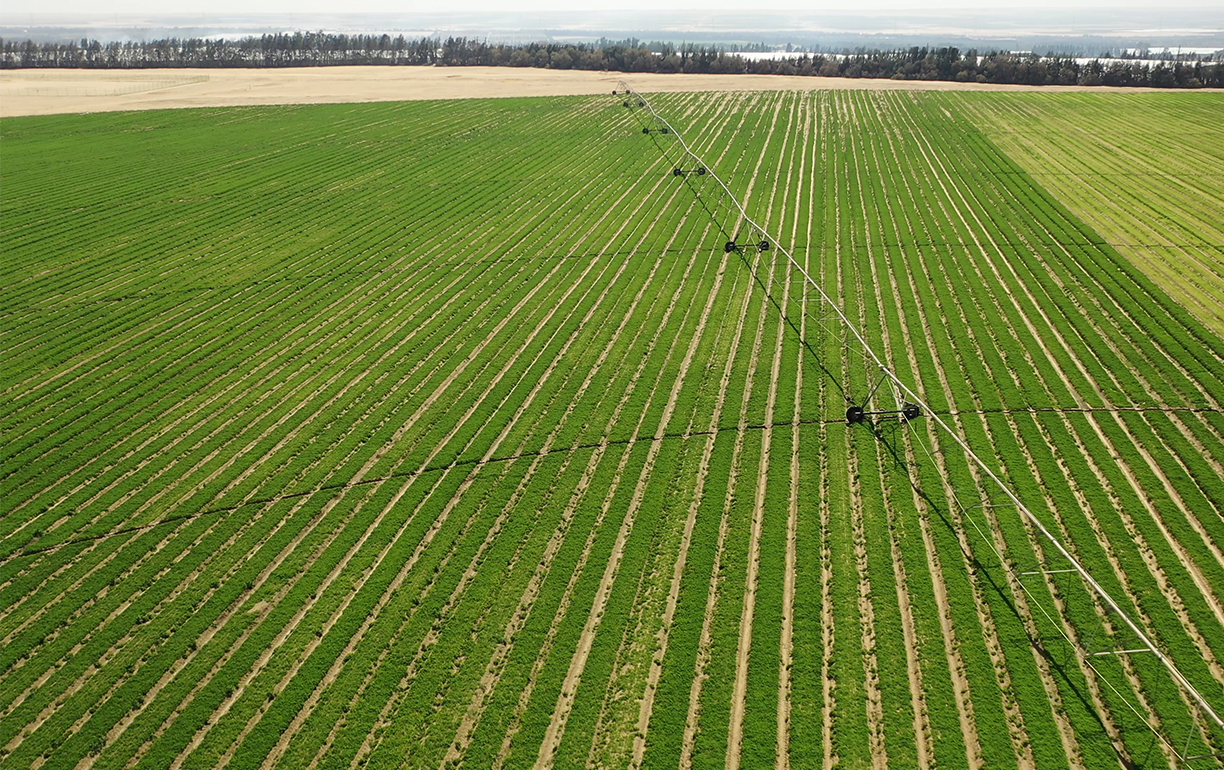
Green desert - Egypt's sustainable agriculture takes off.
From fertile oases to efficient airfreight - Egypt's agriculture is booming and focuses on sustainability. Find out how Lufthansa Cargo is supporting the green movement and reducing CO2 emissions to transport fruit and vegetables.
You can watch this project also on the YouTube channel of Lufthansa Cargo.
Green fields as far as the eye can see. A few miles further on, the desert begins. But the Nile - at 6671 km the longest river in the world - transforms the areas near the river and especially the 24,000 square kilometer Nile Delta into a fertile oasis. The conditions here are ideal for the growth of many plants. Plenty of sunshine, fertile soils, experienced agronomists and clever agricultural practices allow the plants to grow better than in many other countries. A field planted with wheat in Egypt, for example, produces 2.9 tons of grain, compared to 1.5 tons in many other countries.
Egyptians take advantage of these benefits and agriculture makes up a large part of the economy. Agriculture not only contributes to the 15% of gross domestic product, but also employs 28% of the country's workforce, and in Upper Egypt even more than 50%. And the trend is rising. A growth rate of 10% per year is currently forecasted for the coming years. However, the industry plays a key role not only for the country itself, but also for exports to other countries and the production of food worldwide.
The Egyptian government is not only aware of the importance of the industrial sector, but also of the importance of sustainability. And Egypt wants to push ahead with sustainable measures. The Minister of Agriculture, El-Sayed El-Quseir, has a clear vision of Egypt's sustainable agricultural development by 2030. The government is providing targeted support to the sector with low-interest loans for farmers, digitization, and expansion projects to create greater self-sufficiency in strategic crops, increase the competitiveness of Egypt's agricultural exports, minimize the impact of climate change on the agricultural sector and support integrated agricultural and rural communities. A visit to three of the many farms in Egypt confirms these goals and leaves you impressed.
Green fields as far as the eye can see. A few miles further on, the desert begins. But the Nile - at 6671 km the longest river in the world - transforms the areas near the river and especially the 24,000 square kilometer Nile Delta into a fertile oasis. The conditions here are ideal for the growth of many plants. Plenty of sunshine, fertile soils, experienced agronomists and clever agricultural practices allow the plants to grow better than in many other countries. A field planted with wheat in Egypt, for example, produces 2.9 tons of grain, compared to 1.5 tons in many other countries. |
The Egyptian government is not only aware of the importance of the industrial sector, but also of the importance of sustainability. And Egypt wants to push ahead with sustainable measures. The Minister of Agriculture, El-Sayed El-Quseir, has a clear vision of Egypt's sustainable agricultural development by 2030. The government is providing targeted support to the sector with low-interest loans for farmers, digitization, and expansion projects to create greater self-sufficiency in strategic crops, increase the competitiveness of Egypt's agricultural exports, minimize the impact of climate change on the agricultural sector and support integrated agricultural and rural communities. A visit to three of the many farms in Egypt confirms these goals and leaves you impressed.
|
The Belco Farm is located an hour's drive north-west of Cairo. Belco has been producing fruit and vegetables in the Nile Delta since the 1960s. In 1993, the brothers Sherif and Mohsen El-Beltagy took over and continued to expand the farm. Belco now grows for example grapes, beans, spring onions, peas, strawberries, raspberries, blueberries, sweet potatoes and tenderstem broccoli on over 3,000 acres of land. "In addition to our farmland, we also own three packing houses and produce around 15,000 tons of fruit and vegetables a year, mainly for Europe, but also for Africa, Asia and the Middle East," says Sherif El-Beltagy proudly. "Our core values include innovation and sustainability. We persistently invest in our infrastructure, and technological and agricultural capabilities to support both our employees and the surrounding communities and to protect the environment."
Between high bush beans and harvest workers carefully picking raspberries, the Managing Director's words are impressively brought to life. Mohamed Gad, Research & Development Manager at Belco, leads us through rows of Adelita, a raspberry variety that is very well suited for cultivation in Egypt. "Sustainability starts with the selection of the variety," reports Mohamed. "We choose plant species and varieties that achieve the best harvest results in our specific environment, for example with the warm weather. Our irrigation and collection systems make optimum use of every drop of water." When it comes to the environment and biodiversity, he bursts with knowledge. "Of course, we pay attention to crop rotations, such as sweet potatoes first, followed by peas or beans and then spring onions, in order to protect the organic matter in the soil as much as possible. But for us, these are the basics of sustainable agriculture." Things get much more detailed when it comes to pest control. "The use of pesticides is the very last thing we do. Before that, there are dozens of other ways to keep pests away or control them. The most effective measures are actually taken to prevent pest infestations. If an infestation does occur, for example by the well-known and feared red mite, we use persimilis - also known as predatory mites. These are beneficial insects that first eat the red mites and then themselves. This biological control is very effective, does not harm the environment and the pests cannot develop resistance to it, as is the case with some pesticides, for example." The impact on the environment concerns the agronomist in every aspect of production. For example, if the trees are cut on the farm, the wood is used for constructions in the fields. No structures or materials may be used that could injure or even disturb birds during migration. "Of course, we also have to keep the odd rodent away from our farms. But we can only achieve this with measures that do not harm any animals. None of our measures must harm wildlife."
The Belco Farm is located an hour's drive north-west of Cairo. Belco has been producing fruit and vegetables in the Nile Delta since the 1960s. In 1993, the brothers Sherif and Mohsen El-Beltagy took over and continued to expand the farm. Belco now grows for example grapes, beans, spring onions, peas, strawberries, raspberries, blueberries, sweet potatoes and tenderstem broccoli on over 3,000 acres of land. "In addition to our farmland, we also own three packing houses and produce around 15,000 tons of fruit and vegetables a year, mainly for Europe, but also for Africa, Asia and the Middle East," says Sherif El-Beltagy proudly. "Our core values include innovation and sustainability. We persistently invest in our infrastructure, and technological and agricultural capabilities to support both our employees and the surrounding communities and to protect the environment." Between high bush beans and harvest workers carefully picking raspberries, the Managing Director's words are impressively brought to life. Mohamed Gad, Research & Development Manager at Belco, leads us through rows of Adelita, a raspberry variety that is very well suited for cultivation in Egypt. "Sustainability starts with the selection of the variety," reports Mohamed. "We choose plant species and varieties that achieve the best harvest results in our specific environment, for example with the warm weather. Our irrigation and collection systems make optimum use of every drop of water." |
When it comes to the environment and biodiversity, he bursts with knowledge. "Of course, we pay attention to crop rotations, such as sweet potatoes first, followed by Peas or Beans and then Spring onions, in order to protect the organic matter in the soil as much as possible. But for us, these are the basics of sustainable agriculture." Things get much more detailed when it comes to pest control. "The use of pesticides is the very last thing we do. Before that, there are dozens of other ways to keep pests away or control them. The most effective measures are actually taken to prevent pest infestations. If an infestation does occur, for example by the well-known and feared red mite, we use persimilis - also known as predatory mites. These are beneficial insects that first eat the red mites and then themselves. This biological control is very effective, does not harm the environment and the pests cannot develop resistance to it, as is the case with some pesticides, for example." The impact on the environment concerns the agronomist in every aspect of production. For example, if the trees are cut on the farm, the wood is used for constructions in the fields. No structures or materials may be used that could disturb or even injure birds during migration. "Of course, we also have to keep the odd rodent away from our farms. But we can only achieve this with measures that do not harm any animals. None of our measures must harm wildlife."
|
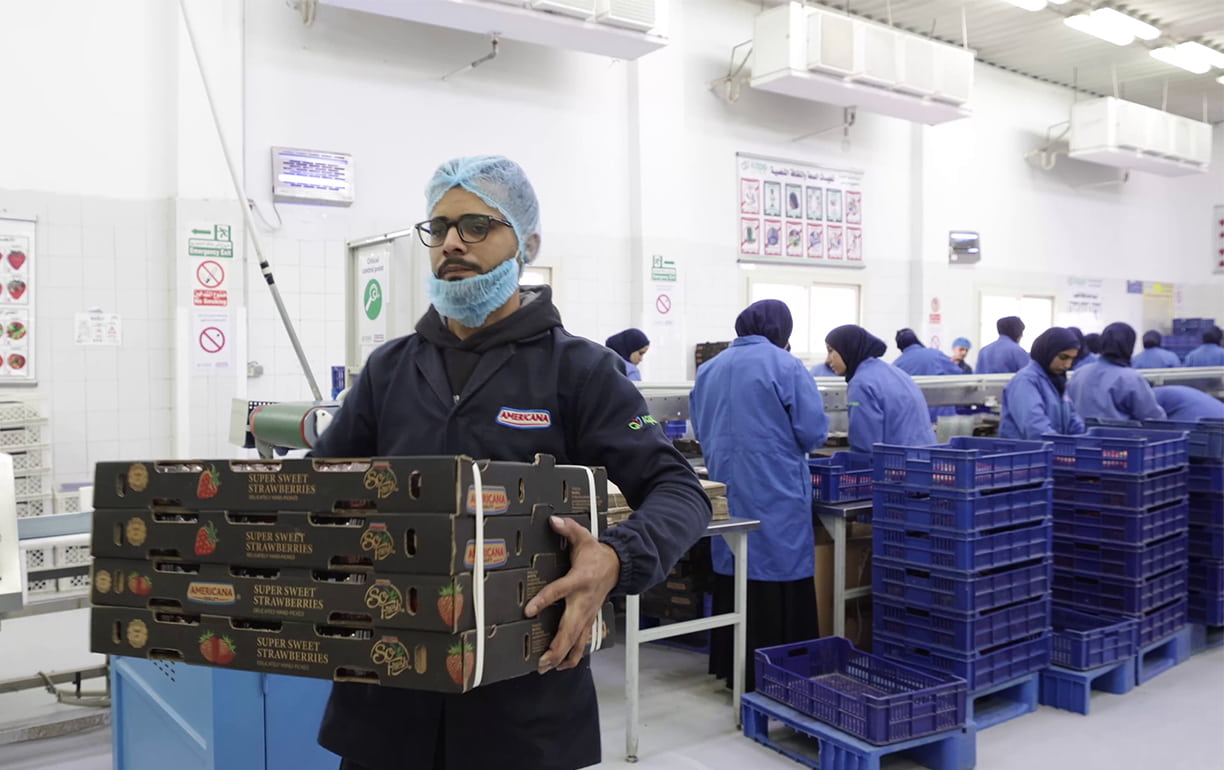
Sustainable measures are also evident during processing in the packing house. The workers carefully cut the green of the spring onions to length and the ends of the beans are also shortened. "We adapt our production to the preferences of our customers. In France and England, the extra-fine beans are currently particularly popular and are often bought already trimmed," reports Mohamed. It might seem obvious to criticize the picky Europeans with their specific ideas about vegetables, but Mohamed disagrees directly. "We see things differently here. On the one hand, our employees here can earn money by cutting off the ends, for example. And while these ends would probably end up in the garbage can in private households, nothing is thrown away here. The cut plant parts are either dried and used in seasoning mixtures, as animal feed or as a component of fertilizer. We always try to implement the customers' wishes in such a way that everyone can benefit from them."
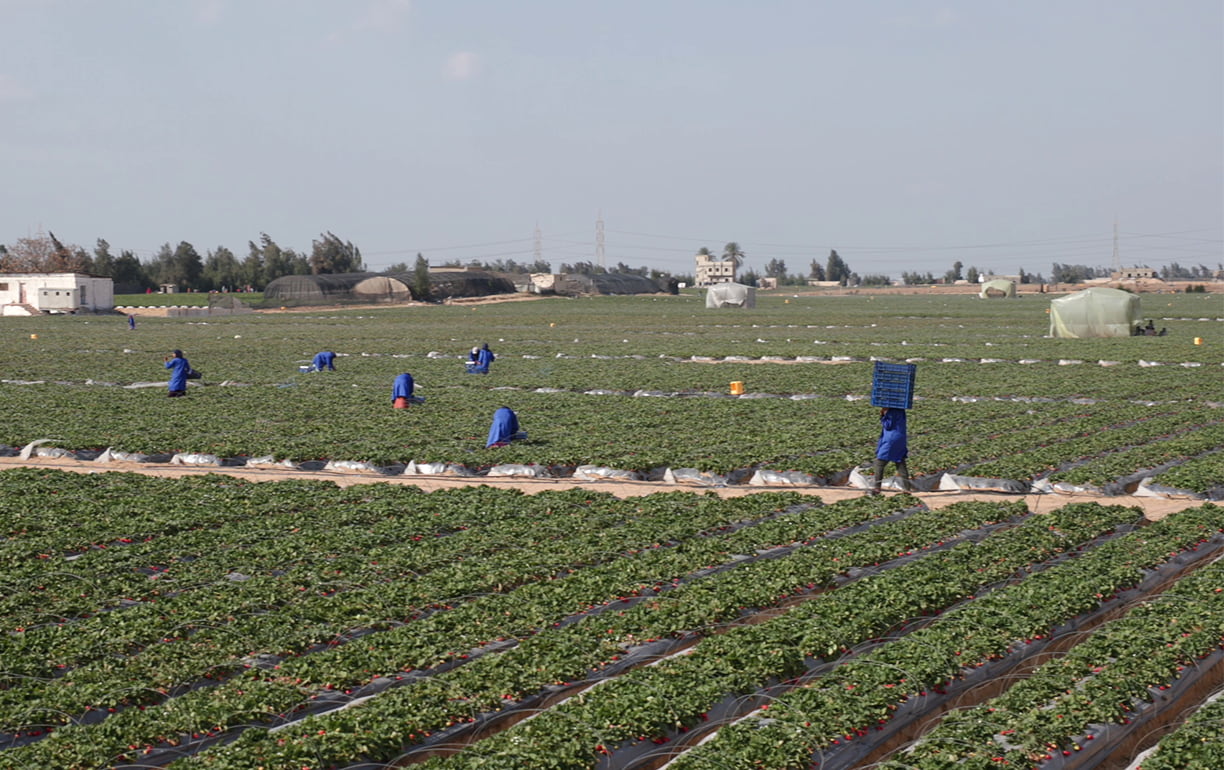
East of Cairo is another farm specialized on strawberries. In addition to strawberries, corn, broccoli, spinach, and much more is grown on 4,000 hectares. "Our fields are located in one of the most fertile agricultural regions in the world and provide an ideal environment for the around 45,000 tons of fruit and vegetables that our fields grow every year," explains Kamal Eldakak, the Agriculture Director of the farm.
While dozens of harvest workers carefully pick strawberries, Kamal talks about the special conditions in Egypt. "Strawberries are only allowed to grow in sterilized soil. Most agricultural countries in the world must use chemicals for this. We can sterilize our soil in the summer months using the sun. We can hardly grow anything at this time, but the heat of the sun acts like a disinfection of the soil for the next generation of strawberries." Of course, the sun is not only used for this purpose. In addition to green fields, there are also solar panels that provide the farm's entire power supply. The very fertile soil requires 50% less fertilizer than other regions. "Less fertilizer also means less energy required to produce and transport it," Kamal sums up.
In addition to the impact on the environment, the support of their employees and communities is particularly important to the agricultural entrepreneurs. All employees have employment contracts that precisely regulate their working hours. In the event of overtime, this must be paid. Medical costs are covered, and full payment is also made in the event of absence due to illness. In the summer months, when the farms are closed, employees continue to receive 50% of their salary.
The farm is also involved in training neighboring small farms and teaches them how to comply with European standards so that the small farms can also offer their products there. Here, community is more important than competition. "We are not only subject to strict international requirements such as Farm to Fork, Global Gap and Sedex, but also to the often even stricter requirements of food chains such as Tesco, Edeka, Sainsbury and Aldi, which carry out annual inspections at our premises. Above all, our own ambition is to deliver the best product while helping our communities and protecting our land. We have been farmers for hundreds of generations and are proud of our achievements," summarizes the Agriculture Director.
While dozens of harvest workers carefully pick strawberries, Kamal talks about the special conditions in Egypt. "Strawberries are only allowed to grow in sterilized soil. Most agricultural countries in the world must use chemicals for this. We can sterilize our soil in the summer months using the sun. We can hardly grow anything at this time, but the heat of the sun acts like a disinfection of the soil for the next generation of strawberries." Of course, the sun is not only used for this purpose. In addition to green fields, there are also solar panels that provide the farm's entire power supply. The very fertile soil requires 50% less fertilizer than other regions. "Less fertilizer also means less energy required to produce and transport it," Kamal sums up. |
The farm is also involved in training neighboring small farms and teaches them how to comply with European standards so that the small farms can also offer their products there. Here, community is more important than competition. "We are not only subject to strict international requirements such as Farm to Fork, Global Gap and Sedex, but also to the often even stricter requirements of food chains such as Tesco, Edeka, Sainsbury and Aldi, which carry out annual inspections at our premises. Above all, our own ambition is to deliver the best product while helping our communities and protecting our land. We have been farmers for hundreds of generations and are proud of our achievements," summarizes the Agriculture Director.
|
A third manufacturer of fresh produce is Green Egypt. “We own seven farms with 4000 acres of land located along the river Nile. We produce fruits and vegetables, some of them like sweet potatoes and green beans are also available as organic,” explains the CEO and founder of Green Egypt Sherif Attia. “Along with the sun sterilization of our soil, the focus on minimizing the water usage at all our farms with either drip irrigation or pivot irrigation, we invest in many more sustainable agriculture processes and are also pioneers in empowering the female workforce.”
The company invested in various initiatives to ensure the wellbeing of their workers, with a special focus on the women in their company. They signed up for a UN project supporting women's empowerment and have taken on the Women's Empowerment Principles (WEPs) to heart. A real game-changer was the nursery they built at their pack house in Giza. This nursery allows mothers with young children to continue working, breaking the cultural norm that forced married women to give up their jobs after marriage. This not only retains experienced women laborers but also encourages others to join the workforce, ultimately boosting productivity and making a positive impact on the community.
But their commitment to the community didn't stop there. Green Egypt had also embarked on water purification projects for the villages surrounding their farms, ensuring that the local communities had access to clean and safe drinking water.
Despite all the investments and innovations in social and economic sustainability on the farms, there is always a point of conflict. The most frequently criticized point in the export and import of fruit is the transport chain. Transportation must take place as quickly as possible to prevent the goods from spoiling. This is where the speed of air freight comes into play.
A third manufacturer of fresh produce is Green Egypt. “We own seven farms with 4000 acres of land located along the river Nile. We produce fruits and vegetables, some of them like sweet potatoes and green beans are also available as organic,” explains the CEO and founder of Green Egypt Sherif Attia. “Along with the sun sterilization of our soil, the focus on minimizing the water usage at all our farms with either drip irrigation or pivot irrigation, we invest in many more sustainable agriculture processes and are also pioneers in empowering the female workforce.” The company invested in various initiatives to ensure the wellbeing of their workers, with a special focus on the women in their company. They signed up for a UN project supporting women's empowerment and have taken on the Women's Empowerment Principles (WEPs) to heart. A real game-changer was the nursery they built at their pack house in Giza. This nursery allows mothers with young children to continue working, breaking the cultural norm that forced married women to give up their jobs after marriage. This not only retains experienced women laborers but also encourages others to join the workforce, ultimately boosting productivity and making a positive impact on the community. |
But their commitment to the community didn't stop there. Green Egypt had also embarked on water purification projects for the villages surrounding their farms, ensuring that the local communities had access to clean and safe drinking water. Despite all the investments and innovations in social and economic sustainability on the farms, there is always a point of conflict. The most frequently criticized point in the export and import of fruit is the transport chain. Transportation must take place as quickly as possible to prevent the goods from spoiling. This is where the speed of air freight comes into play. |
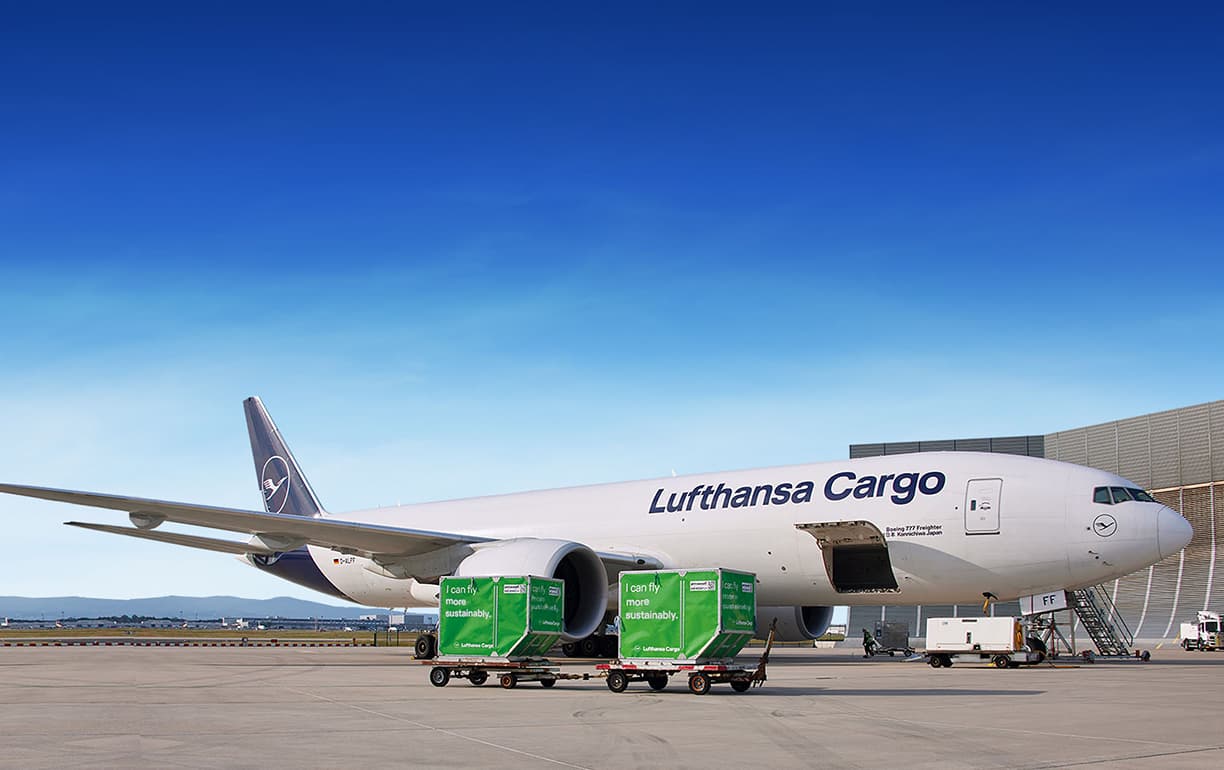
Depending on the time of year, the carbon footprint of fruit and vegetables can even be better if they are imported, as growing them in greenhouses or storing them for extended periods in cold stores causes more CO2 than transportation in some cases. However, this does not mean that not every opportunity to optimize should be considered. There are various ways of saving or offsetting emissions during transportation. "Lufthansa Cargo itself optimizes the reduction of its emissions through many measures, such as the use of AeroSHARK, lighter loading equipment and optimal flight route planning. For customers, there are two additional ways to contribute to the reduction of CO2 emissions. Firstly, by using Sustainable Aviation Fuel, and secondly, by offsetting remaining CO2 emissions through the contribution to high-quality climate protection projects," explains Nevine Saba, Commercial Manager at Lufthansa Cargo. She herself is involved in the production of SAF admittedly on a small scale. "We have an app in Egypt that we can use to collect our old cooking oil. These leftovers are then used for the production of SAF."
Venus International Transport also recognizes the importance of these measures. Samia El Sayed has been managing the leading exporter in Egypt since 1986 and appreciates the close cooperation with Lufthansa Cargo: "Airfreight is crucial for perishables, as they need to arrive at their destination as quickly as possible. Lufthansa Cargo is the perfect partner due to its network, its infrastructure such as the Perishable Center in Frankfurt and its reliability. With their Perishable toDoor service in Europe, they offer direct and temperature-controlled delivery to the recipient's warehouse, with the goods already checked and cleared through customs. This saves us the most important thing in this business: time." Another crucial factor when it comes to speed: a high-frequency network. Cairo currently has five weekly freighter connections to Frankfurt. On top of this, there are thirty weekly belly connections to Frankfurt, Munich, and Vienna.
In recent years, the entrepreneur, who is very well connected in her industry, has also focused on the most sustainable supply chain possible and relies on sustainable aviation fuel. "We already had 100% offset charters from Cairo to Frankfurt in 2022 and 2023. In 2024, we had two fully offset A321F charters with Sustainable Aviation Fuel. For me, Lufthansa Cargo is the leading provider in terms of sustainability in air freight," reports the logistics expert, who is known to everyone as "Madame Samia". The next generation is already integrated into the company at Venus International Transport. Vice Chairman Ahmed Fouad continues: "Globalization also means producing what you can do best under the given circumstances. And Egypt is a pioneer in agriculture. Air freight enables our farmers to be part of the global community and offer what we have perfected over hundreds and thousands of years. Lufthansa Cargo's purpose #EnablingGlobalBusiness is exactly in line with our idea of giving Egypt's innovative agricultural industry the chance to participate in the global market and make the most of global needs and local conditions."
Venus International Transport also recognizes the importance of these measures. Samia El Sayed has been managing the leading exporter in Egypt since 1986 and appreciates the close cooperation with Lufthansa Cargo: "Airfreight is crucial for perishables, as they need to arrive at their destination as quickly as possible. Lufthansa Cargo is the perfect partner due to its network, its infrastructure such as the Perishable Center in Frankfurt and its reliability. With their Perishable toDoor service in Europe, they offer direct and temperature-controlled delivery to the recipient's warehouse, with the goods already checked and cleared through customs. This saves us the most important thing in this business: time." Another crucial factor when it comes to speed: a high-frequency network. Cairo currently has five weekly freighter connections to Frankfurt. On top of this, there are thirty weekly belly connections to Frankfurt, Munich, and Vienna. |
In recent years, the entrepreneur, who is very well connected in her industry, has also focused on the most sustainable supply chain possible and relies on sustainable aviation fuel. "We already had 100% offset charters from Cairo to Frankfurt in 2022 and 2023. In 2024, we had two fully offset A321F charters with Sustainable Aviation Fuel. For me, Lufthansa Cargo is the leading provider in terms of sustainability in air freight," reports the logistics expert, who is known to everyone as "Madame Samia". The next generation is already integrated into the company at Venus International Transport. Vice Chairman Ahmed Fouad continues: "Globalization also means producing what you can do best under the given circumstances. And Egypt is a pioneer in agriculture. Air freight enables our farmers to be part of the global community and offer what we have perfected over hundreds and thousands of years. Lufthansa Cargo's purpose #EnablingGlobalBusiness is exactly in line with our idea of giving Egypt's innovative agricultural industry the chance to participate in the global market and make the most of global needs and local conditions." |
Find out more about our global network and our Perishable product.
Published 11/2024
Pictures: Luis Pedro Costa Gomes, Lufthansa Cargo
Find out more about our global network and our Perishable product.
Published 11/2024
Pictures: Luis Pedro Costa Gomes, Lufthansa Cargo
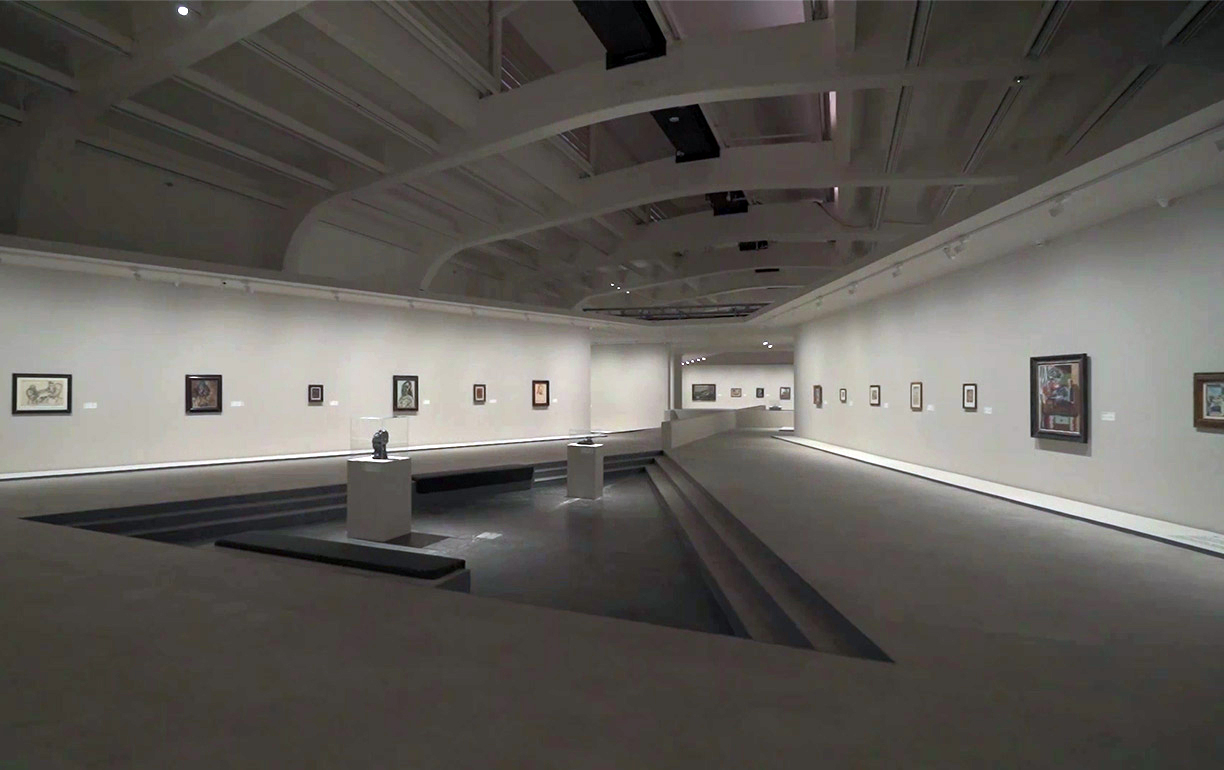
The Berggruen collection on a world tour
Berggruen! A name that everyone in Berlin and the art world knows. An art collection with history. History that is currently traveling the world.
You can watch this project also on the YouTube channel of Lufthansa Cargo.
The collection once belonged to Heinz Berggruen, one of the most important art dealers and collectors of the 20th century. Born in 1914, Berggruen grew up in a Jewish, middle-class family in Berlin. In 1936 he received a scholarship from Berkeley University in California and was thus able to flee from the National Socialists in Germany.
Sixty years later, he returned to Germany with a gesture of generosity and reconciliation with his homeland: his art collection consisting of 170 works, mainly by Picasso, Klee, Giacometti, and Matisse. The State Museums in Berlin bought the collection for 253 million Deutschmarks, a price well below its market value. Since then, the works have been exhibited in the specially renovated Stüler Building, opposite Charlottenburg Palace, on the upper floor of which Berggruen also lived during his time in Berlin. Keeping the collection in Germany was extremely important to the art collector. After Heinz Berggruen's death in 2007, his family agreed to make further works available to the Museum Berggruen on permanent loan and to continue to support the museum.
The collection once belonged to Heinz Berggruen, one of the most important art dealers and collectors of the 20th century. Born in 1914, Berggruen grew up in a Jewish, middle-class family in Berlin. In 1936 he received a scholarship from Berkeley University in California and was thus able to flee from the National Socialists in Germany. Sixty years later, he returned to Germany with a gesture of generosity and reconciliation with his homeland: his art collection consisting of 170 works, mainly by Picasso, Klee, Giacometti, and Matisse. |
The State Museums in Berlin bought the collection for 253 million Deutschmarks, a price well below its market value. Since then, the works have been exhibited in the specially renovated Stüler Building, opposite Charlottenburg Palace, on the upper floor of which Berggruen also lived during his time in Berlin. Keeping the collection in Germany was extremely important to the art collector. After Heinz Berggruen's death in 2007, his family agreed to make further works available to the Museum Berggruen on permanent loan and to continue to support the museum.
|
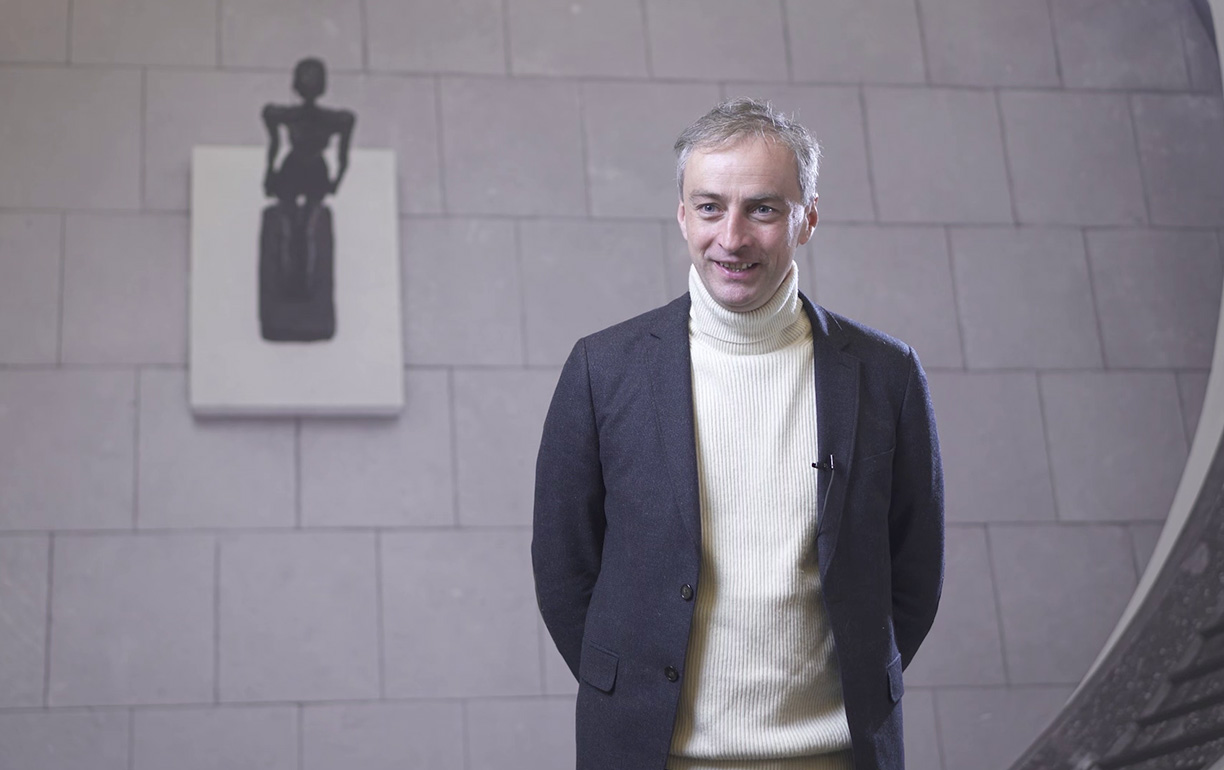
Gabriel Montua, Head of Museum Berggruen, explains what is so special about the collection: "The collection is unique in the sense that it was chosen and selected by one individual, Heinz Berggruen, according to the tastes and the currents of his time. That's why it is composed of just a handful of very well-known artists from the 20th century to which he had built a very special relationship. Especially the works of Picasso, of which we have about 135 in our collection, are far more than most other museums have. And when you're in Berlin or you are visiting one of the museums we collaborate with, you can truly walk through the galleries and experience nine decades of Picasso's works."
The museum has been under renovation since September 2022. A large part of the exhibition has been traveling since then. Tokyo, Osaka, Shanghai, Beijing, and Venice have been the stops so far. The exhibition flew from Germany to Japan and from Beijing back to Europe with Lufthansa Cargo.
Transporting a shipment of this size is no everyday business. A total of 91 works of art in 42 bespoke climate crates were transported on five flights. The largest works found space on board the B777 freighter. Other works of art flew in the bellies of the Lufthansa passenger aircraft from Beijing. The Lufthansa Cargo network offers extensive possibilities. The current 17 B777Fs are among the largest and most efficient freighters of their generation and will offer 82 weekly connections worldwide in the 2024 summer timetable. In addition, there is a short and medium-haul network of A321 freighters and over 7,000 weekly flights in the cargo holds of passenger aircraft operated by Lufthansa, Austrian Airlines, Brussels Airlines, Discover Airlines and SunExpress. Even the largest works of art can be accommodated in the B777F. The freighter currently connects the Chinese capital with Frankfurt five times a week. In addition, there are daily connections with Lufthansa's A340 to Frankfurt and also daily connections to Munich with the A350.
When transporting large consignments of art, however, it is not just a flexible route network that is important. Above all, it is about the professional transportation of irretrievable goods. In addition to Lufthansa Cargo, the Berggruen Museum relied on Hasenkamp and Eric Art Services.
The museum has been under renovation since September 2022. A large part of the exhibition has been traveling since then. Tokyo, Osaka, Shanghai, Beijing, and Venice have been the stops so far. The exhibition flew from Germany to Japan and from Beijing back to Europe with Lufthansa Cargo. |
The current 17 B777Fs are among the largest and most efficient freighters of their generation and will offer 82 weekly connections worldwide in the 2024 summer timetable. In addition, there is a short and medium-haul network of A321 freighters and over 7,000 weekly flights in the cargo holds of passenger aircraft operated by Lufthansa, Austrian Airlines, Brussels Airlines, Discover Airlines and SunExpress. Even the largest works of art can be accommodated in the B777F. The freighter currently connects the Chinese capital with Frankfurt five times a week. In addition, there are daily connections with Lufthansa's A340 to Frankfurt and also daily connections to Munich with the A350. When transporting large consignments of art, however, it is not just a flexible route network that is important. Above all, it is about the professional transportation of irretrievable goods. In addition to Lufthansa Cargo, the Berggruen Museum relied on Hasenkamp and Eric Art Services.
|
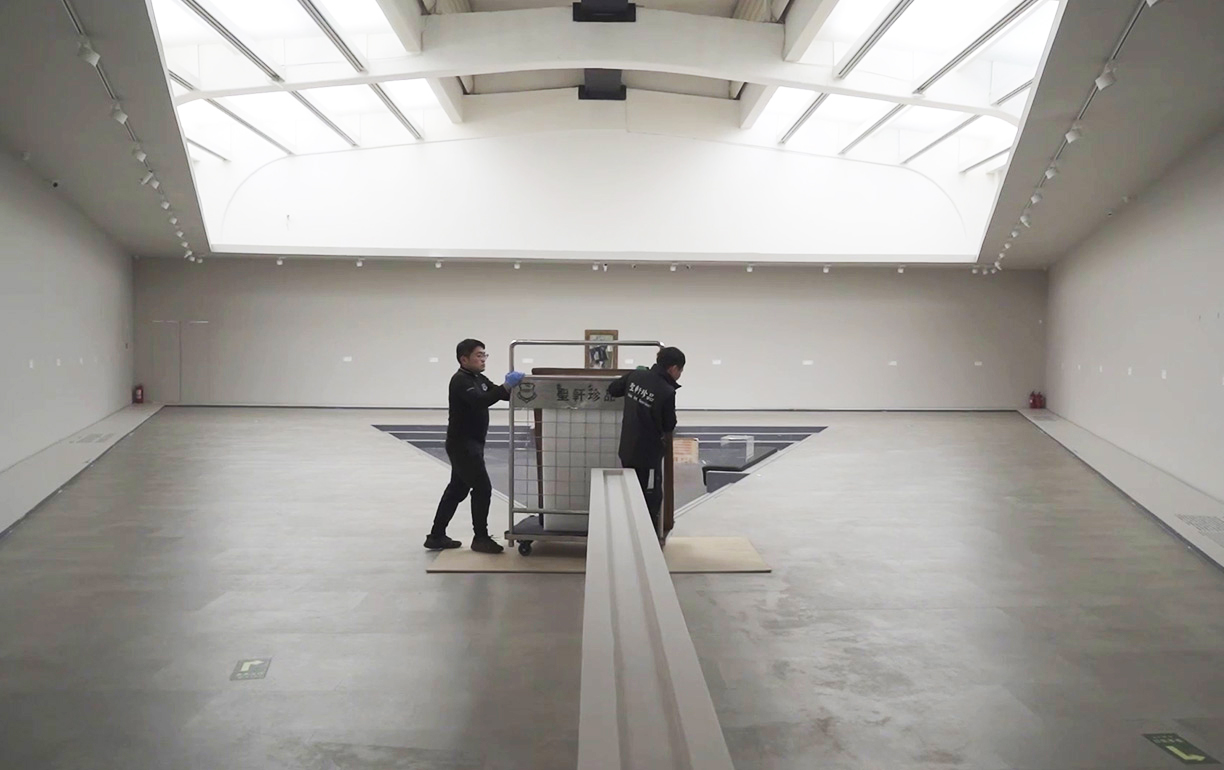
Hasenkamp can look back on over 100 years of experience in the transportation and storage of valuable and sensitive items. With around 1,000 employees worldwide, Hasenkamp is one of the leading providers in the field of art logistics. "From individual works of art to the complete inventory of entire museums, from the transport of a small-format painting to a statue weighing several tons, we can handle any project with our employees at a total of 40 locations in 28 countries. Our specialists around the world also work with specially selected service providers," says Rachel Riddell, key-account manager for Museum Berggruen in Berlin.
One of these selected service providers is Eric Arts Services. Eric Arts Services was founded in 2014 as a small company with only a few employees. Within ten years they've grown to 150 employees with 13 offices in China and one in London. "As a company in the cultural business, we deal with artworks every day. In the past year, we organized the transport of more than 800 exhibitions by all branches, including galleries, museums, auction houses and other institutions," says Stella Wang, Managing Director of Eric Arts Services. "Each piece of artwork is unique, and most of them cannot be replicated; we treat them like a newborn baby. Packaging, temperature and humidity, and route are all crucial for the transportation of artworks. The delivery of artworks plays a crucial role in the entire exhibition chain. Only when the artworks are safely delivered, the exhibition can be opened as scheduled. Ensuring its safe transportation is of great significance for protecting cultural heritage, promoting cultural exchange, and developing the art market."
"Every time a work of art changes its location, it's a challenge," adds Gabriel Montua. "You need to make sure that the work will be moved without being damaged or harmed in any way. So usually what happens between museums is that you ask for one, or maybe two or three works to come as a loan to a special exhibition. What is special here is that they're talking about a completely different scale with 91 works. The efforts required to make sure that all these works are transported safely and that everything goes smoothly are, of course, significantly greater than if we if we were dealing with just a single loan.” Stella Wang resumes: "Lufthansa Cargo has done a great job! They not only ensure timeliness, but also guarantee the safety of the goods transported."
One of these selected service providers is Eric Arts Services. Eric Arts Services was founded in 2014 as a small company with only a few employees. Within ten years they've grown to 150 employees with 13 offices in China and one in London. "As a company in the cultural business, we deal with artworks every day. In the past year, we organized the transport of more than 800 exhibitions by all branches, including galleries, museums, auction houses and other institutions," says Stella Wang, Managing Director of Eric Arts Services. "Each piece of artwork is unique, and most of them cannot be replicated; we treat them like a newborn baby. Packaging, temperature and humidity, and route are all crucial for the transportation of artworks. The delivery of artworks plays a crucial role in the entire exhibition chain. Only when the artworks are safely delivered, the exhibition can be opened as scheduled. Ensuring its safe transportation is of great significance for protecting cultural heritage, promoting cultural exchange, and developing the art market." |
"Every time a work of art changes its location, it's a challenge," adds Gabriel Montua. "You need to make sure that the work will be moved without being damaged or harmed in any way. So usually what happens between museums is that you ask for one, or maybe two or three works to come as a loan to a special exhibition. What is special here is that they're talking about a completely different scale with 91 works. The efforts required to make sure that all these works are transported safely and that everything goes smoothly are, of course, significantly greater than if we if we were dealing with just a single loan.” Stella Wang resumes: "Lufthansa Cargo has done a great job! They not only ensure timeliness, but also guarantee the safety of the goods transported."
|
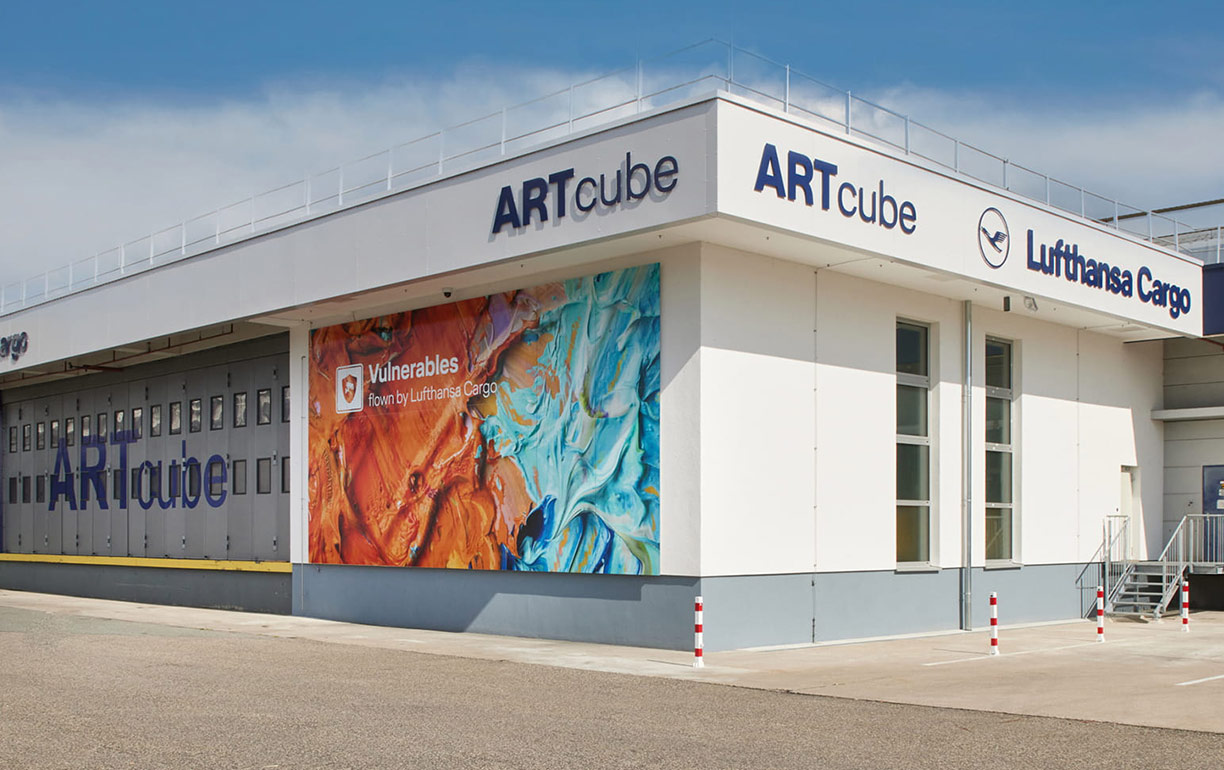
"We have been cooperating with Lufthansa Cargo worldwide for decades. We appreciate the unparalleled route network, especially from and to the cultural hotspot Europe, the close and competent exchange with the employees and the art-specific infrastructure such as the ARTcube in Frankfurt,” says Rachel Riddell from Hasenkamp, summarizing the cooperation.
After arrival in Frankfurt, the artworks are stored in the ARTCube at the airline's home airport. This is specially designed to meet the climate and security requirements for the storage of sensitive works of art. The shipment is handled by specially trained staff who know the requirements of the special cargo inside out. In addition, Lufthansa Cargo also offers the option of having a supervisor accompany the shipments at the Frankfurt hub.
Back in Europe, the collection was just shown in Venice. From March to June 2024, a selection of works from the Museum Berggruen was on display at two locations in Venice in dialog with works from the collection of the Gallerie dell'Accademia. This will be followed in the fall by a comprehensive exhibition at the Musée de l'Orangerie in Paris. In 2026, the museum in Berlin will reopen and welcome the artworks back home.
Stella Wang could then view the exhibition again in its home country and fulfill two more dreams. She would like to see Documenta at the Museum Fridericianum in Kassel and La Biennale di Venezia. Both Wang and Montua emphasize the significance of traveling art. “Nowadays most images are available online. You can find mostly anything on the internet. But being able to actually see the original work is, of course, something very, very special,” says the Head of Museum Berggruen.
Back in Europe, the collection was just shown in Venice. From March to June 2024, a selection of works from the Museum Berggruen was on display at two locations in Venice in dialog with works from the collection of the Gallerie dell'Accademia. This will be followed in the fall by a comprehensive exhibition at the Musée de l'Orangerie in Paris. In 2026, the museum in Berlin will reopen and welcome the artworks back home. |
Stella Wang could then view the exhibition again in its home country and fulfill two more dreams. She would like to see Documenta at the Museum Fridericianum in Kassel and La Biennale di Venezia. Both Wang and Montua emphasize the significance of traveling art. “Nowadays most images are available online. You can find mostly anything on the internet. But being able to actually see the original work is, of course, something very, very special,” says the Head of Museum Berggruen.
|
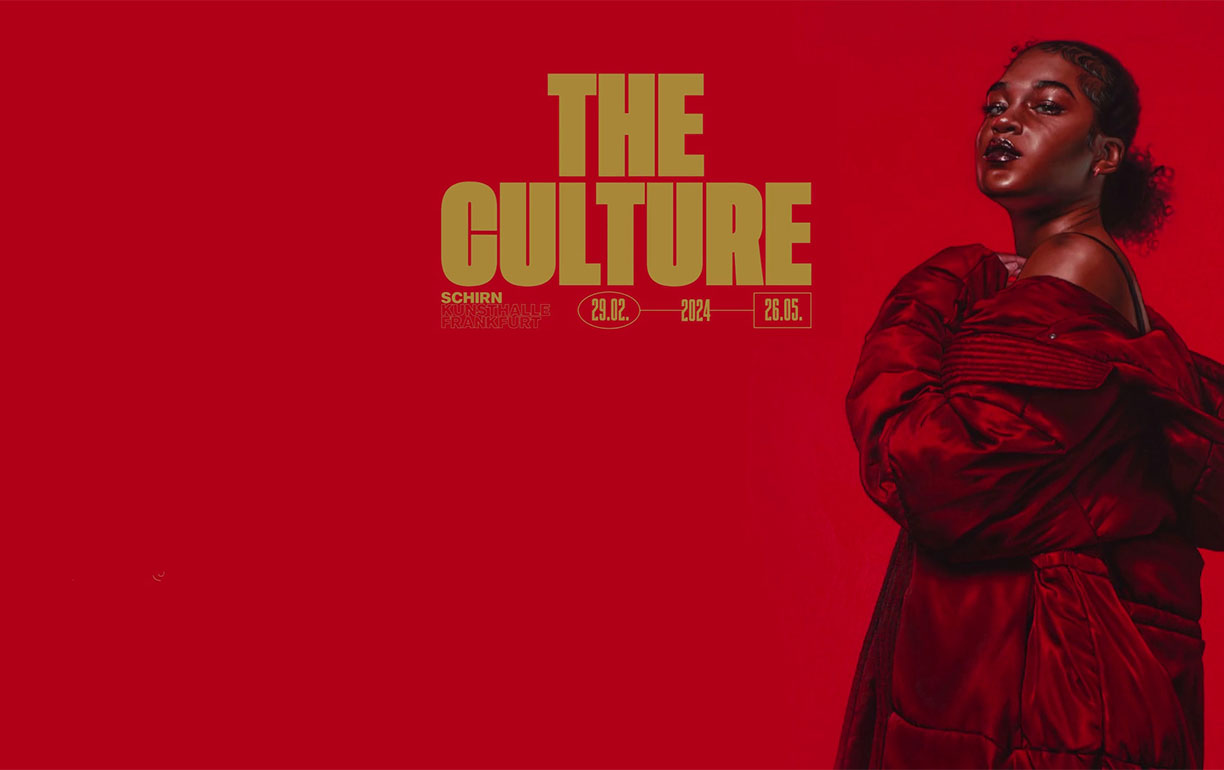
Art in transcultural exchange
"I say hip, you say hop." Everyone joins in the DJ's call. Lines by Notorious B.I.G., Grandmaster Flash and the Sugarhill Gang echo from the speakers. You can feel the bass in your whole body. The dance floor is packed. People are standing on the stairs, all moving to hip-hop highlights from the past five decades. Anyone expecting a quiet evening at the opening of an art exhibition was in for a surprise at “THE CULTURE. Hip-Hop and Contemporary Art in the 21st Century”. It was loud, glittering and everything that 50 years of hip-hop promises.
To celebrate its 50th anniversary, the SCHIRN is dedicating a large interdisciplinary exhibition to hip-hop and its profound influence on contemporary art and culture in our society. Anyone visiting the exhibition these days, after the opening party is over, will be able to enjoy it in peace. Still, it is worth bringing your smartphone and headphones. QR codes on the artworks will allow you to listen to the songs to which they refer. More than one hundred artworks are on display, including paintings, photographs, sculptures, and videos, as well as fashion and vinyl, by internationally renowned contemporary artists. Well-known artists include Jean-Michel Basquiat, Lauren Halsey, Julie Mehretu, Tschabalala Self, Arthur Jafa, Khalil Joseph, Virgil Abloh, and Gordon Parks. THE CULTURE was organized by the Baltimore Museum of Art and the Saint Louis Art Museum and is presented in cooperation with the SCHIRN KUNSTHALLE FRANKFURT. The exhibition traveled from the United States to Germany aboard Lufthansa Cargo. | The challenge of transporting art is that it involves the mobilization of unique, irreplaceable cultural assets. As a result, the artworks must be handled and protected with the utmost care. Each piece has a unique structure, material composition and delicate surface, making the preparation and execution of the transport an extremely demanding task. In addition, factors such as temperature, humidity and vibration play a crucial role, as they can damage the artwork during transport. Therefore, transporting art requires specialized planning, packaging, and logistics to ensure that they arrive safely at their destination.
|
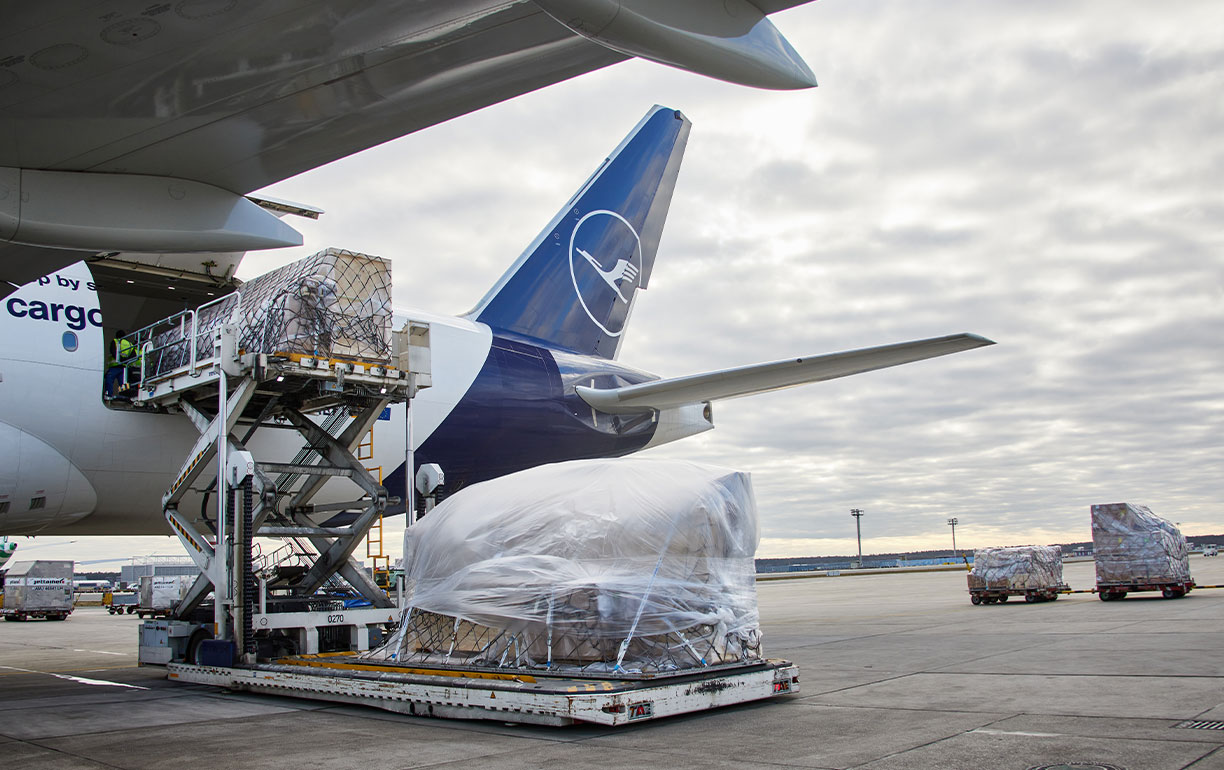
The B777 freighter transported a total of 62 packages and 14640 kg of art from Chicago, the logistical heart of the US, to Lufthansa Cargo's hub in Frankfurt in the center of Europe. "A shipment of this size is not standard. We look at a shipment of this scale as a project, not just an AWB shipment. The preparations in advance, the transport itself, the storage in our ARTcube and the delivery are precisely timed and planned," explains Georg Csiky, Global Industry Development Manager at Lufthansa Cargo.
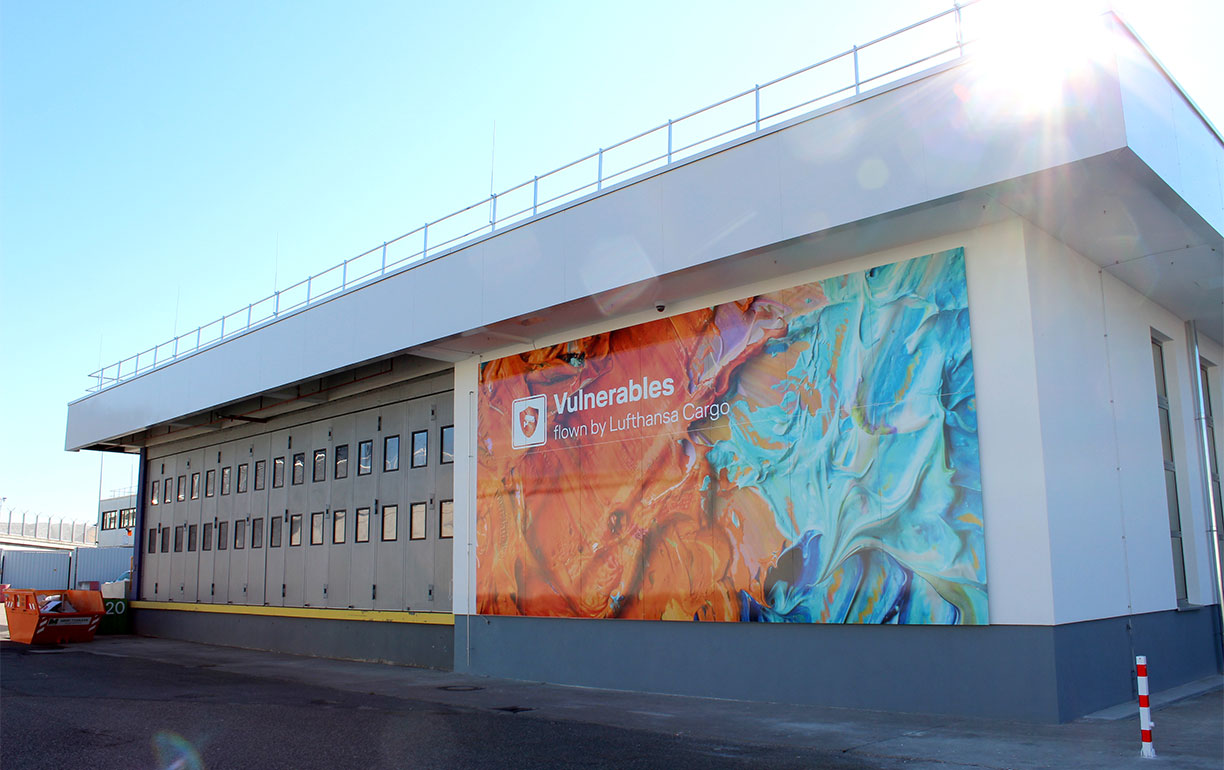
The ARTcube at the Lufthansa Cargo Center in Frankfurt is the perfect storage location for art and valuable goods. It is specially designed to meet the climatic and security requirements. The artworks spent several days in the ARTcube until they were transported to SCHIRN KUNSTHALLE.
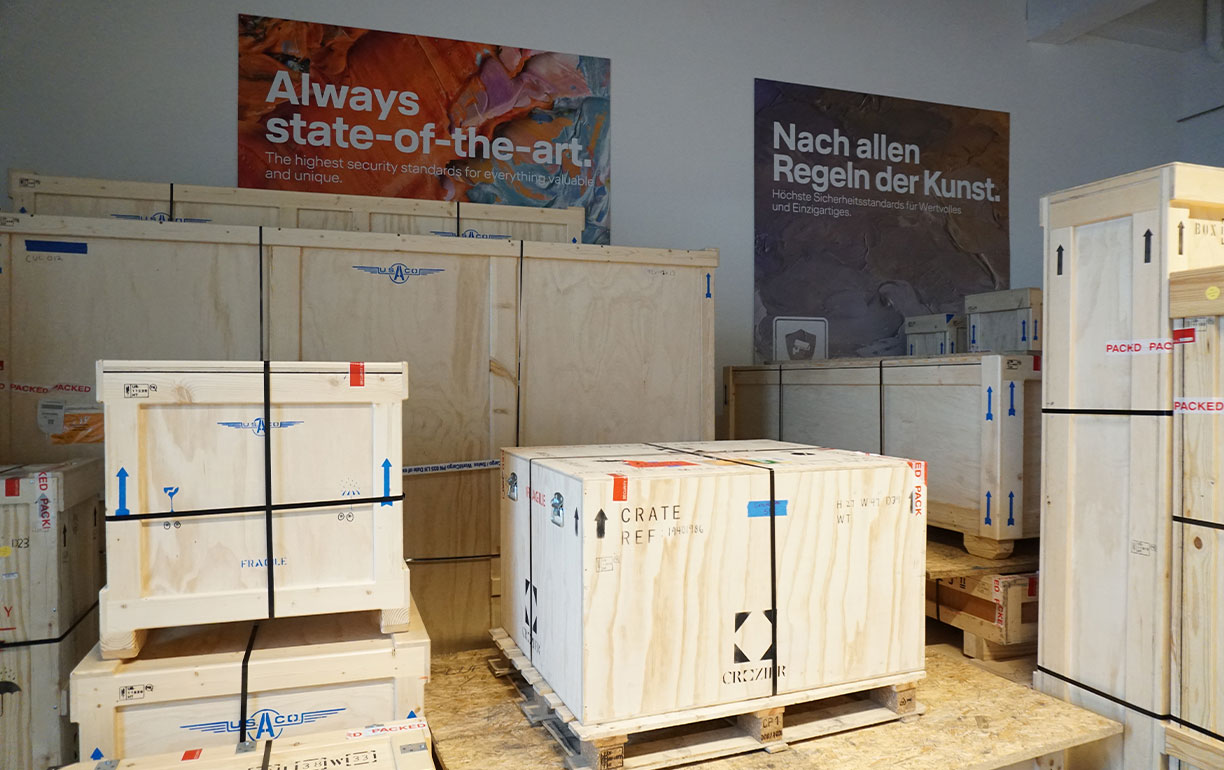
Loading the 62 packages into a truck at the Lufthansa Cargo Center was like playing Tetris. The packages varied greatly in size and weight. The smallest package measured 109 x 89 x 36 cm and weighed 58 kg. The largest package towered over everything at 361 x 33 x 234 cm, and there was also a real heavyweight at 593 kg. "For pieces of this size, transportation in a freighter is the only option," explains Kai Nissen, Head of Aviation and Security Services at CS4Art. CS4Art specializes in the transport of art and ships around 1000 tons of art around the world every year.
"Lufthansa Cargo offers us two main advantages: The experts and the network. In Lufthansa Cargo's handling department, there are supervisors that I have known since 1999. They know exactly what our customers and we need, and what is important to handle fine art shipments in air freight. And Lufthansa Cargo's network is second to none. Nobody has as many connections to and from Europe as the cargo crane," says Kai Nissen on the day of loading, before he has to go back to work. They were looking for a box with a width of about 130 cm. This would fit perfectly into the free space in the truck. | There are special trucks for transporting art. They are equipped with air conditioning, air suspension and various possibilities to straps and fastenings for the works of art in the most secured way. After a smooth arrival at the SCHIRN in downtown Frankfurt, the exhibition was set up for visitors within six days and opened on February 28.
|
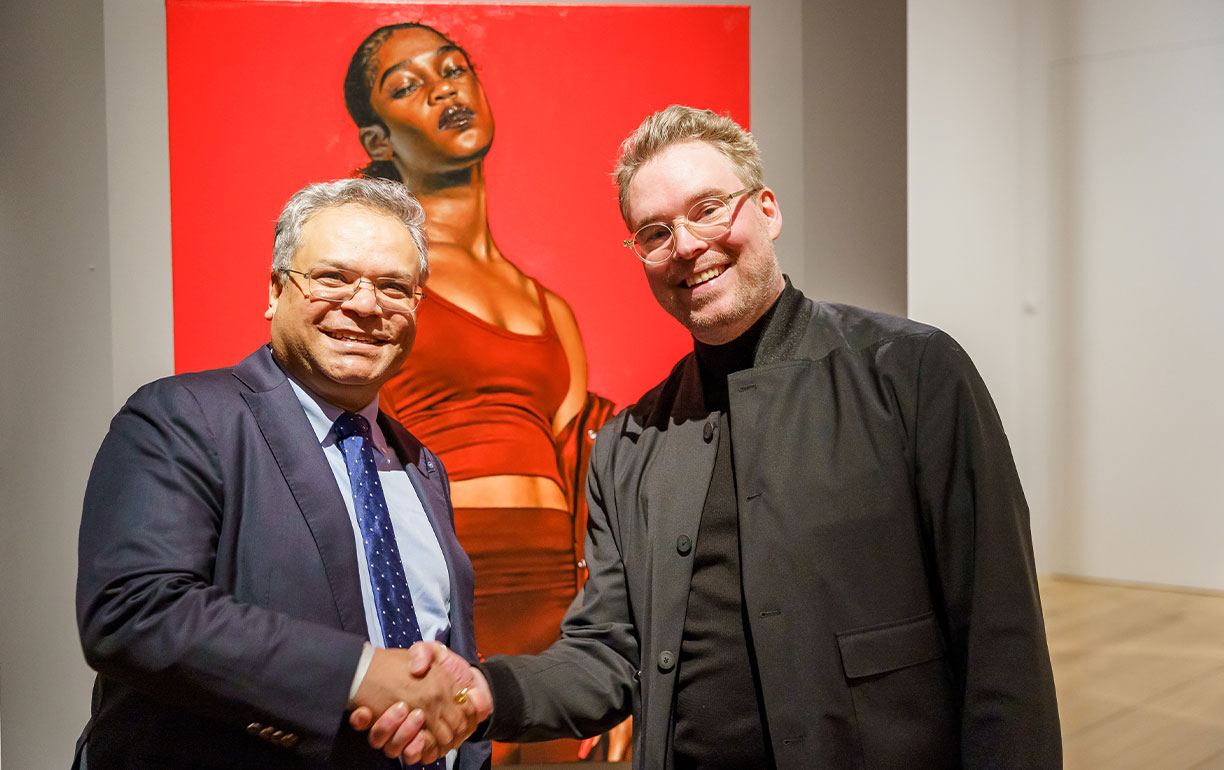
At the opening of the exhibition, Dr. Sebastian Baden, Director of the SCHIRN KUNSTHALLE , also spoke about art on the move: “For the first time this exhibition, THE CULTURE, presents hip hop as global phenomenon and highlights it’s influence on our current artistic and cultural landscape. Thanks to the support of Lufthansa Cargo, it was possible to organize transportation for this extraordinarily relevant international exhibition project more sustainable.”
The SCHIRN used two measures to transport the artworks for THE CULTURE in a sustainable way: 30% of the calculated CO2 emissions were reduced using Sustainable Aviation Fuel (SAF). A further 70% of the calculated CO2 emissions were offset through contributions to high-quality climate protection projects. Lufthansa Cargo offers its customers both options to the extent desired. Lufthansa Cargo CEO Ashwin Bhat was also present at the opening of the exhibition: “It's been a pleasure for Lufthansa Cargo to be the logistic partner of the SCHIRN for their exhibition THE CULTURE. The artwork has been transported via our hub in Chicago to Frankfurt. In Frankfurt, the ARTcube, which is a special warehouse for the artwork has been utilized before the artwork has moved to the SCHIRN. And most important, this artwork was transported sustainably. What a great partnership. Good luck for the exhibition." | After visiting the exhibition, he added: "I don't often have the opportunity to physically experience something that we have transported. To experience these fragile works of art in person here, knowing the expertise and organization behind the transport, also fills me with pride to be part of this work." Carolin Gerstenmaier, Head of Industry Development at Lufthansa Cargo, was also enthusiastic: "This exhibition today, where we are standing at the opening event, is again a great example of Fine Arts being transported in a perfect way with Lufthansa Cargo. What makes this exhibition and the transportation of the artworks even more special is that they are transported in a CO2 compensated way using sustainable aviation fuel combined with other forms of compensation. So today we are not only looking back, taking a glimpse on 50 years of hip hop, but we are also looking forward to a future oriented way of making artwork available to the public by transporting it around the globe in a sustainable way.”
|
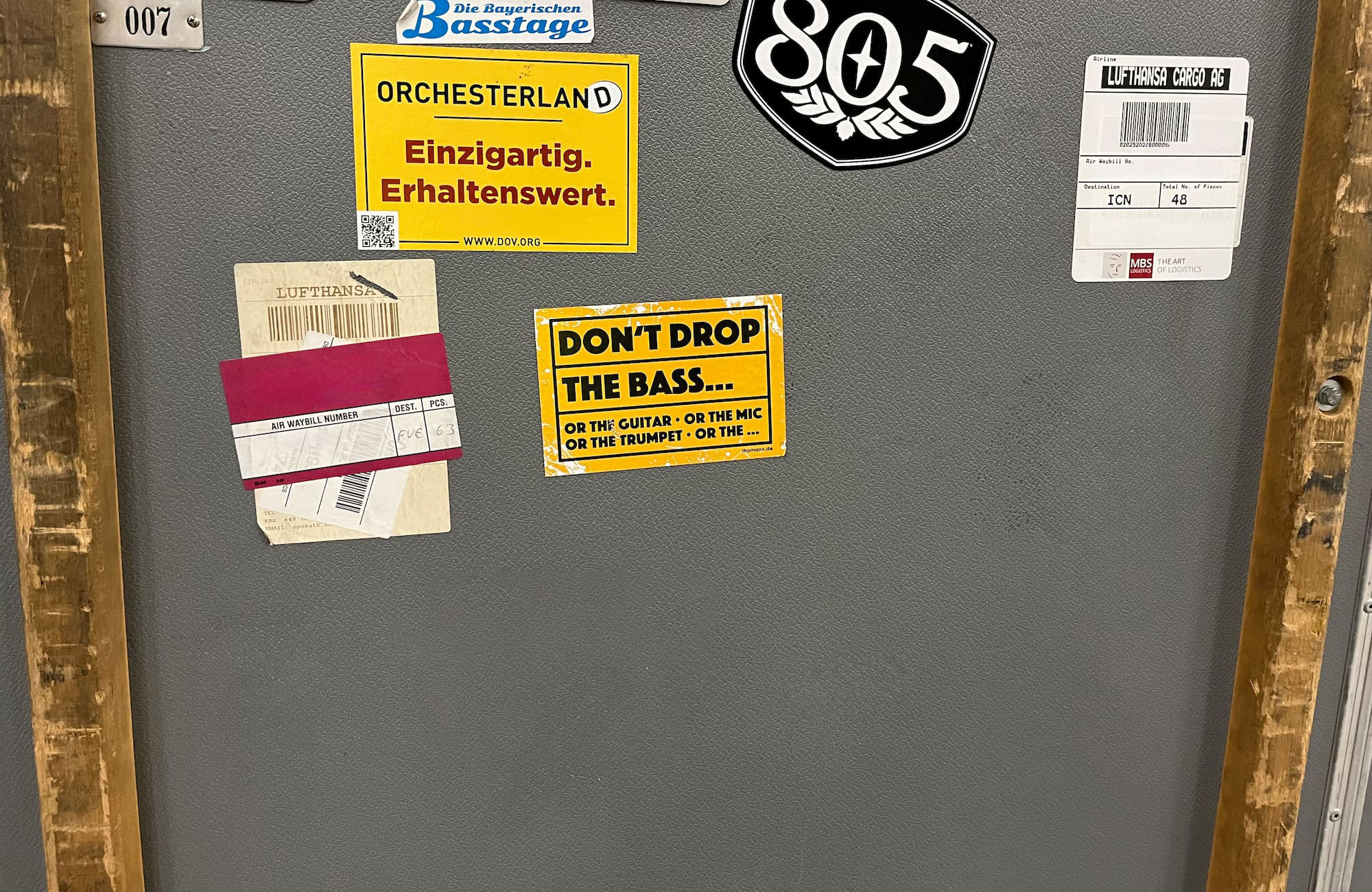
Don't drop the bass
The Munich Philharmonic Orchestra is on its way to Korea. When an orchestra goes on tour, not only the musicians have to travel, but also instruments of various sizes and types. The professionals at Luxreisen and MBS Logistics know exactly what challenges such a trip presents and how to overcome them. Read our full story below.
The security check scanner shows a black item. This transport box needs to be opened. Loadmaster Oliver Putzar is looking for the right key in his waistband to open the 2.14-metre-high crate. A double bass and a tuxedo are revealed behind it. He checks the image on the security scanner again. He has to search the upper right corner of the box. And he immediately finds what he is looking for. The double bass player had forgotten to remove a small deodorant spray. "It happens sometimes," summarizes the logistics specialist from Luxreisen. "But since the explosive detection dog can't get that high into the box, we may have to wipe it down again for the explosive detector."
Securing orchestra cargo is a complex matter that is always accompanied by specialists. They know exactly how to turn and place the crates, how to move the instruments, and they also know the peculiarities of the various orchestras.
"There are orchestras where there is one key to all the transport boxes, and there is nothing in those crates that is not allowed in the cargo. There are 50 crates that go through security and none of them have to be opened. But I've also taken whole cases of beer out of transport boxes. Guest gifts," he adds with a laugh.
At his side is Marius Wyrwa from MBS Logistics. Long before the day of delivery, Marius Wyrwa coordinates the procedure with everyone involved. He puts together a team with representatives from the travel agency, the freight forwarder, the warehouse staff and cargo airline to plan the entire process in detail. He holds all the logistical strings in his hands and is, of course, also on site on the day of delivery, during the security check and the set-up process.
While Oliver Putzar secures the crates together with the warehouse staff and the sniffer dog, Marius Wyrwa is at the customs office in Frankfurt. There are discrepancies regarding a violin bow. The antique piece was still made with ivory elements. Special CITES certificates are required for this, and customs will not accept the one at hand. The bow cannot be taken to Korea and remains in Germany. The musician is informed that he must bring a replacement. Shipping instruments of this class is a highly complex issue, regardless of how the instruments are handled. On the one hand, materials were used in the past that are no longer allowed and must be shipped with special certificates. On the other hand, some instruments are classified as cultural heritage. In this case, an export permit is required to take the instrument abroad.
The security check scanner shows a black item. This transport box needs to be opened. Loadmaster Oliver Putzar is looking for the right key in his waistband to open the 2.14-metre-high crate. A double bass and a tuxedo are revealed behind it. He checks the image on the security scanner again. He has to search the upper right corner of the box. And he immediately finds what he is looking for. The double bass player had forgotten to remove a small deodorant spray. "It happens sometimes," summarizes the logistics specialist from Luxreisen. "But since the explosive detection dog can't get that high into the box, we may have to wipe it down again for the explosive detector." Securing orchestra cargo is a complex matter that is always accompanied by specialists. They know exactly how to turn and place the crates, how to move the instruments, and they also know the peculiarities of the various orchestras. "There are orchestras where there is one key to all the transport boxes, and there is nothing in those crates that is not allowed in the cargo. There are 50 crates that go through security and none of them have to be opened. But I've also taken whole cases of beer out of transport boxes. Guest gifts," he adds with a laugh. |
At his side is Marius Wyrwa from MBS Logistics. Long before the day of delivery, Marius Wyrwa coordinates the procedure with everyone involved. He puts together a team with representatives from the travel agency, the freight forwarder, the warehouse staff and cargo airline to plan the entire process in detail. He holds all the logistical strings in his hands and is, of course, also on site on the day of delivery, during the security check and the set-up process. While Oliver Putzar secures the crates together with the warehouse staff and the sniffer dog, Marius Wyrwa is at the customs office in Frankfurt. There are discrepancies regarding a violin bow. The antique piece was still made with ivory elements. Special CITES certificates are required for this, and customs will not accept the one at hand. The bow cannot be taken to Korea and remains in Germany. The musician is informed that he must bring a replacement. Shipping instruments of this class is a highly complex issue, regardless of how the instruments are handled. On the one hand, materials were used in the past that are no longer allowed and must be shipped with special certificates. On the other hand, some instruments are classified as cultural heritage. In this case, an export permit is required to take the instrument abroad. |
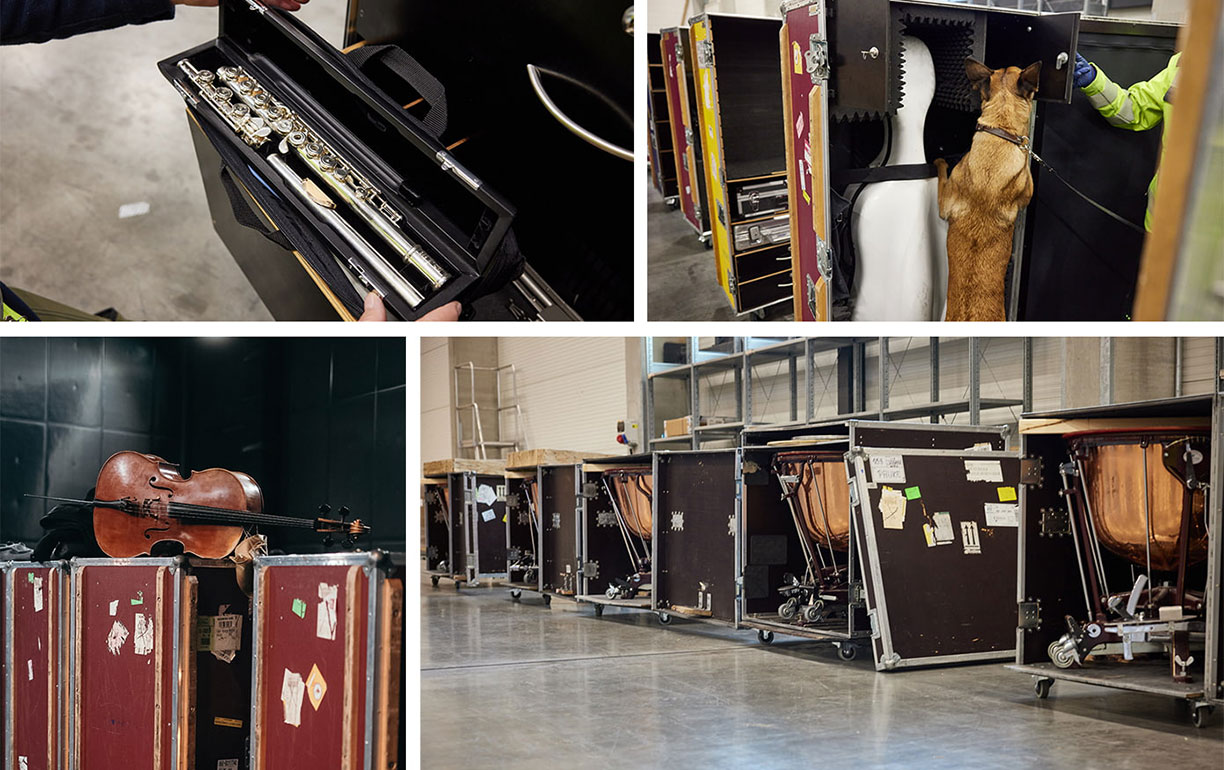
A glance into the transport boxes reveals instruments of all shapes, sizes and materials. The sniffer dog is unimpressed and fully focused on his target.
"Most people think about avoiding vibrations and certain temperature conditions when transporting instruments. These are important criteria. We can rely on Lufthansa Cargo's handling here. However, the real challenge is to handle the size of the shipment and all the formal requirements within a very tight time frame," explains Oliver Hamacher, Head of Airfreight at Cologne-based freight forwarder MBS Logistics.
The last orchestra rehearsal often takes place the evening before delivery at the airport. Another rehearsal and the first concert follow the day after arrival in the destination country. With a schedule like this, nothing can go wrong - from the special care during handling, to the securing according to LBA specifications, to the packing of the 48 pieces on just five special 3x2.1m loading pallets, to the delivery.
Hamacher admits that he is not the greatest music connoisseur. But he knows a lot about transporting instruments. Several times a year, the freight forwarder MBS Logistics organizes such shipments all over the world.
Lufthansa Cargo is also very familiar with the customs of transporting instruments. "We have a special and cooperative relationship with Lufthansa Cargo. Our colleagues are very familiar with the special requirements of these transports. We are therefore in close contact, which is very important for highly specialized instrument transports," says Hamacher.
For this shipment, MBS Logistics relies on the Lufthansa Cargo product Vulnerables in combination with the speed td.Flash. Vulnerables offers high security precautions, handling, storage and transport appropriate to the type of goods, and seamless traceability and monitoring. On request, the shipment can be personally accompanied during handling in Frankfurt. td.Flash is not limited by weight or size and offers the required speed and guaranteed capacity thanks to late acceptance and short transit times.
"Most people think about avoiding vibrations and certain temperature conditions when transporting instruments. These are important criteria. We can rely on Lufthansa Cargo's handling here. However, the real challenge is to handle the size of the shipment and all the formal requirements within a very tight time frame," explains Oliver Hamacher, Head of Airfreight at Cologne-based freight forwarder MBS Logistics. The last orchestra rehearsal often takes place the evening before delivery at the airport. Another rehearsal and the first concert follow the day after arrival in the destination country. With a schedule like this, nothing can go wrong - from the special care during handling, to the securing according to LBA specifications, to the packing of the 48 pieces on just five special 3x2.1m loading pallets, to the delivery. Hamacher admits that he is not the greatest music connoisseur. But he knows a lot about transporting instruments. Several times a year, the freight forwarder MBS Logistics organizes such shipments all over the world. |
Lufthansa Cargo is also very familiar with the customs of transporting instruments. "We have a special and cooperative relationship with Lufthansa Cargo. Our colleagues are very familiar with the special requirements of these transports. We are therefore in close contact, which is very important for highly specialized instrument transports," says Hamacher. For this shipment, MBS Logistics relies on the Lufthansa Cargo product Vulnerables in combination with the speed td.Flash. Vulnerables offers high security precautions, handling, storage and transport appropriate to the type of goods, and seamless traceability and monitoring. On request, the shipment can be personally accompanied during handling in Frankfurt. td.Flash is not limited by weight or size and offers the required speed and guaranteed capacity thanks to late acceptance and short transit times.
|
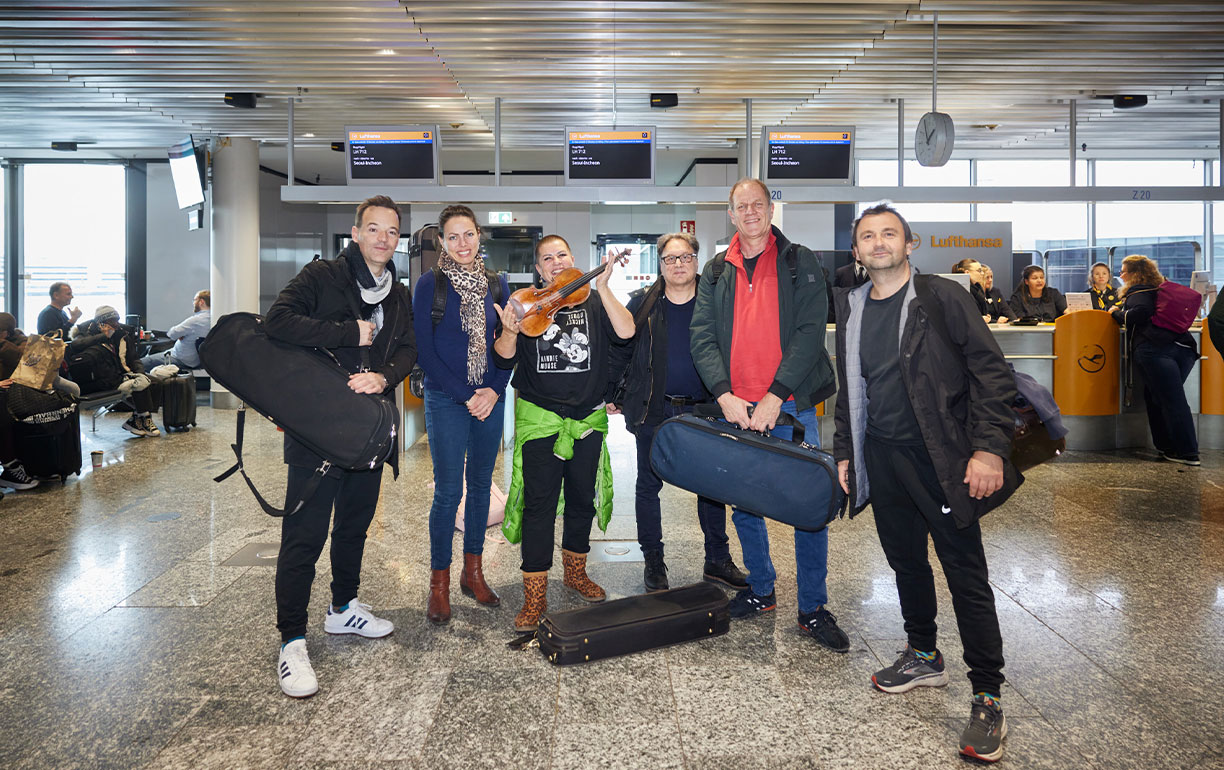
"Some instruments are not even in the cargo hold," says Annette Lux the next day when she meets the orchestra at the gate in Frankfurt, where they are waiting for their onward flight to Seoul on LH712. "In most cases, the musicians carry a Stradivarius with them. This can be for insurance reasons, but depending on the size of the instrument, the musicians don't want to let it out of their hands. Or they don't want to be without it for a few days for their own rehearsals." At the gate, you can also see many instrument cases on the backs and in the hands of orchestra members: violas, violins, trumpets, and oboes. "But I've also booked a seat for a cello several times in the past," says the business graduate, who has been accompanying orchestras since she was a child.
In 1972, her father founded Luxreisen - a travel agency specializing in choir and orchestra tours. In 1997, she became the second generation to take over Luxreisen - together with her sister Brigitta Lux since 2000. To this day, there are not many operators at the level of Luxreisen - about six in Europe and about ten worldwide - that can organize trips of this size and quality.
When you talk to Lux about her work, you immediately realize that her passion and profession go hand in hand. "I am motivated by the idea of bringing music and beautiful experiences into the world. Music is international understanding... more important than ever in this day and age.”
In 1972, her father founded Luxreisen - a travel agency specializing in choir and orchestra tours. In 1997, she became the second generation to take over Luxreisen - together with her sister Brigitta Lux since 2000. To this day, there are not many operators at the level of Luxreisen - about six in Europe and about ten worldwide - that can organize trips of this size and quality. |
When you talk to Lux about her work, you immediately realize that her passion and profession go hand in hand. "I am motivated by the idea of bringing music and beautiful experiences into the world. Music is international understanding... more important than ever in this day and age.” |
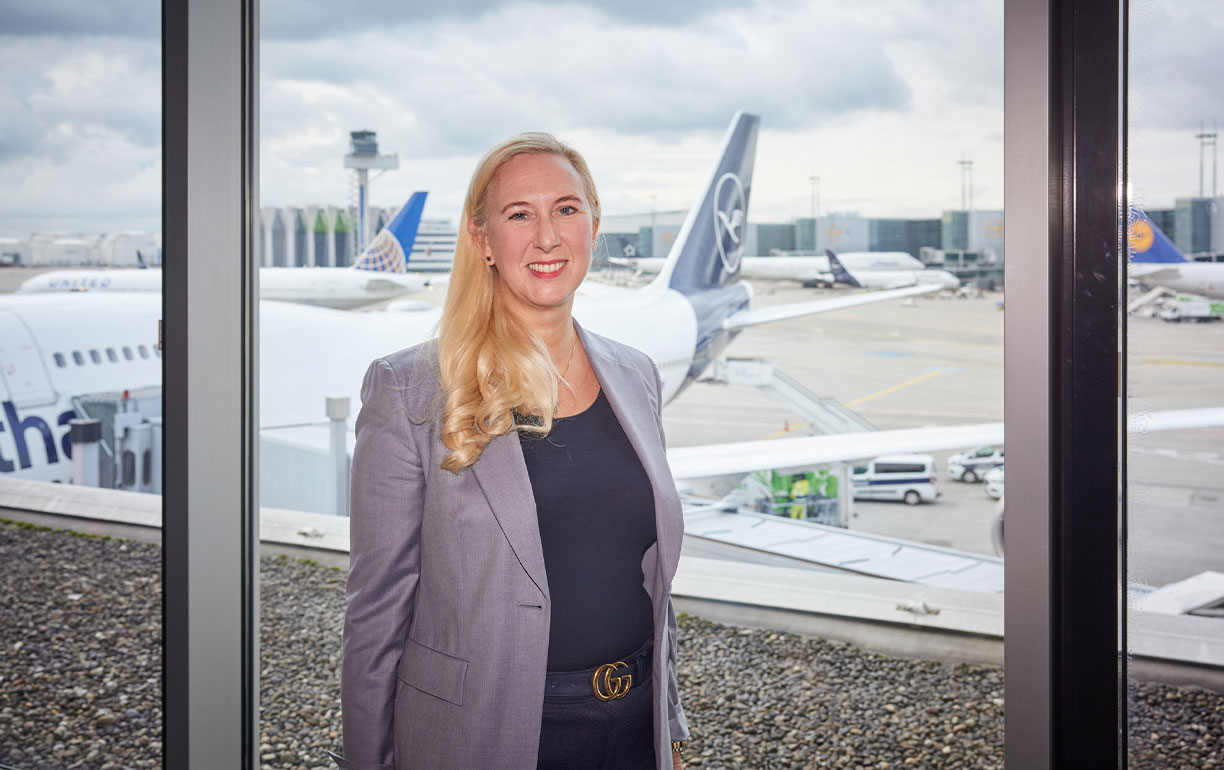
She has particularly fond memories of a concert by the Bamberg Symphony Orchestra, who were guests at the Teatro del Lago in Frutillar in southern Chile. "The concert hall is one of the most extraordinary in the world, located directly on a lake and next to a volcano. The setting is impressive. The orchestra was picked up in Rio by the Chilean president's Boeing 767. That was impressive too," she smiles.
Killian Geppert, stage manager of the Munich Philharmonic Orchestra, also has fond memories of special concerts. "We once had a special concert in Buenos Aires, right next to the obelisk. An eight-lane road was closed for the open-air concert, so there was room for 25,000 spectators." Memories like these make the enormous effort behind the travel organization worthwhile.
When asked if anything ever goes wrong, there are equally interesting stories to tell. Lux tells of a pallet of timpani that could not be taken on board due to the trim. The timpani arrived in Sao Paulo with a last-minute delivery. A concert without timpani roll? Unthinkable.
Lux also recalls a trip to the USA: "I once had an orchestra that was stuck in New York. They were supposed to play a concert in Florida, but in the morning a blizzard hit New York, shutting down air traffic. The first aircraft were able to take off in the afternoon, but all flights for the next three days were fully booked and we needed almost 100 seats for the musicians. Force majeure is no excuse. In my business, there are no problems, only solutions. The orchestra has to be there. In fact, we were able to arrange a charter flight on short notice, and the orchestra landed in Vero Beach in time for the concert."
Killian Geppert, stage manager of the Munich Philharmonic Orchestra, also has fond memories of special concerts. "We once had a special concert in Buenos Aires, right next to the obelisk. An eight-lane road was closed for the open-air concert, so there was room for 25,000 spectators." Memories like these make the enormous effort behind the travel organization worthwhile. When asked if anything ever goes wrong, there are equally interesting stories to tell. Lux tells of a pallet of timpani that could not be taken on board due to the trim. The timpani arrived in Sao Paulo with a last-minute delivery. A concert without timpani roll? Unthinkable. |
Lux also recalls a trip to the USA: "I once had an orchestra that was stuck in New York. They were supposed to play a concert in Florida, but in the morning a blizzard hit New York, shutting down air traffic. The first aircraft were able to take off in the afternoon, but all flights for the next three days were fully booked and we needed almost 100 seats for the musicians. Force majeure is no excuse. In my business, there are no problems, only solutions. The orchestra has to be there. In fact, we were able to arrange a charter flight on short notice, and the orchestra landed in Vero Beach in time for the concert." |
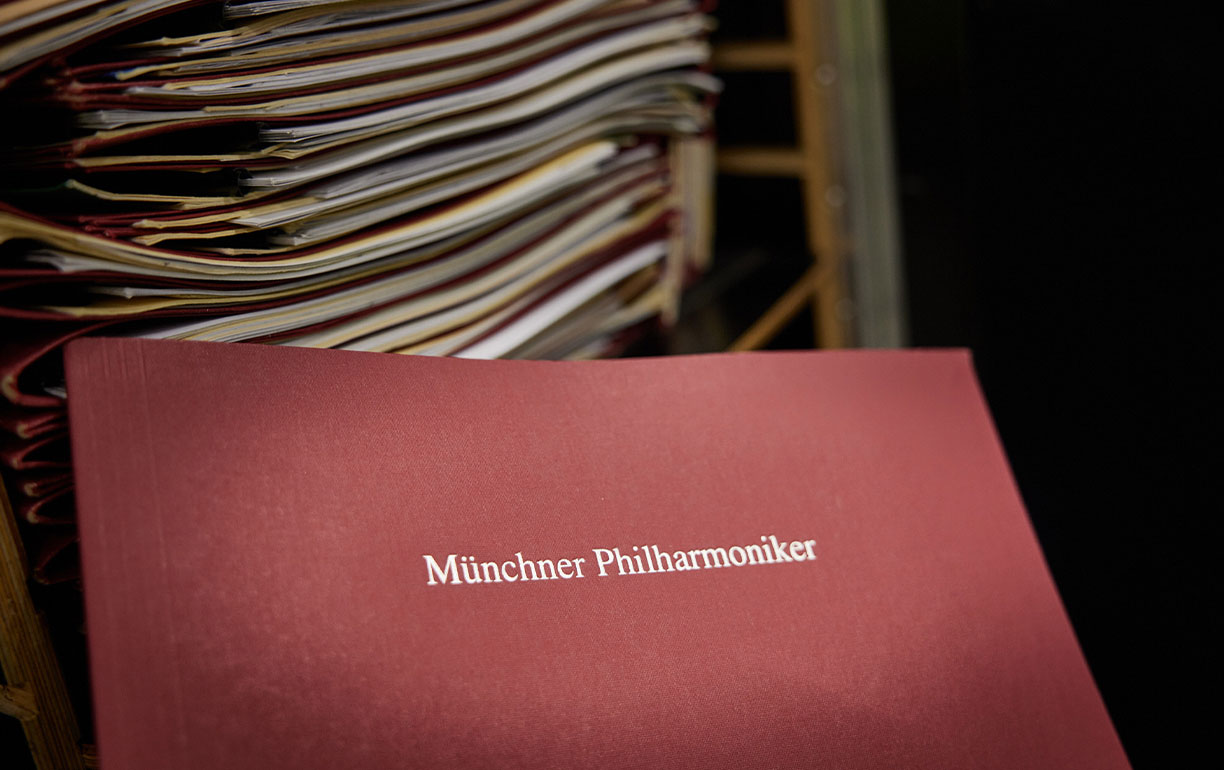
A service that does not go unnoticed by the Munich Philharmonic Orchestra. "We have been working with Luxreisen since the 1980s. They are incredibly competent, experienced, and reliable and can solve any situation, no matter how tricky," summarizes Killian Geppert.
It was precisely these exceptional situations that led her to choose MBS Logistics and Lufthansa Cargo. "For logistics on this scale, I need fixed contacts who know their way around," says the entrepreneur. "In the big forwarding companies of this world, I'm just an air waybill number and often get stuck in very rigid processes. MBS Logistics is a medium-sized, owner-managed forwarding company. Here I have personal contacts who think along with me and see our transport as a project and not as their daily task. Of course, my main concern is that everything goes according to plan. But no freight forwarder or airline can predict capricious weather conditions, for example. If there are any irregularities, I need a direct contact person who immediately understands what we need. That's important to me.”
Airfreight specialist Hamacher can confirm this: "The special thing about MBS Logistics is its family character. We are defined by our employees and our closeness to our customers. We know our customers and they know us. We are contact persons, and we know the needs of our customers. This is what the face in our logo stands for. It stands for every single member of our team. At Lufthansa Cargo, I also get this partnership-based cooperation with a fixed contact person who understands our needs."
At Lufthansa Cargo, that person is Dirk Müller-Glissmann and the Sales Team Germany West. "I am very pleased that our customers also feel that behind every eAWB and every process there is a person who takes care of them and makes sure that everything runs smoothly, even though a lot has changed and become more digital in our environment."
The freight forwarder and travel agency are also noticing the changes. Hamacher compares: "A lot of things that used to be done manually are now done electronically. For example, hardly any shipments are accompanied by a paper waybill. The air waybill data is transmitted digitally from the freight forwarder to the airline and then from the airline to the destination airport. In most cases, customs clearance is also automated via interfaces between the forwarding software and the customs system. Lufthansa Cargo has always been a driver of digitalization in the aviation industry. It makes a lot of things easier and more efficient."
Digitalization has also changed a lot for Annette Lux. Until 2007, she traveled on almost every tour. In 2023, she was only present on three out of 110 organized tours. "A lot has changed and is often better managed from home than on the road," she says of the digitalization of her industry. "But a real concert experience cannot be digitized." As a result, countless tours are already in the pipeline for 2024. The Munich Philharmonic Orchestra started the year with a tour to Spain and a trip to the USA, where they performed Brahms at the famous Carnegie Hall in New York.
Both the Philharmonic and Ms. Lux have dream concerts and trips in mind. For the Bavarian capital's Philharmonic, it is an open-air concert at the foot of Table Mountain or Machu Picchu. For Annette Lux, a dream will come true next year when the Bamberg Symphony Orchestra makes a stop in Iceland on its way to the United States. "I have always wanted to visit the Harpa Concert Hall in Reykjavik with its fiery red interior. I will be traveling to Iceland again at my own request," says Ms. Lux happily.
Table Mountain, Machu Picchu or Iceland. Lufthansa Cargo is happy to fly the instruments to concert halls all over the world.
It was precisely these exceptional situations that led her to choose MBS Logistics and Lufthansa Cargo. "For logistics on this scale, I need fixed contacts who know their way around," says the entrepreneur. "In the big forwarding companies of this world, I'm just an air waybill number and often get stuck in very rigid processes. MBS Logistics is a medium-sized, owner-managed forwarding company. Here I have personal contacts who think along with me and see our transport as a project and not as their daily task. Of course, my main concern is that everything goes according to plan. But no freight forwarder or airline can predict capricious weather conditions, for example. If there are any irregularities, I need a direct contact person who immediately understands what we need. That's important to me.” Airfreight specialist Hamacher can confirm this: "The special thing about MBS Logistics is its family character. We are defined by our employees and our closeness to our customers. We know our customers and they know us. We are contact persons, and we know the needs of our customers. This is what the face in our logo stands for. It stands for every single member of our team. At Lufthansa Cargo, I also get this partnership-based cooperation with a fixed contact person who understands our needs." At Lufthansa Cargo, that person is Dirk Müller-Glissmann and the Sales Team Germany West. "I am very pleased that our customers also feel that behind every eAWB and every process there is a person who takes care of them and makes sure that everything runs smoothly, even though a lot has changed and become more digital in our environment." |
The freight forwarder and travel agency are also noticing the changes. Hamacher compares: "A lot of things that used to be done manually are now done electronically. For example, hardly any shipments are accompanied by a paper waybill. The air waybill data is transmitted digitally from the freight forwarder to the airline and then from the airline to the destination airport. In most cases, customs clearance is also automated via interfaces between the forwarding software and the customs system. Lufthansa Cargo has always been a driver of digitalization in the aviation industry. It makes a lot of things easier and more efficient." Digitalization has also changed a lot for Annette Lux. Until 2007, she traveled on almost every tour. In 2023, she was only present on three out of 110 organized tours. "A lot has changed and is often better managed from home than on the road," she says of the digitalization of her industry. "But a real concert experience cannot be digitized." As a result, countless tours are already in the pipeline for 2024. The Munich Philharmonic Orchestra started the year with a tour to Spain and a trip to the USA, where they performed Brahms at the famous Carnegie Hall in New York. Both the Philharmonic and Ms. Lux have dream concerts and trips in mind. For the Bavarian capital's Philharmonic, it is an open-air concert at the foot of Table Mountain or Machu Picchu. For Annette Lux, a dream will come true next year when the Bamberg Symphony Orchestra makes a stop in Iceland on its way to the United States. "I have always wanted to visit the Harpa Concert Hall in Reykjavik with its fiery red interior. I will be traveling to Iceland again at my own request," says Ms. Lux happily. Table Mountain, Machu Picchu or Iceland. Lufthansa Cargo is happy to fly the instruments to concert halls all over the world. |
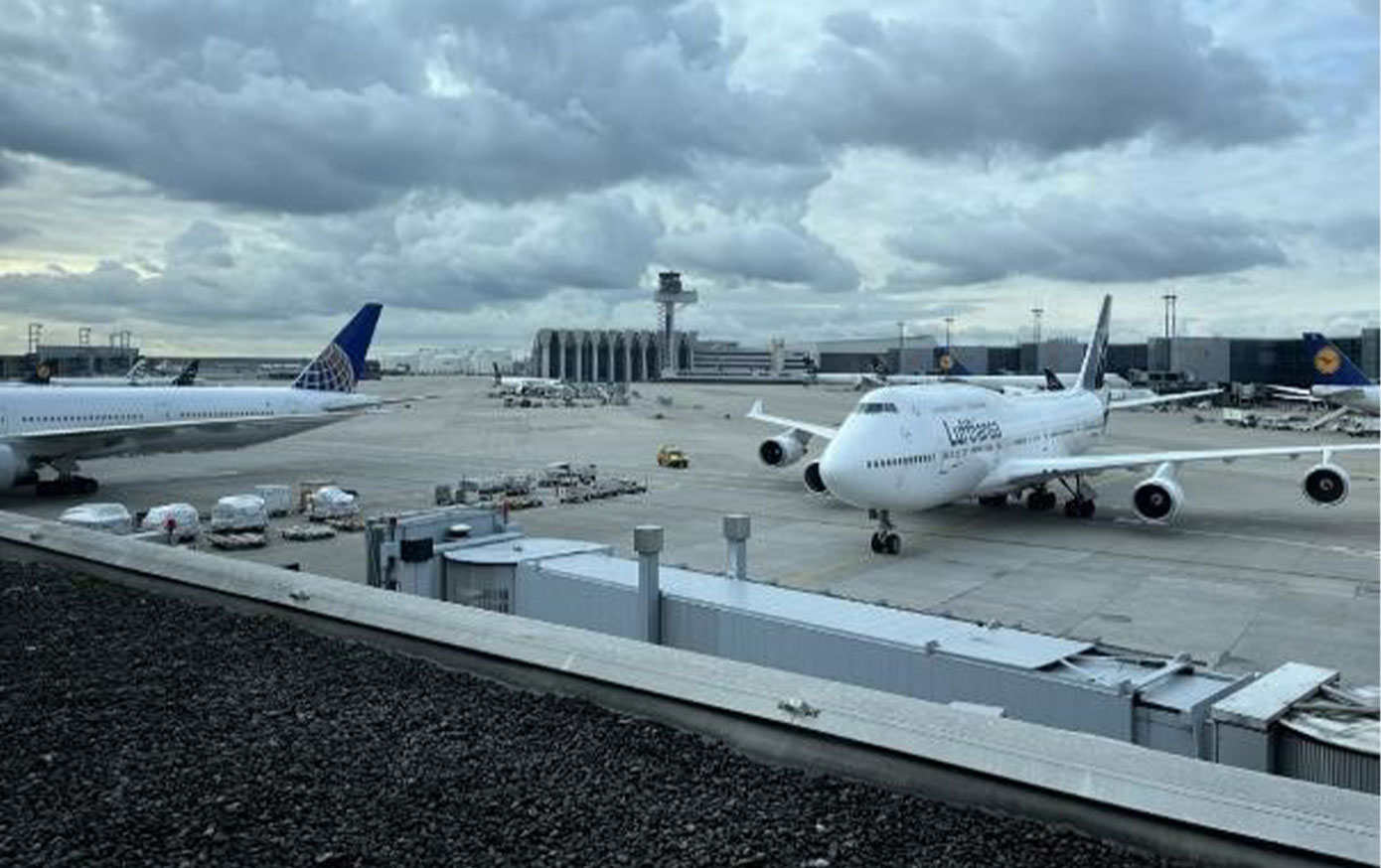
The instruments fly in the cargo hold of the Boeing 747 passenger plane on this journey. On the left, the pallets are already waiting for the arriving aircraft.
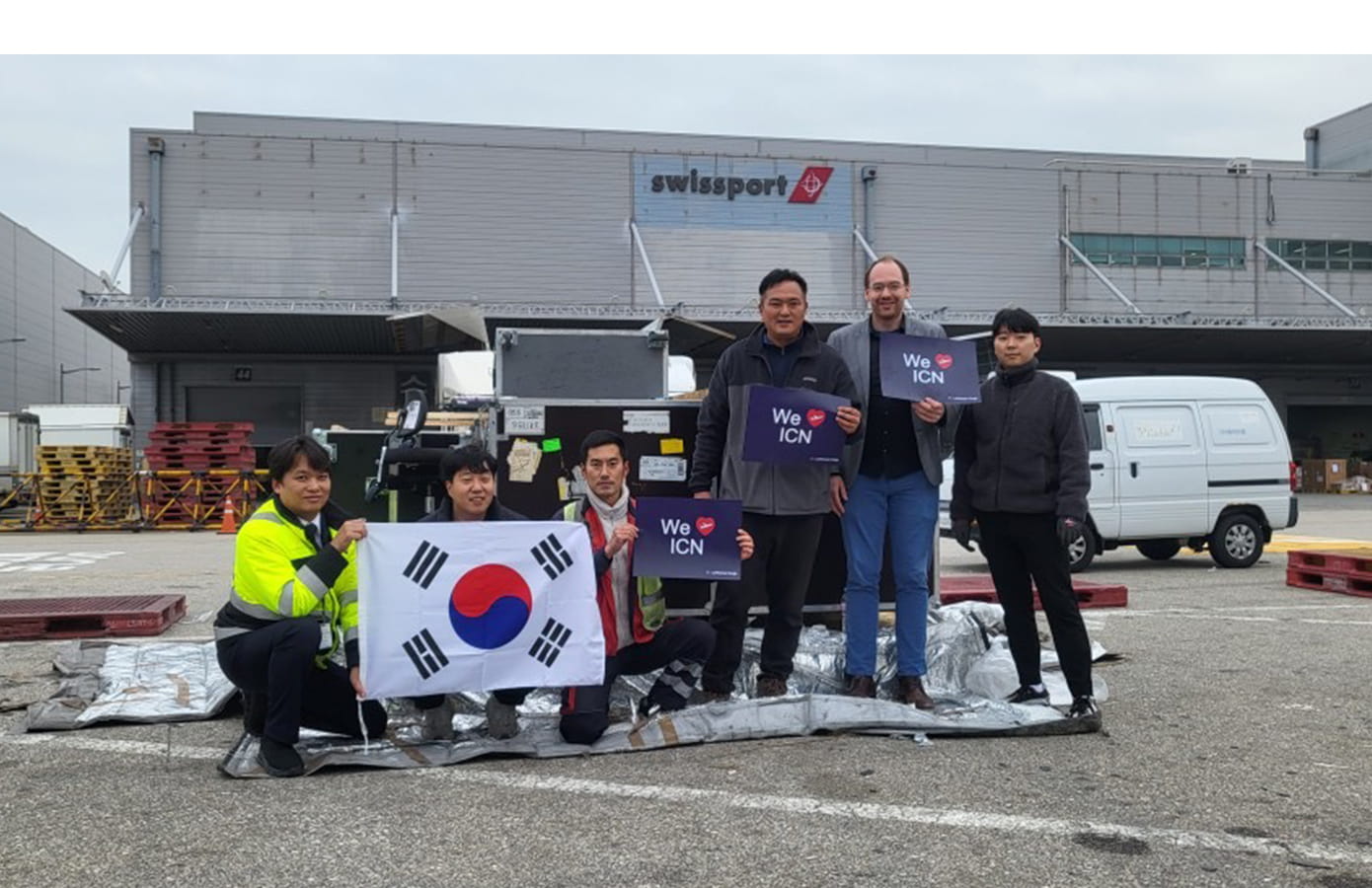
The colleagues in Seoul are also delighted with the Munich Philharmonic's special cargo, here at the breakdown with stage manager Killian Geppert.
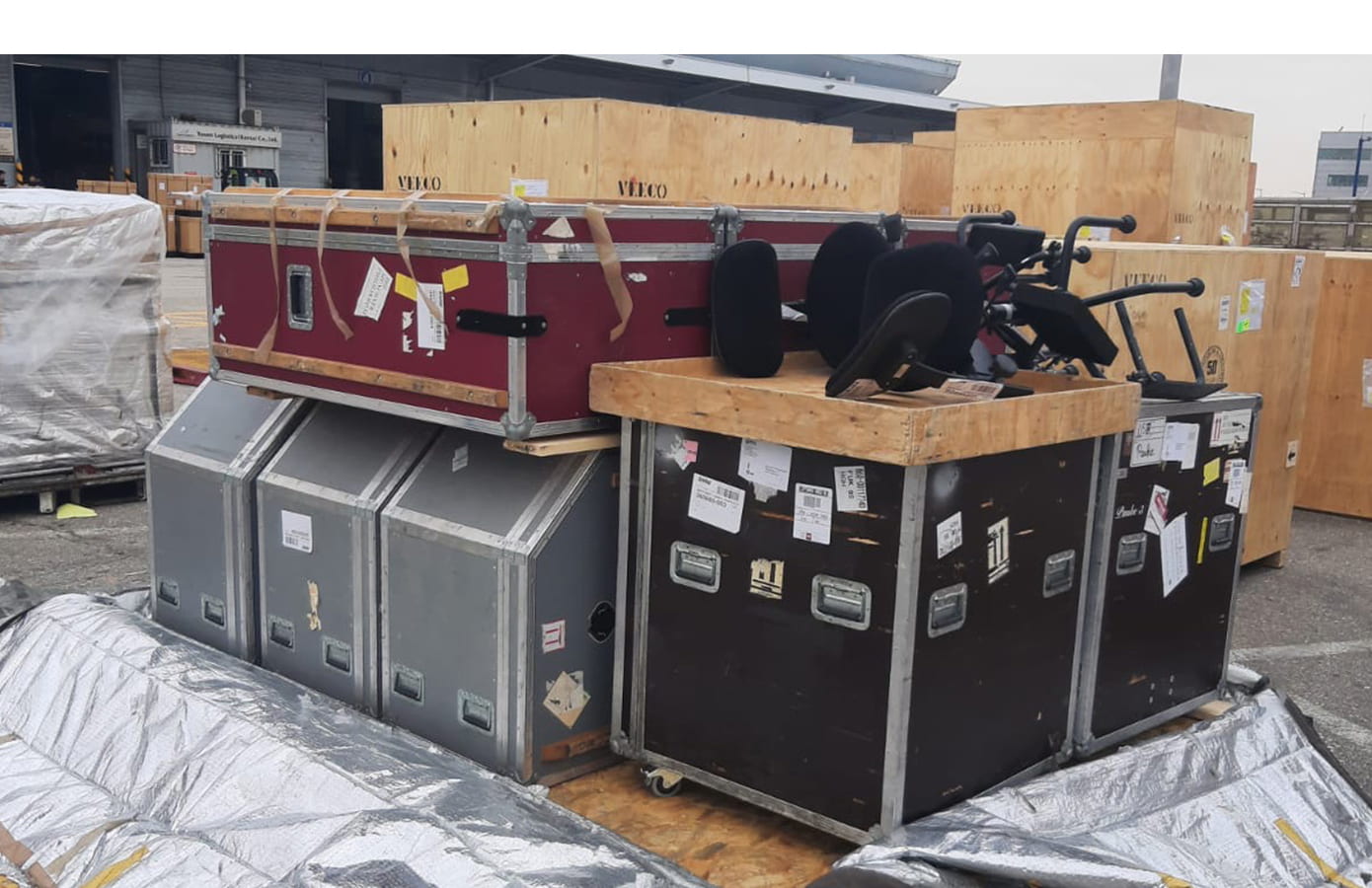
The build-up may remind a little of a Tetris game. The team managed to fit 48 parts onto five pallets. Here, the thermal covers have just been removed and the freight is being loaded onto the trucks for onward transportation in Korea.
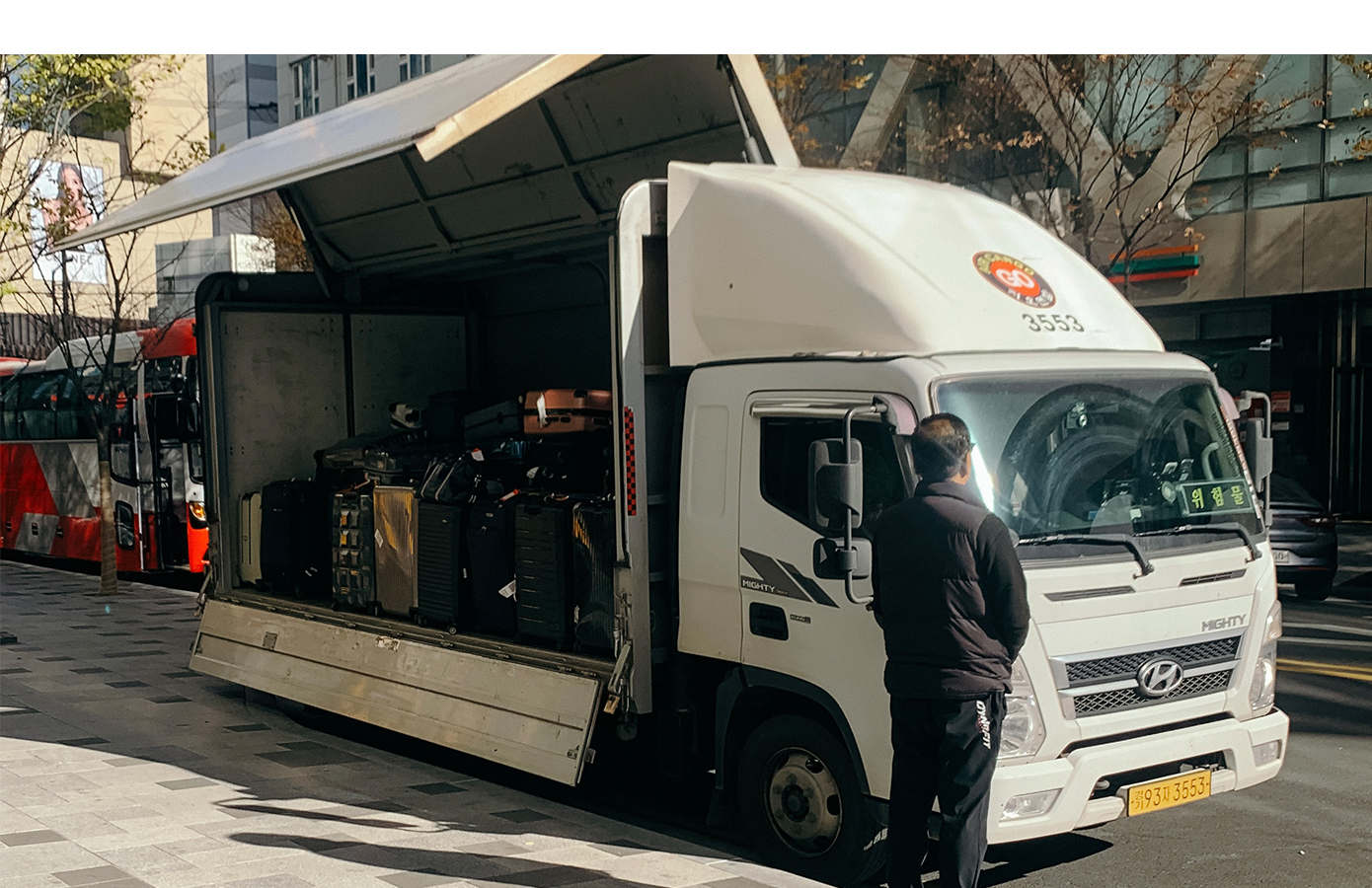
The logistics continue on site. The instruments are transported between six concert halls in Seoul, Sejong, Gwangju, Daejeon and Daegu.
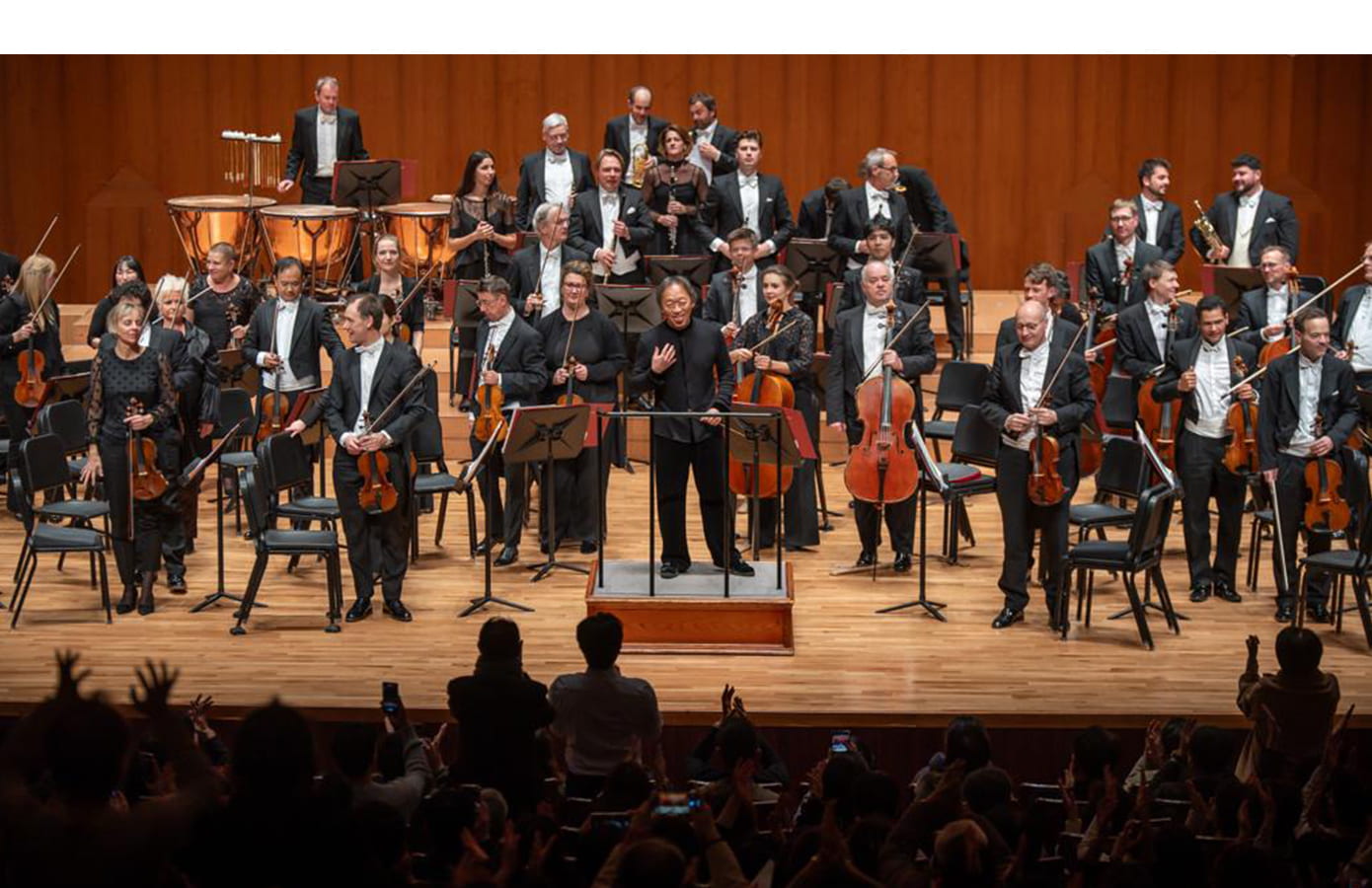
The Philharmonic Orchestra gave a total of seven concerts in eight days. All were conducted by Seoul-born conductor Myung-Whun Chung. The orchestra performed together with guest violinist Clara-Jumi Kang and guest pianist Yunchan Lim. They played works by Beethoven.
Photos: Münchner Philharmoniker, Uli Neumann-Cosel, Killian Geppert, Oliver Rösler, Lufthansa Cargo, Won Hee Lee, Sejong Center
Published 04/2024
Photos: Münchner Philharmoniker, Uli Neumann-Cosel, Killian Geppert, Oliver Rösler, Lufthansa Cargo, Won Hee Lee, Sejong Center
Published 04/2024
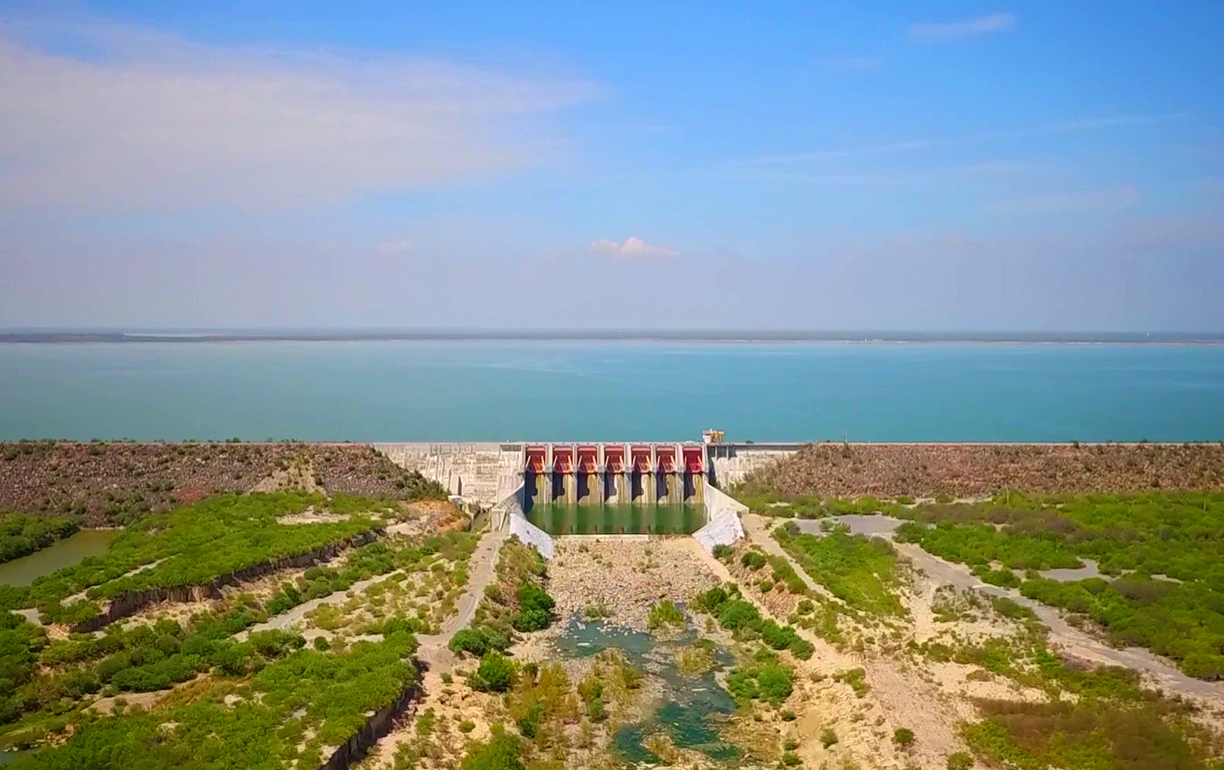
Logistics flowing like water
Not everyone takes it for granted to open the tap and let fresh water flow. The inhabitants of the state of Nuevo Léon in Mexico also have to struggle with water shortages. In the summer of 2022, the region was hit by a severe drought. Some of the dams that supply water to the region of 5.3 million people had reached less than 1% capacity. Water consumption by private households was severely limited and water trucks drove to the hardest-hit areas to distribute water to residents, but civil unrest was already developing over the distribution of the precious wet.
You can watch on this project on the YouTube channel of Lufthansa Cargo: https://youtu.be/0FVh6MgnBsE
The government had to find a solution to this existential challenge. In July 2022, the government of Nuevo Leon announced the start of the "El Cuchillo II" construction project. To be completed in a record time of less than a year, the project will then bring 5,000 liters of water per second over 110 kilometers from the small Mexican town of China to the metropolis of Monterrey. |
The ten construction companies involved, three piping companies, the steel companies and also the pump manufacturer "Ruhrpumpen" all come from the state of Nuevo Leon.
|
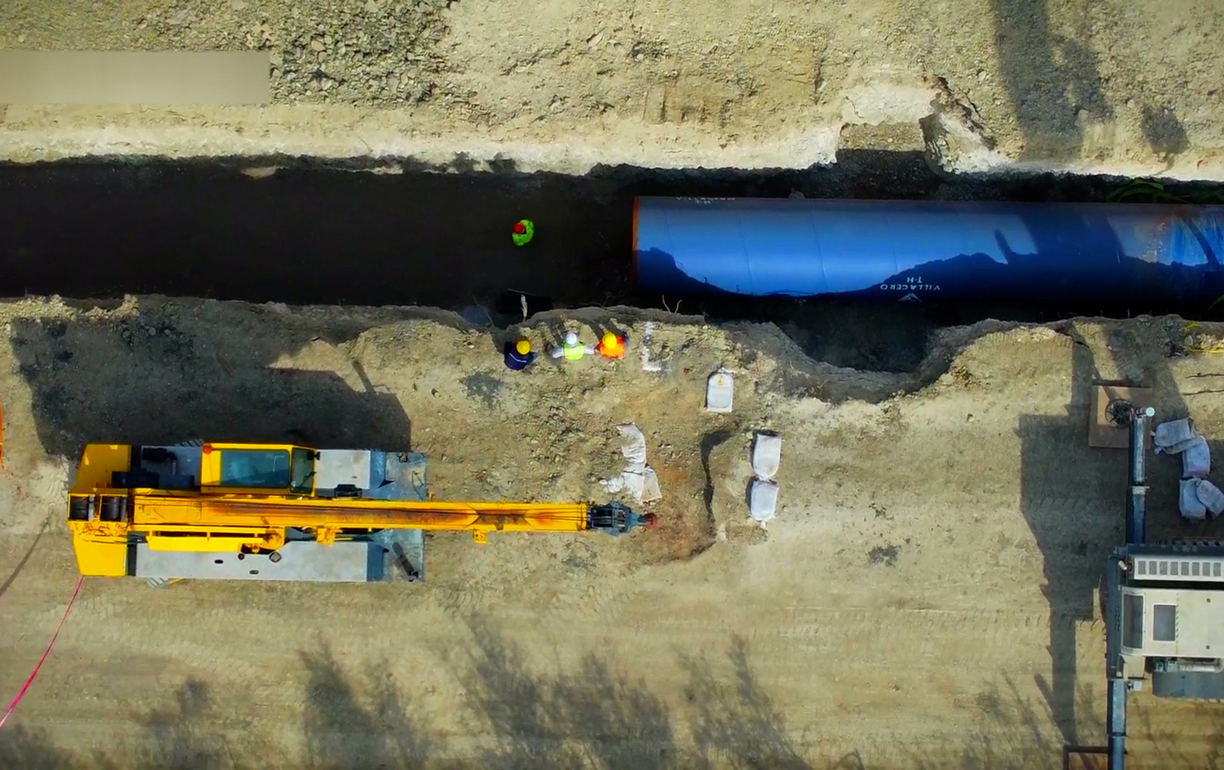
"Ruhrpumpen" with its headquarters in Monterrey does not sound very Mexican at first. But it conceals an impressive history of Mexican entrepreneurship. In 1997, Ruhrpumpen from Witten was bought by Cesar A. Elizondo Villarreal, who was the first Mexican entrepreneur ever to invest in a German industrial company.
Today, the pump manufacturer has production facilities in ten countries around the globe. The close cooperation between Mexico and Germany still exists. Jose Luis Martinez Gonzalez, Global Logistics Director at Ruhrpumpen, also appreciates the close cooperation: "We come from Monterrey, the industrial heart of Mexico, with a well-known strong work ethic. |
Our colleagues in Germany have first-class technical experience. Side by side, we join forces and have been able to create a strong conglomerate that allows us to grow together, learn from each other and build a strong partnership to spread in different countries, with one mission: to be the supplier of choice for our customers."
|
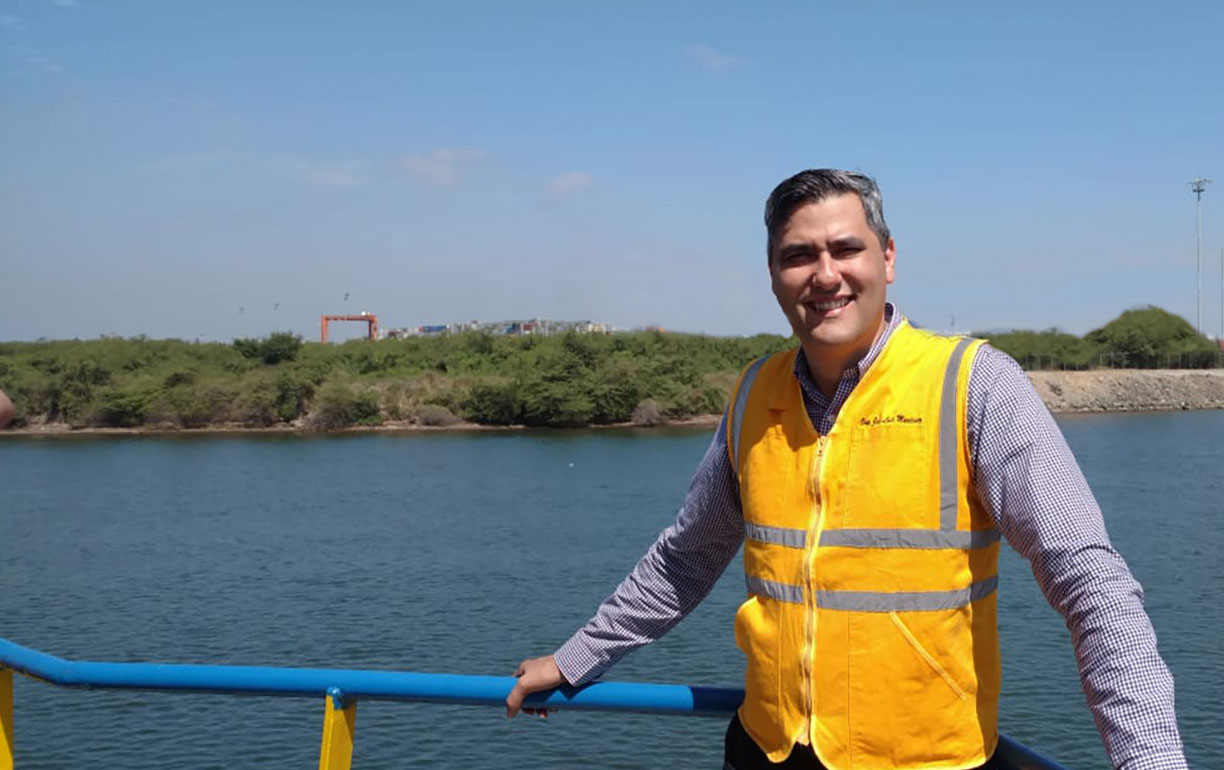
"The ease of doing business with us is what defines our company. We're a family-owned and -run business that makes decisions quickly and always puts our customers' needs first."
Jose Luis Martinez Gonzalez, Global Logistics Director, Ruhrpumpen
Martinez Gonzalez knows that Ruhrpumpen was not only chosen for its proximity: "Time is of the essence in this project. The biggest challenge is planning and allocating all resources to the day in order to complete such an important project in record time. Our corporate culture is also an advantage here: we make decisions within days, while others take months. We have plants in the same locations as our competitors and similar products and manufacturing costs, but what differentiates us is our flexibility and the speed with which we work." The valves of the required pumps for the construction of the dam are manufactured in Germany. The pump manufacturer Ruhrpumpen chose the German forwarder H.J. Schryver & Co for the transport services, which they already knew from other projects. The logistics manager of Ruhrpumpen sums up the selection process: "We were looking for motivated and expert partners who understand the meaning of this project and who would enable us to transport the required components from the other side of the world within a few days. |
A delay on our side could have an impact on several tasks during construction and a very sophisticated plan would be thrown into disarray." Hamburg-based logistics company Schryver also has a close relationship with South America. "We are represented in nine countries in Latin America with the Schryver brand," says Carsten Schryver, Managing Partner of the company. "Hamburg was and is a gateway to the world. And Hamburg's connection with Latin America has brought together tradesmen and women and companies for centuries. This has given rise to business opportunities, then small outposts of Schryver, and now independent organizations with a total of more than 300 employees." Schryver serves very diverse markets in this region. In Brazil and Mexico, they operate in industrially developed countries. In Ecuador and Peru, they often work with large suppliers of mining products or food manufacturers.
|
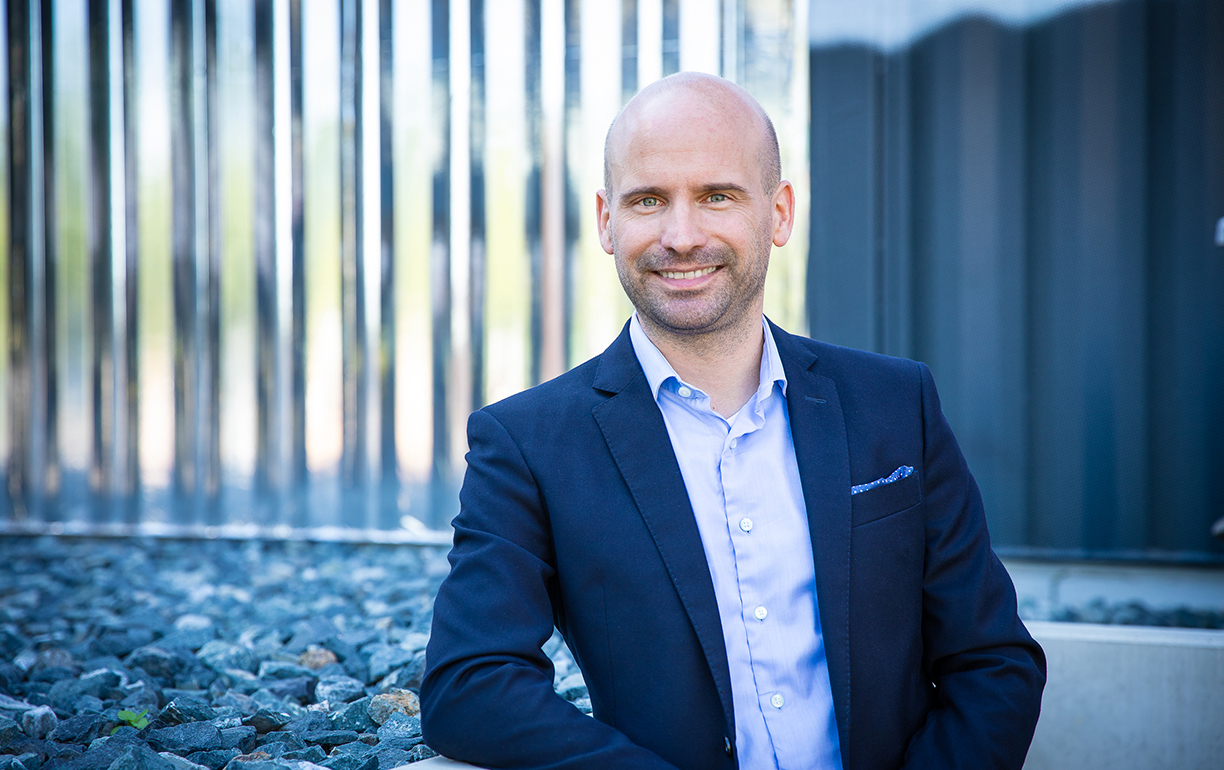
"We are very broadly positioned and, of course, particularly enjoy large logistics projects with producer’s goods. The more complicated the better. And that doesn't necessarily always have to be a large volume," says Carsten Schryver, Managing Partner of H.J. Schryver & Co. Schryver loves the challenge of logistics projects. His heart's project was the construction of a CO₂ -neutral thermo-solar power plant on the Galapagos Islands in the Pacific, which Schryver was able to support logistically.
The construction of the dam in Nuevo Léon is primarily about the time factor. Reloading the shipment is out of the question in view of the urgency. Added to this were other uncertainties such as the move from freighters from the capital's MEX airport to the NLU airport requested by the Mexican government. "We need planning capability and personal accessibility of contact persons in case of problems. |
This is given for us both here in Germany and in Mexico with Lufthansa Cargo. Due to the size of the shipments, only the transport by freighters is an option. With the direct freighter flight from Frankfurt to Mexico six times a week, both the capacities and the conditions are right," reports Schryver.
|
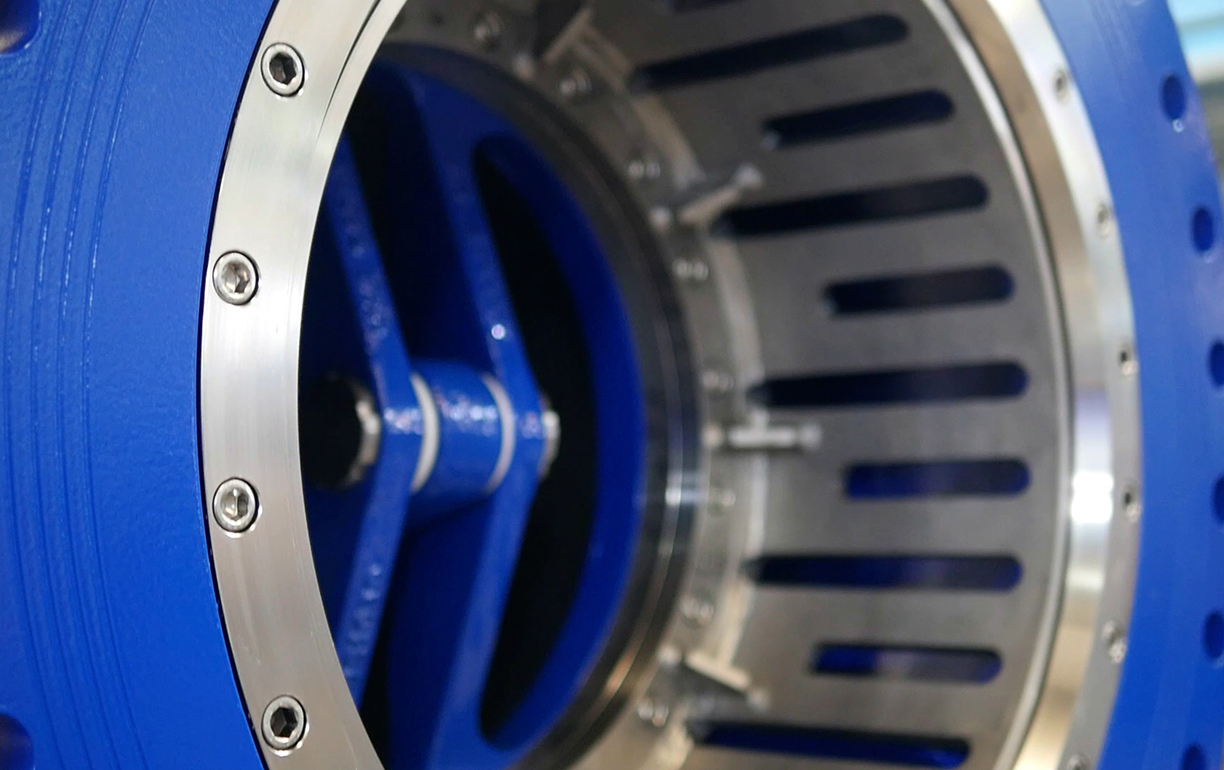
"In total, we have transported 175 tons in 14 shipments for the project so far. The largest shipment was 23 tons," says Gunnar Strauß, Key Account Manager for Schryver on the Lufthansa Cargo side. Even though the pumps are very large at 4.50 x 2.20 x 2.70m and the corresponding valves, the size is not a challenge for our freighters in this case.
However, the project coincided exactly with the changeover from Aeropuerto Internacional de la Ciudad de México (MEX) to the new Felipe Ángeles International Airport (NLU). The team in Mexico led by Frank Nozinsky, Head of Sales & Handling Mexico, Colombia, Ecuador, Central America and Caribbean at Lufthansa Cargo, has achieved an incredible accomplishment. In less than three months, they were able to open a new station at an airport that was basically not in operation at all, including opening a branch, introducing station and handling processes, starting ramp services, fueling and all the related organization and communication. |
On July 7, the last Lufthansa Cargo freighter flight landed in MEX, and on July 8, the first B777F of the cargo crane, with flight number LH8220, landed in NLU. On board both aircraft was equipment for the El Cuchillo II Dam pumps.
|
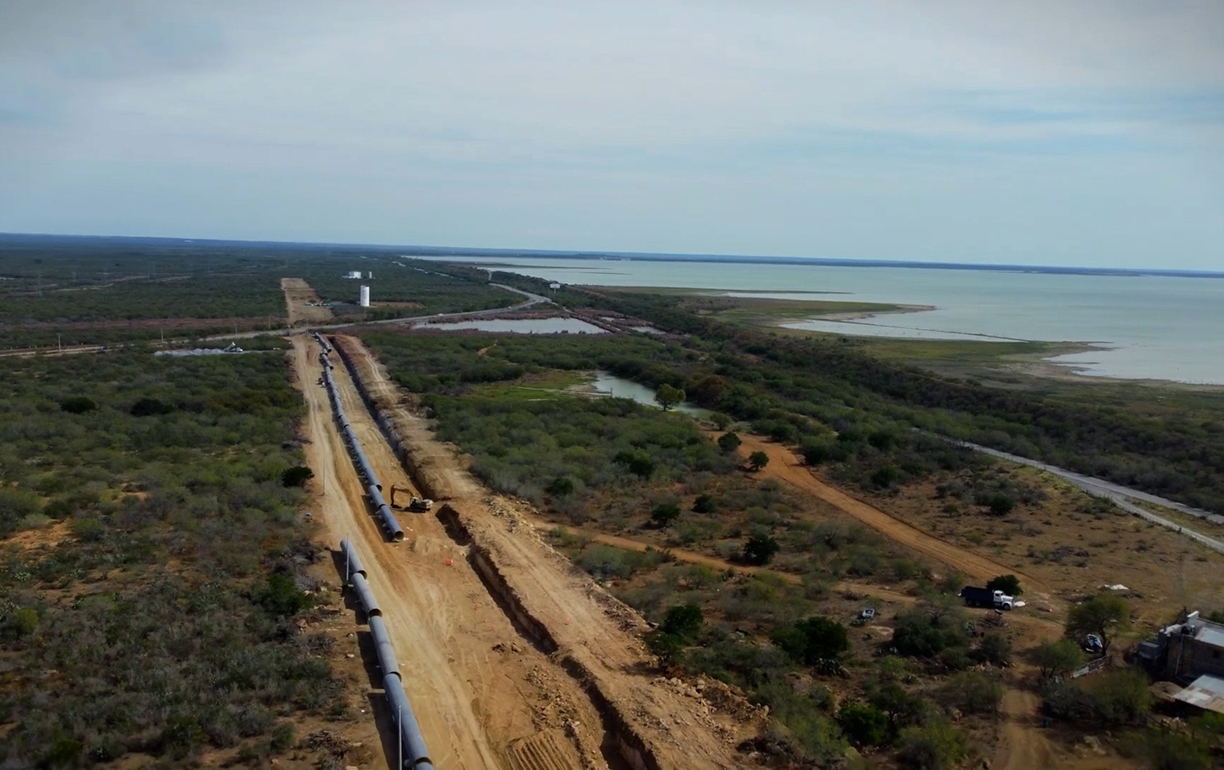
"This project is a particularly fine example of how to support local companies and yet promote global cooperation," sums up Frank Nozinsky, Head of Sales & Handling Mexico, Colombia, Ecuador, Central America and Caribbean at Lufthansa Cargo.
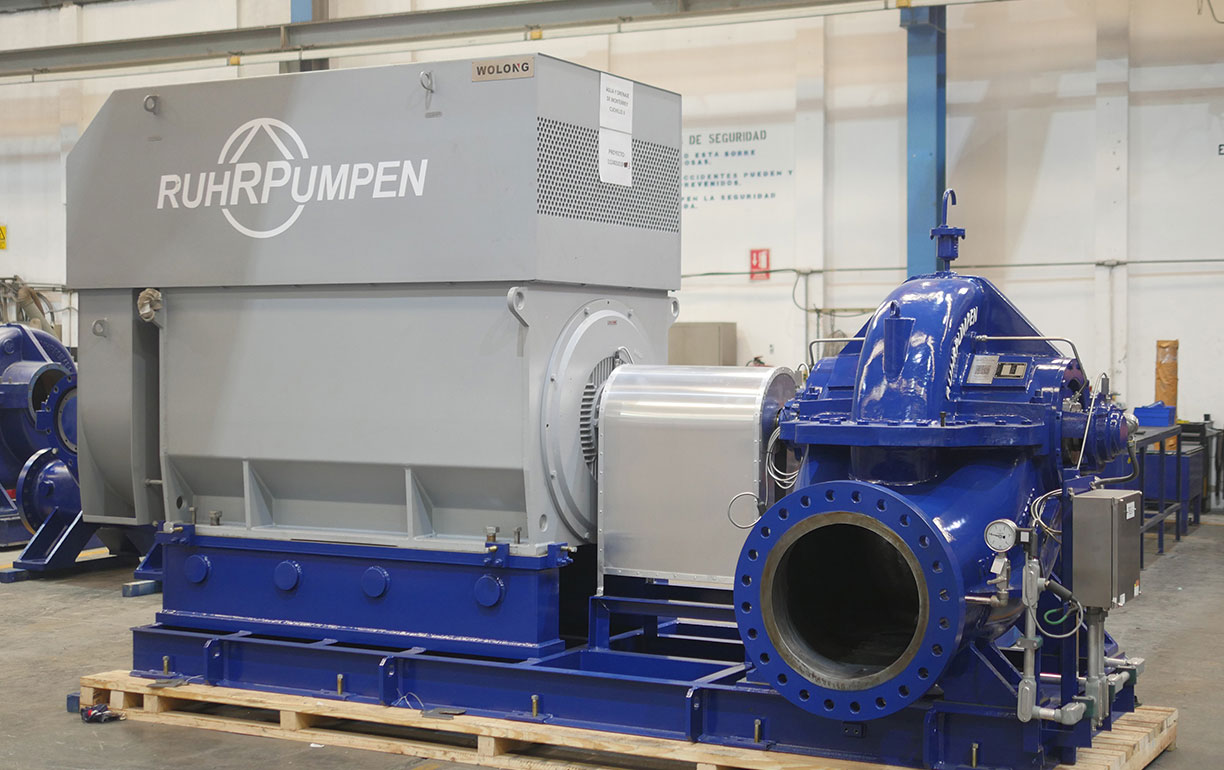
Arrived and installed in Mexico, the pumps deliver top performance. Many years of experience go into the design and manufacture of the pumps, which operate under continuous load. One of the "ZW Horizontal Split Case Pumps" can reach up to 9000 cubic meters per hour and a head of 340m with 14mt. A total of 30 pumps of this type are planned in the construction project.
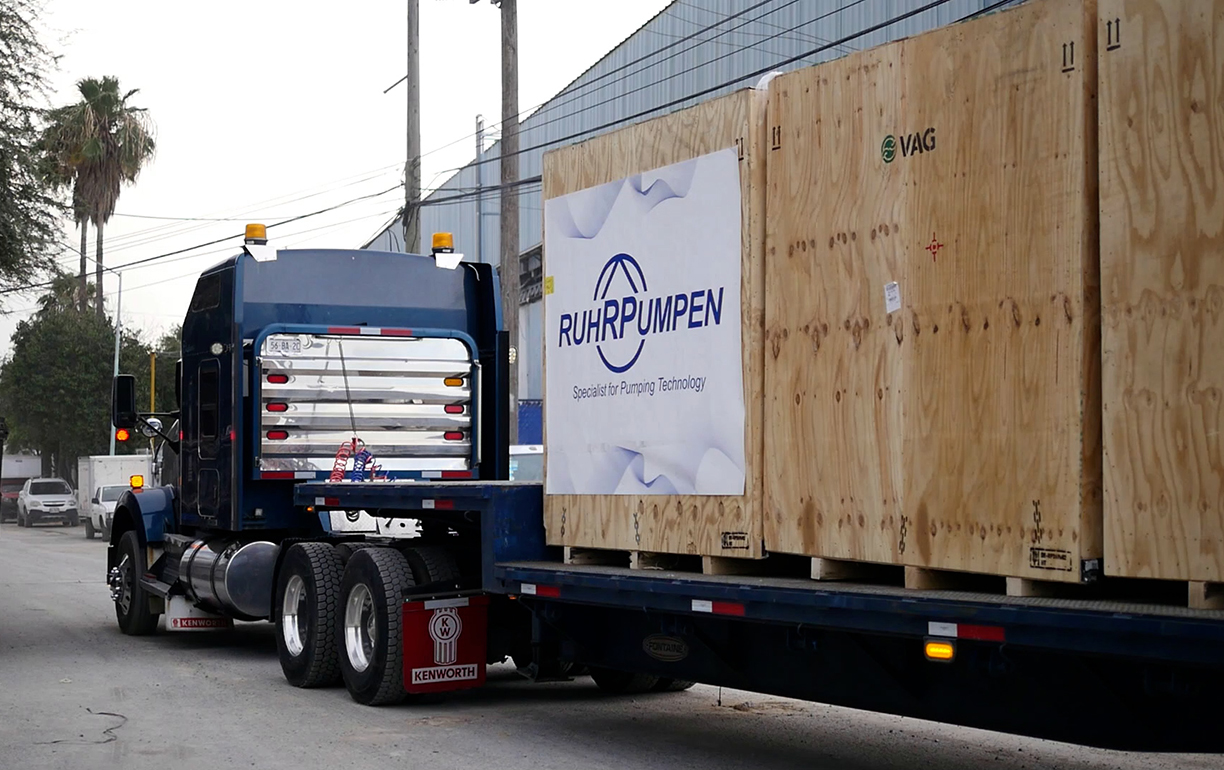
"We have already installed more than 60,000 pumping solutions in more than 90 countries and always give our best. Providing millions of families in our hometown with water in the long term until 2050 fills us with special pride this time!" tells family man Jose Luis Martinez Gonzalez. "And I can say that the logistics are a resounding success. The cooperation with Schryver and Lufthansa Cargo is an absolute win. Now, all of us can hardly wait for the first water to flow through the dam to the families in Monterrey."
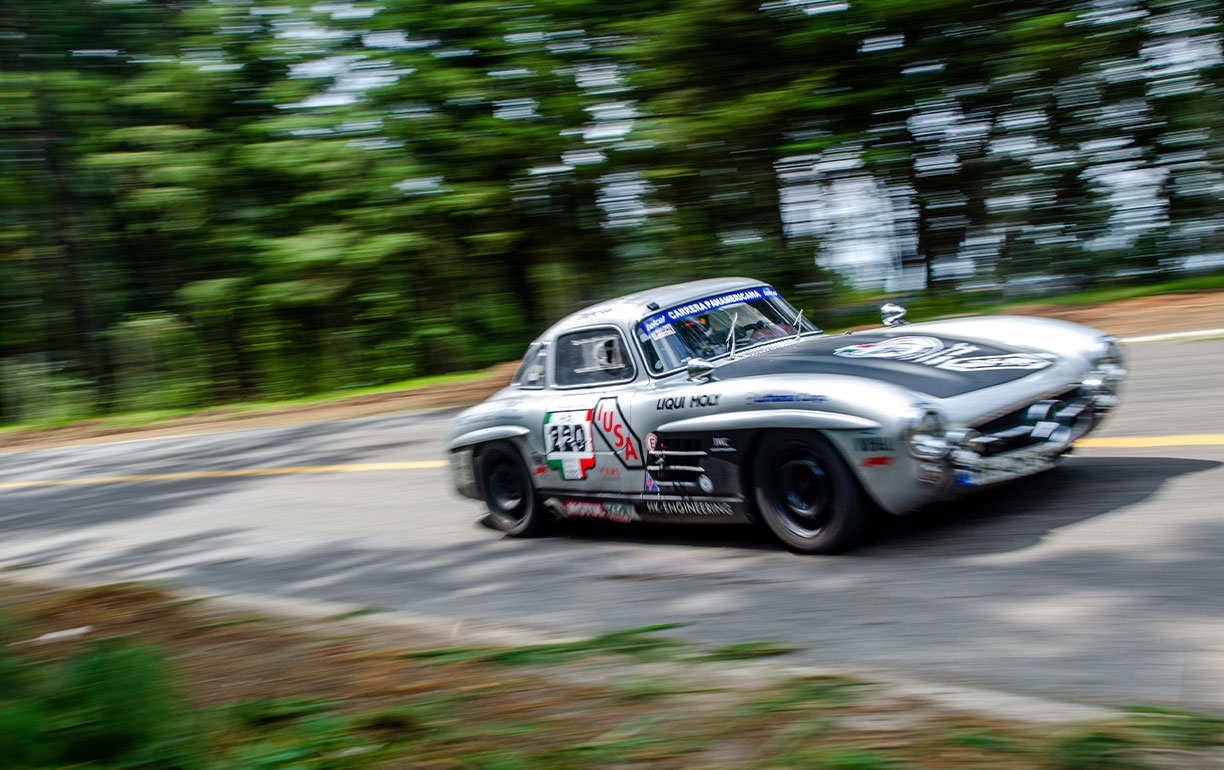
Time travel with Lufthansa Cargo: A gullwing flies into adventure
With the Mercedes 300 SL at the Carrera Panamericana 2022
A hand-painted poster, a silver racing car on a dust track, a huge cactus in the background. Just two words as a headline: "Triumphant double victory" and then two names: 1. Karl Kling, 2. Hermann Lang. That's all it takes for the birth of a legend: The Mercedes 300 SL and the road-going version derived from it will write automotive history - as the Mercedes "Gullwing." A story that begins on the racetrack of the Carrera Panamericana in 1952. And which 70 years later is still not over.
2022, Veracruz, Mexico. The almost unmuffled sound of classic racing engines roars in our ears. We see historic Porsches, a Ferrari, a Jaguar. But the crowd only has eyes for the silver car with the starting number 220: a Mercedes 300 SL Gullwing. The legend is back. 70 years after its great triumph, it is on the grid for the 35th edition of the race. This was made possible by a man who is standing next to the car, tired but smiling, getting ready for the start. He has run from pillar to post to find sponsors for his dream. He didn't know an hour ago whether his dream would come true or fall apart. And who was lucky enough to find a partner in Lufthansa Cargo who can make time travel possible and win races against time. It is the story of Kurt Richter, the dreamer, the doer and the racer. And of Lufthansa Cargo, which as a facilitator has shown what "just in time" can sometimes also mean ... |
Flashback. Kurt Richter, a Mexican hobby racer with German roots, has had a close relationship with Mercedes gullwing cars for years. He has already looked after the cars as a mechanic at previous editions of the Carrera Panamericana, knows their strengths, their (few) quirks, and of course their history, which is perhaps even more present in Mexico than in Germany. And in 2021, as a visitor to the Panamericana, which has since been revived, a plan matures in him: When the great success of 1952 is celebrated for the 70th time, there must actually be a gullwing on the starting line. To take the very track under its tires that finally put the Mercedes racing division back on the winning track after the Second World War ...
|
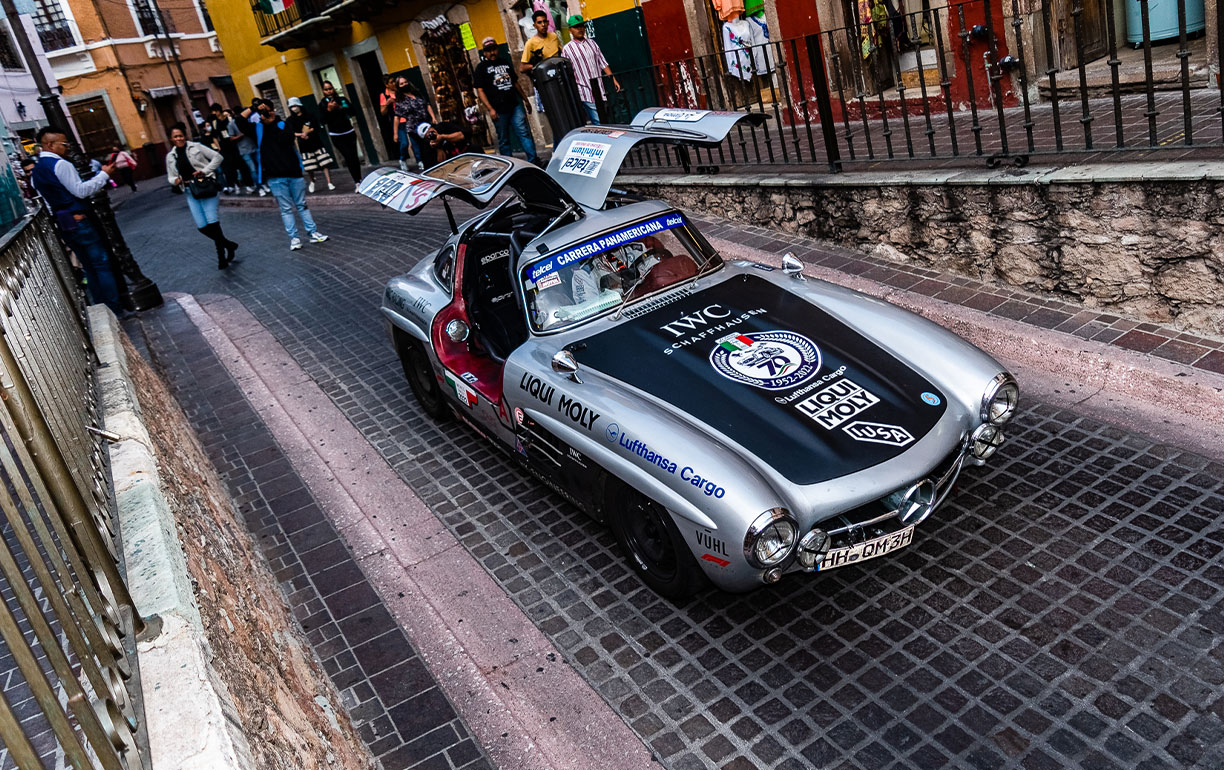
"I wanted to bring this car back to the people of Mexico - badly!"
Potholes, dusty roads. Heat. Mexico, November 1952. The first year in which Mercedes took part in racing again after the war was drawing to a close, and there had already been some successes with the new racing sports car, the 300 SL: Double victory at Le Mans, the three first places at the Eifel race at the Nürburgring. But those had been real racetracks, courses you knew or at least could quickly memorize. But this is something completely different: thousands of kilometers on public roads, poor surface, plus enormous differences in altitude and temperature. Whoever starts here for the first time is an outsider. Come here to learn. For this reason alone, the Germans have the sympathy of the Mexicans. And also because the Alemanos have a few strange idiosyncrasies: They drive the day's routes beforehand and write down each passage, each curve, each eye of a needle neatly in a book. The competition laughs at them.
But what no one knows at the time is that this Panamericana is probably also the birth of the so-called "prayer book" - from which the co-driver tells the driver exactly what is coming next. "300 meters, 60 degrees left, 50, second gear, then straight, fourth gear, 180, ..." Today, every rally is driven like this. In 1952, this idea saved the Mercedes team valuable time and was one of the very important cornerstones of victory ... Kurt Richter's prayer book initially contains something quite different - namely, an enormous sum of money that is needed to actually get the car started. Richter quickly overcomes the other hurdle, namely finding a 300 SL approved for racing: He has close ties to HK Engineering in Polling, Bavaria, and thus has access to a 300 SL that has been successfully competing in historic races for 15 years. But racing is an expensive business, even more so on the other side of the world - and even more so when the market value of the vehicle is a conservative estimate of 1.5 million. And so Kurt Richter embarks on a stage race of a very different kind, one that is less about speed and more about patience: the search for sponsors. |
And all those who come into question wave them off. Put off. They don't want to get involved until it's clear that the car will actually find its way to Mexico. "First bring a gullwing here, then we'll see." Meanwhile, the clock is ticking, time is passing. The year 2022 is dawning. It will be spring. It will be summer. Kurt Richter is simply not making any progress. And then he writes an e-mail. The content: The history of the race. The anniversary. The idea. And the info that the car is not the problem. The recipient: Frank Nozinsky. Director of Lufthansa Cargo for the Central American region. Headquarters: Mexico City. It is now August 25, a Thursday. Richter knows that Cargo is fast. But he is surprised just how fast: On Monday, he receives the answer: "Time for a team call? I'll invite the head office right away." "I saw Kurt's request and immediately thought, if this isn't Enabling Global Business - what is?"
|
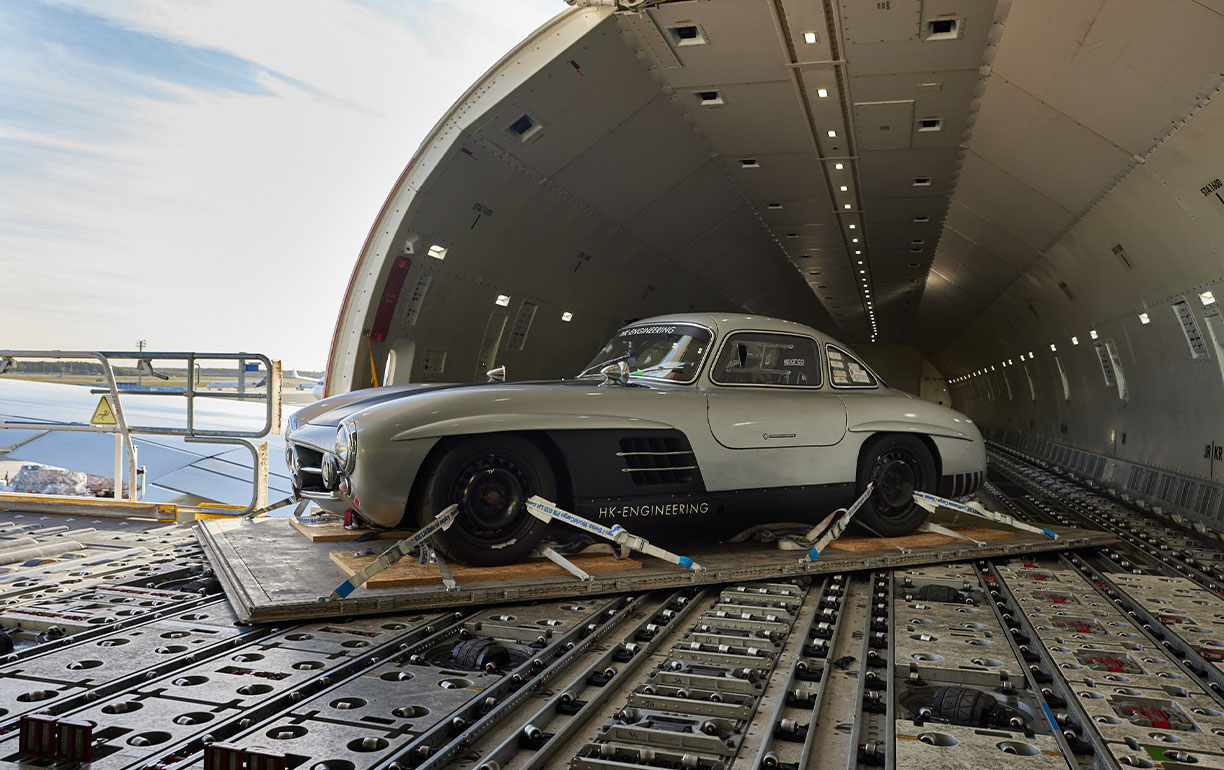
It's not just the quick response that gives Kurt Richter new hope - he also knows that, with Lufthansa Cargo, he's relying on real professionals when it comes to car transport. Hardly anyone transports as many valuable cars or important spare parts through the air as Lufthansa Cargo. And hardly anyone has as much experience with automotive rarities, has such well-trained personnel on site and has established special and particularly prudent processes for goods of this kind - Valuable Goods. The first call takes place the same week. The message to Kurt Richter is as clear as it is encouraging: "We'll help you. We'll take care of the transport.
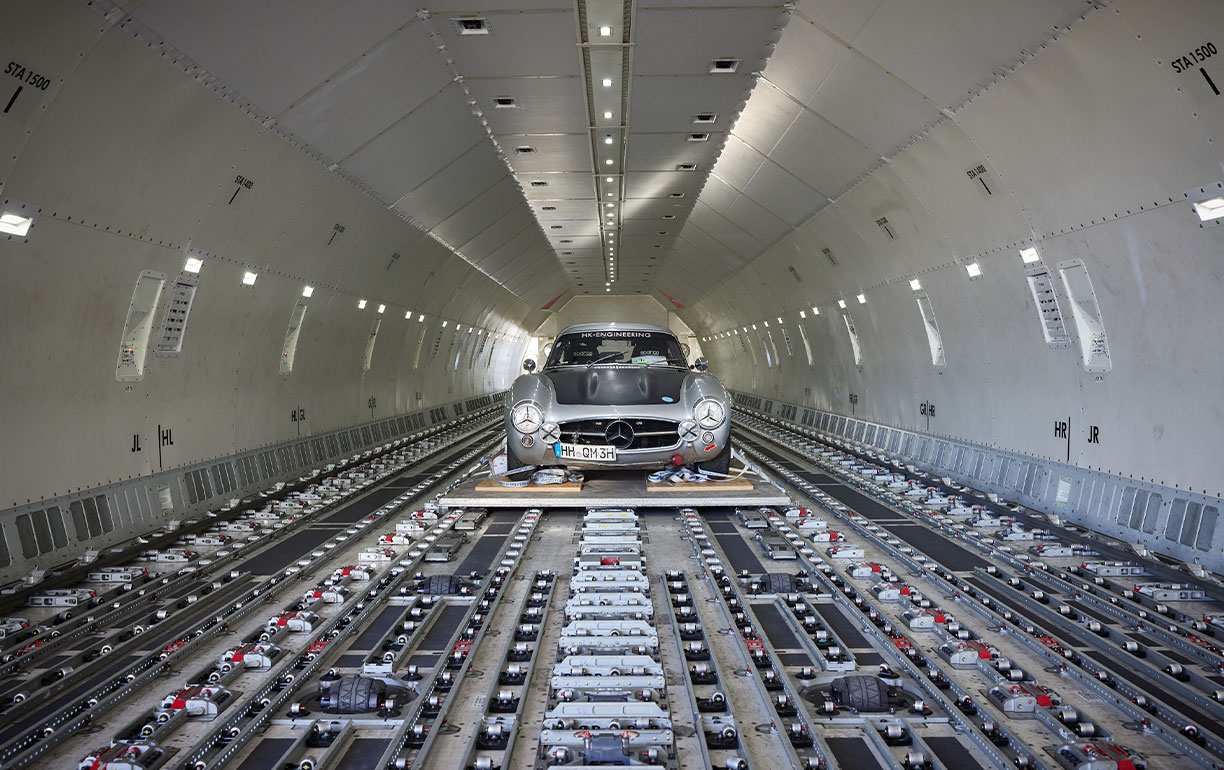
The ice is broken. Now suddenly others want to join in, too. They accept. Promise financial support. But until Richter receives the money, more valuable time passes. The Carrera Panamericana starts on October 14. And it is not until September 23 that Kurt Richter actually has the money from all the sponsors at his disposal. Gives the go to HK Engineering: Get the car ready. The race before the race begins. Because the car has to be raised. Needs a different brake system. Because in Mexico there are still different road conditions than on European race tracks ...
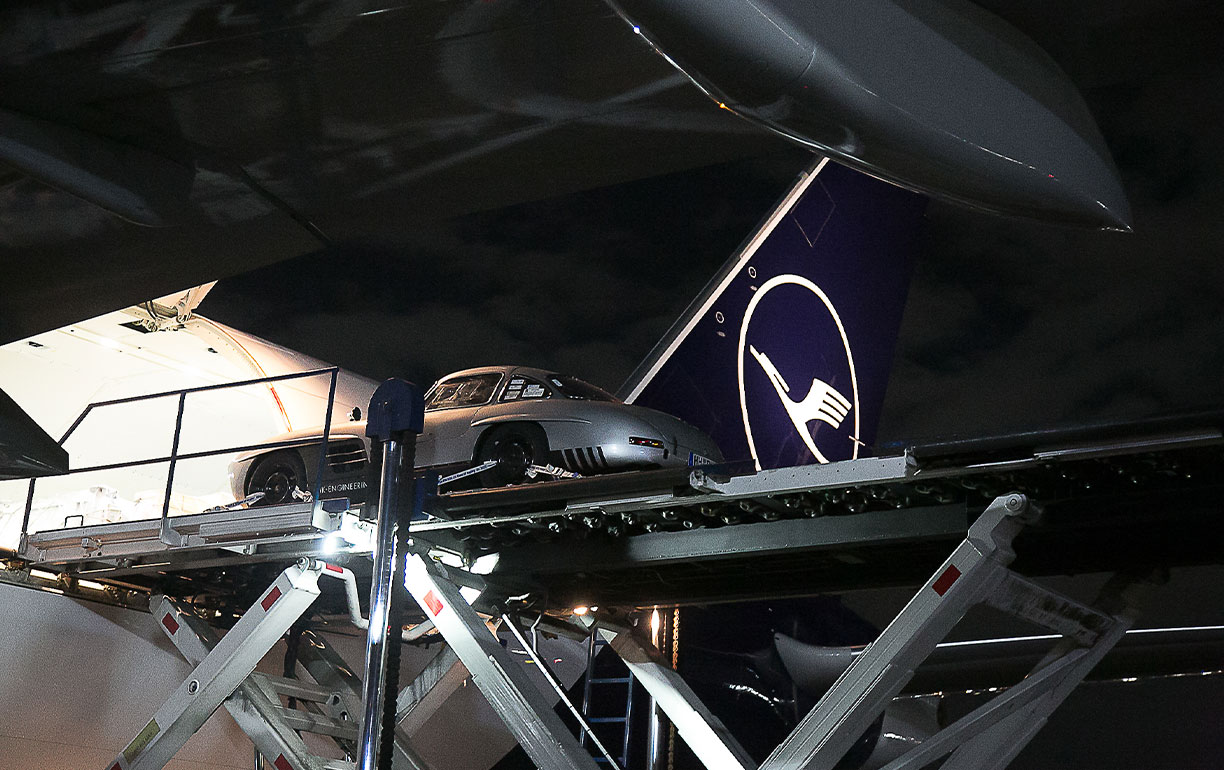
Somewhere between Tuxtla and Oaxaca in southern Mexico. The first day of racing. The silver-colored lightweight races along the narrow track at almost 200 kilometers per hour. The man at the wheel listens to the announcements from the prayer book. With a steering wheel that is huge by today's standards, he steers the car around the bends with millimeter precision. Reacts precisely to every swerve, every bump. But then he doesn't stand a chance: a huge vulture crashes into the windshield with full force. Glass shatters. The driver struggles to keep the car on the track. He looks to the side. His passenger is covered in blood. Unconscious. It takes what feels like an eternity before he regains consciousness - and insists on continuing the journey immediately. It all happened on the morning of November 19, 1952, and it was the stuff of legend. On this first day, despite the accident, it was still enough for third place. And six days later, on November 25, the damaged Mercedes 300 SL reaches the finish line of the race. As the winner. Karl Kling at the wheel and Hans Klenk as co-driver lay the foundation for further racing successes for the Silver Arrows from Stuttgart. And show that the will to win is sometimes the most important thing ...
Time jump. September 2022 in Polling. The schedule until the launch in Veracruz is tight, but feasible. The car is scheduled to take off in Frankfurt on October 4. No problem - if the injection system didn't suddenly start acting up. Anyone who has ever had to wait for a spare part in a modern car knows what that means. But with a historic racer? Although HK Engineering does nothing but service Mercedes 300 SLs, the repair turns out to be difficult. And time-consuming. Until, at some point, it becomes clear to everyone involved that it's not going to work. The car can't take off on the 4th. Off? Over? All for nothing? |
One milestone has already been reached: the Mercedes 300 SL Gullwing is on Mexican soil. But there is neither time nor reason to breathe a sigh of relief. The car still has to be cleared through customs. And it is precisely at this point that there are suddenly new problems, everything seems to have conspired against Kurt Richter: The car is stuck in customs. The clock keeps ticking. Relentlessly. Unstoppable. It is October 13, 11 p.m., when customs finally releases the car. Now the gullwing has to be taken to Veracruz. Only now? No, because that's another 400 kilometers - by truck. And in Veracruz? Technical inspection. Testing for race fitness. The start would then be at 7:30 in the morning. In theory. Because in practice, that's actually no longer possible.
|
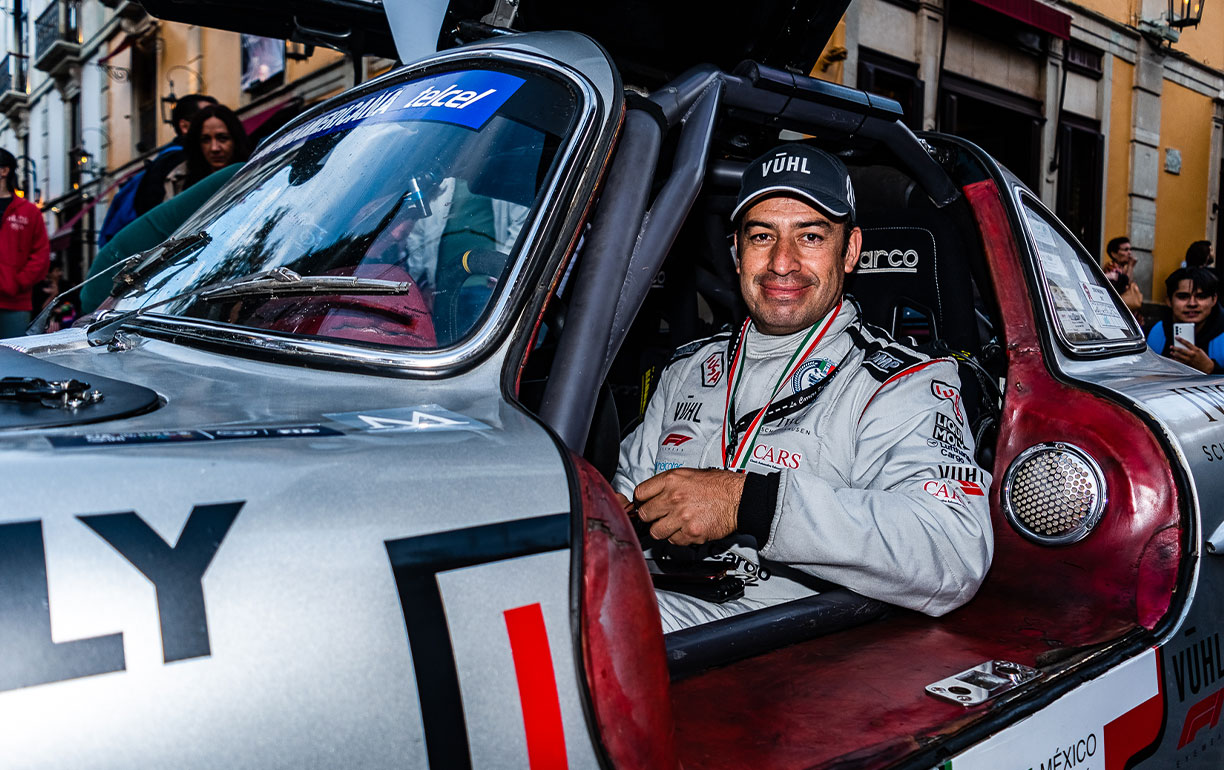
Via the México 150, we drive east in a wild chase. Fortunately, there is not much traffic at this hour. Kurt Richter tries to sleep, but it's no use. Too many thoughts run through his head, and above all the anxious question: Will it be enough? Will they make it in time against all odds? Or was it really all in vain? What if they get stuck in a traffic jam somewhere? What if there's no way through because of the race in Veracruz? What if the race commissioners don't play ball?
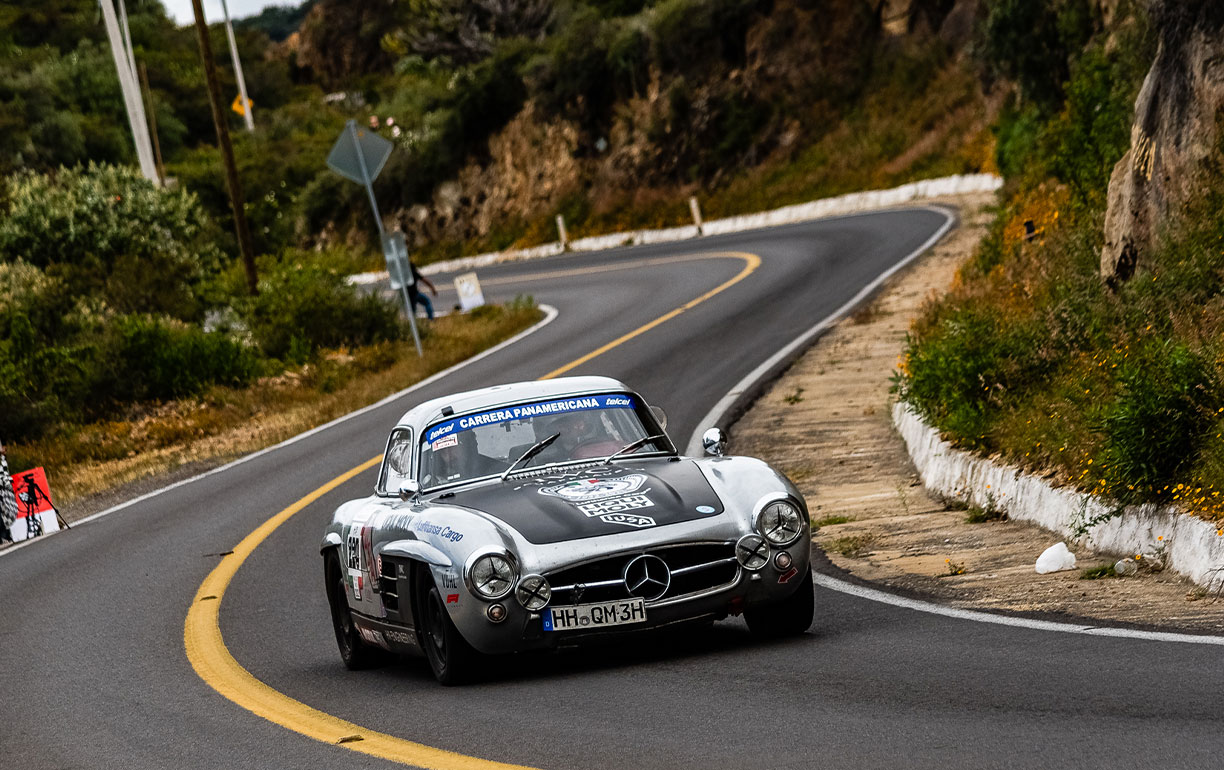
But now Richter has the luck of the fittest: They get through well and reach the starting location at 6:30 a.m. - an hour before the race is supposed to start. And it turns out that someone else has been waiting eagerly for the 300 SL Gullwing: the race organizers. For them, the legend's comeback on its 70th anniversary is also a real matter of the heart. In no time at all, the car is checked and given the go-ahead to start.
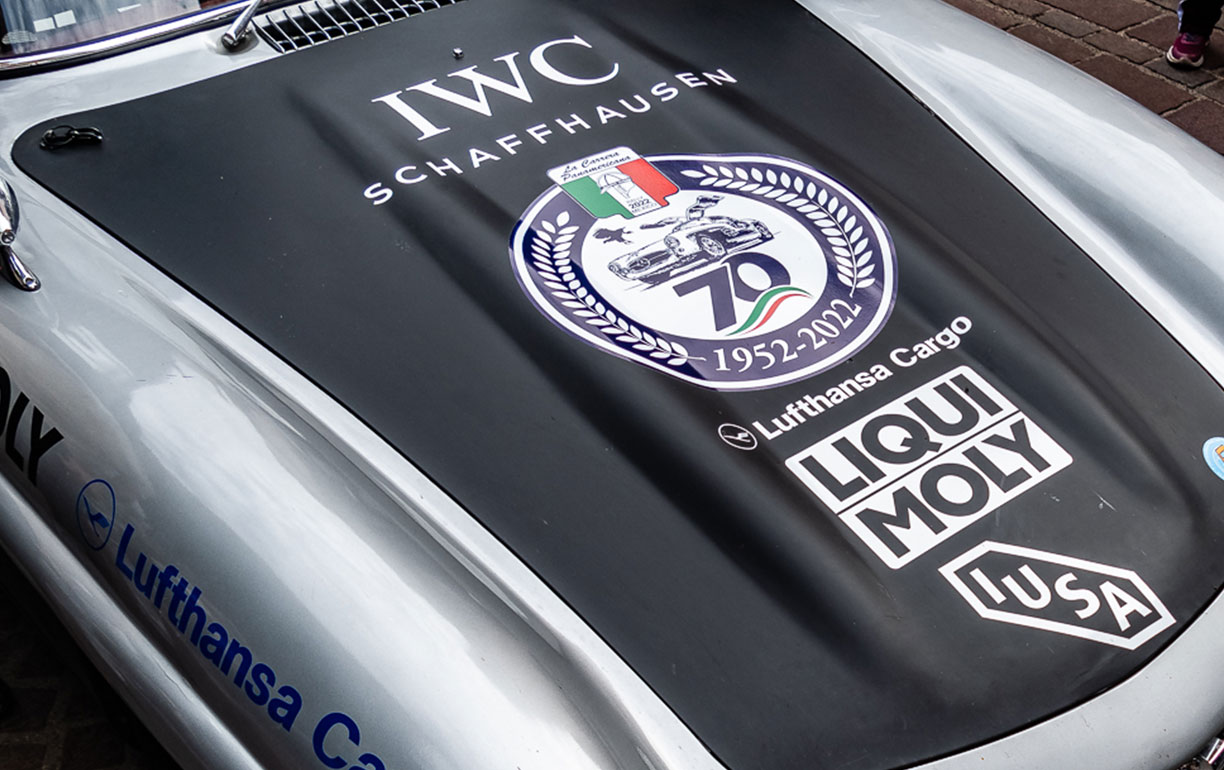
Veracruz, October 14, 2022, 7:29 am. At walking pace, a silver Mercedes 300 SL Gullwing rolls up to the starting line of the 35th Carrera Panamericana. 70 years after the legendary double victory. Tens of thousands of enthusiastic visitors point their cameras at the car. Kurt Richter keeps the engine revving with a light tap of the gas pedal. The hoarse rumble of the six-cylinder engine barely muffles his ears through the sliding side windows. On the passenger seat, Ricardo Galindo has the prayer book on his knees. A hand pushes in front of the windshield from the left, counting down the last seconds. Four. Three. Two. One. Go. The hand jumps to 7:30. The engine howls. The 300 SL shoots off as if unleashed. The legend is back.
"People saw the gullwing - and they had tears in their eyes."
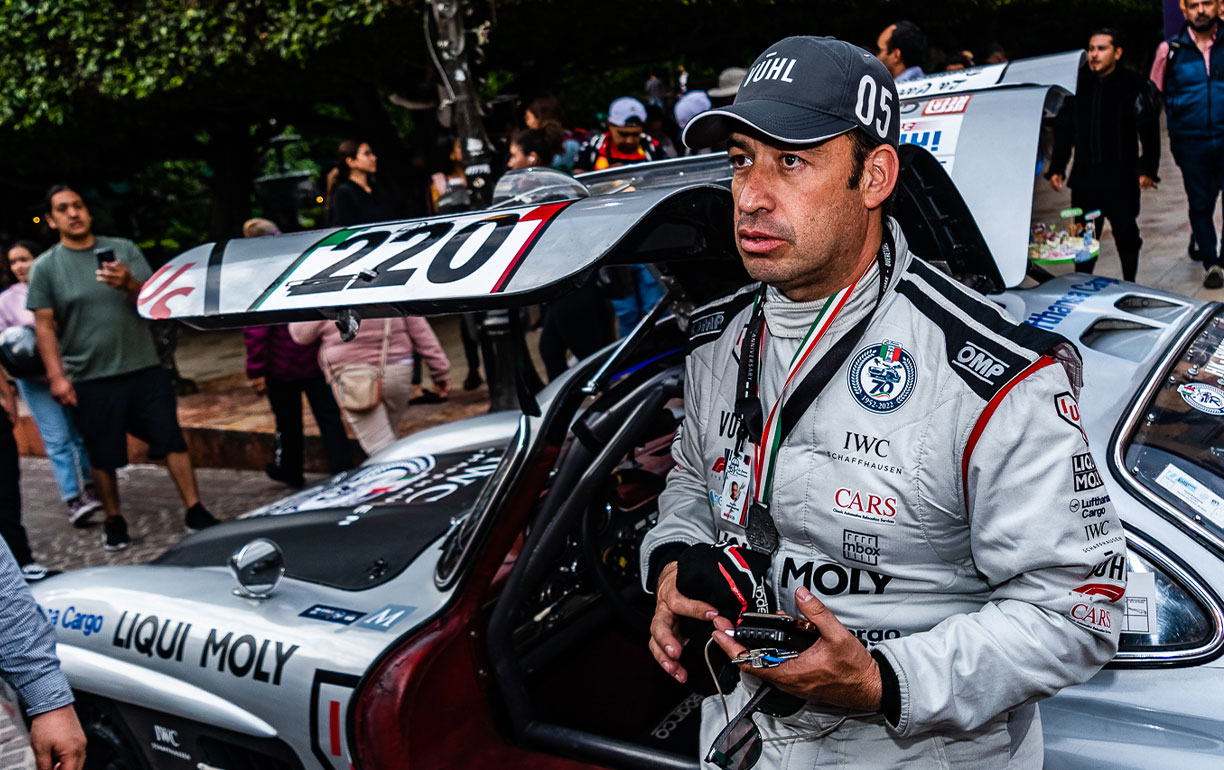
The man
Kurt Richter, born 1977
Born in Mexico; the family emigrated to Mexico after the First World War. His father was an importer of BMW and Porsche in Mexico and passed the car virus on to his son. Originally a trained car mechanic, Kurt Richter now works as an event consultant and motorsport promoter. He regularly competes in races and rallies, preferably with historic vehicles. By taking part in the Carrera Panamericana in a 300 SL Gullwing, Richter has fulfilled a lifelong dream. He finished the 35th edition of the race to mark the 70th anniversary of the historic double success of 1952 in third place in his racing class.
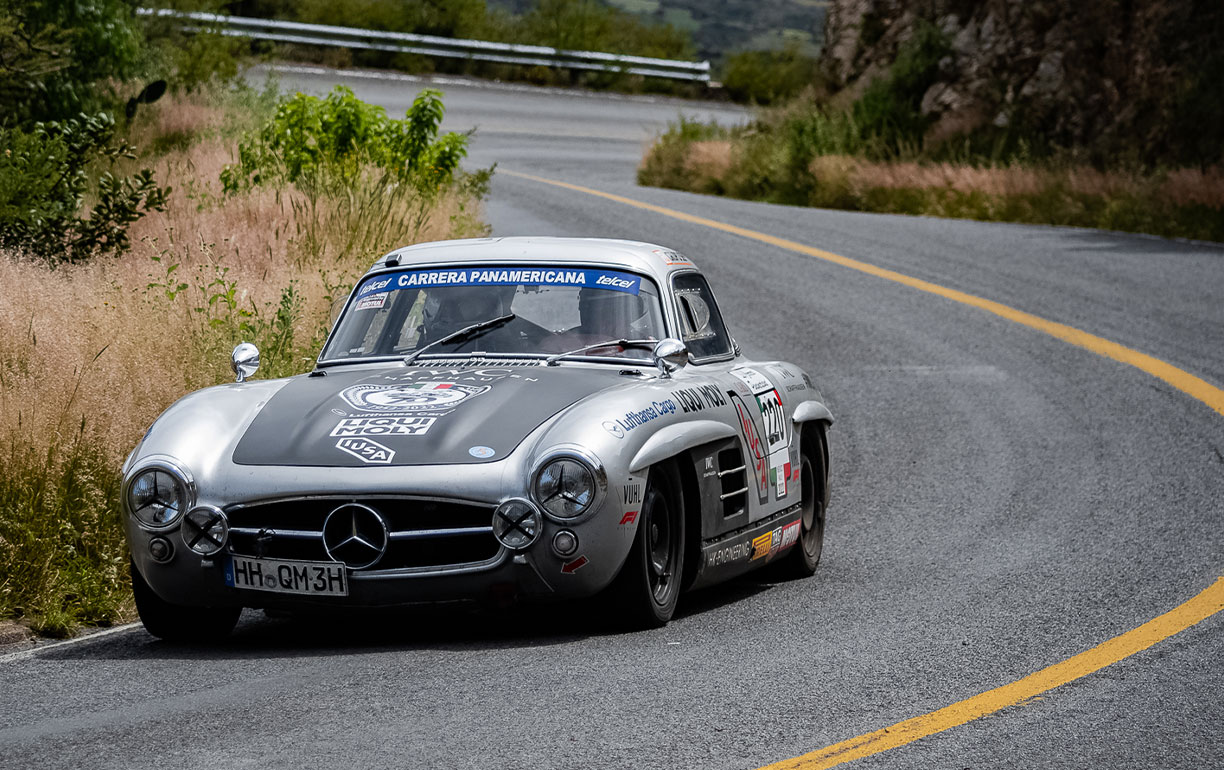
The machine
Mercedes 300 SL (W198) Coupé (Gullwing); road version, converted to racing car.
In-line six-cylinder, 3 L displacement, 245 hp
Weight (in racing trim) 1,300 kilos
Owner: Hans Kleissl (HK Engineering)
The vehicle looks back on a long and successful racing career and is a regular guest at the Festival of Speed in Goodwood, among other events. In the past, it has been driven by several former Formula 1 drivers, including David Coulthard and Jochen Mass. HK Engineering is the only company in the world that specializes exclusively in the maintenance, care and repair of Mercedes 300 SL.
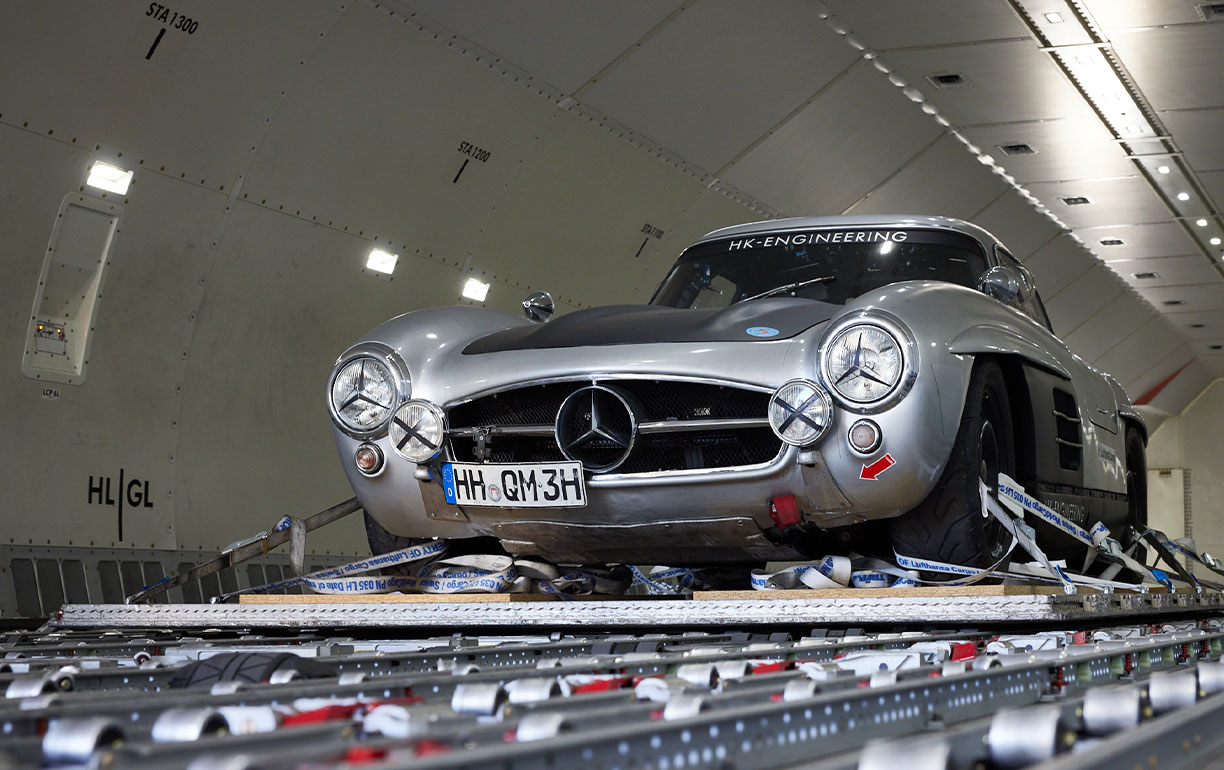
The logistics
Lufthansa Cargo td.flash from Frankfurt to Mexico City
Three logistical challenges come together in this project - deadline pressure, the fact that cars are Dangerous Goods, and the high value, which also makes the gullwing a "Valuable Good". In practice, this means that td.flash is the product of choice, and for everything else it means paying special attention to the last detail. In terms of safety, special attention is paid to the lubricants and operating fluids, the battery and also the tire pressure. Outside the aircraft, cars are always kept in protected areas so that damage from normal storage operations can be ruled out.
In addition, classic cars are always accompanied by a supervisor. On the pallet itself, the same applies as on the race track: The perfect balance between ground adhesion and dynamics is the trump card, so that on the one hand the car does not become self-sufficient in case of air holes, but on the other hand the strong forces during the flight do not cause any damage to the vehicle structure. |
And as in many other professional areas, it is evident that nothing is more valuable than years of experience mixed with passion for one hundred percent performance.
|
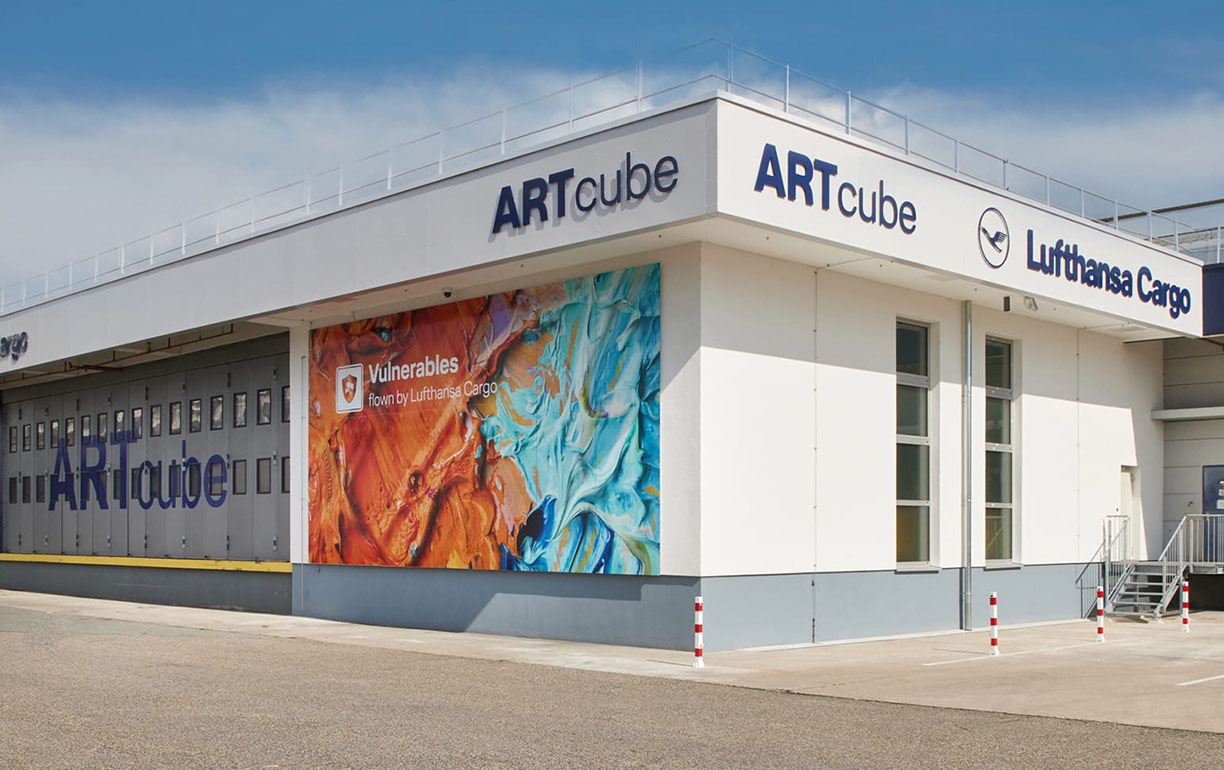
Always state of the art - our ARTcube Frankfurt
In June, 2022 we opened our new Fine Arts warehouse facility at the Frankfurt Hub. With 155 square meters, the ARTcube in the Lufthansa Cargo Center now offers our customers twice as much space for safe and professional storage of high-value Fine Arts of all kinds.
"The modern ARTcube combines optimal handling processes with the highest security features. This allows us to meet the special requirements of sensitive art objects and offer customized solutions for the storage of Fine Arts in our Hub," explains Thomas Rohrmeier, Head of Handling Frankfurt. "With the new building, we have further sharpened our qualitative focus on this special product and thus curators and art collectors experience the best storage conditions for their Fine Arts shipments with us."
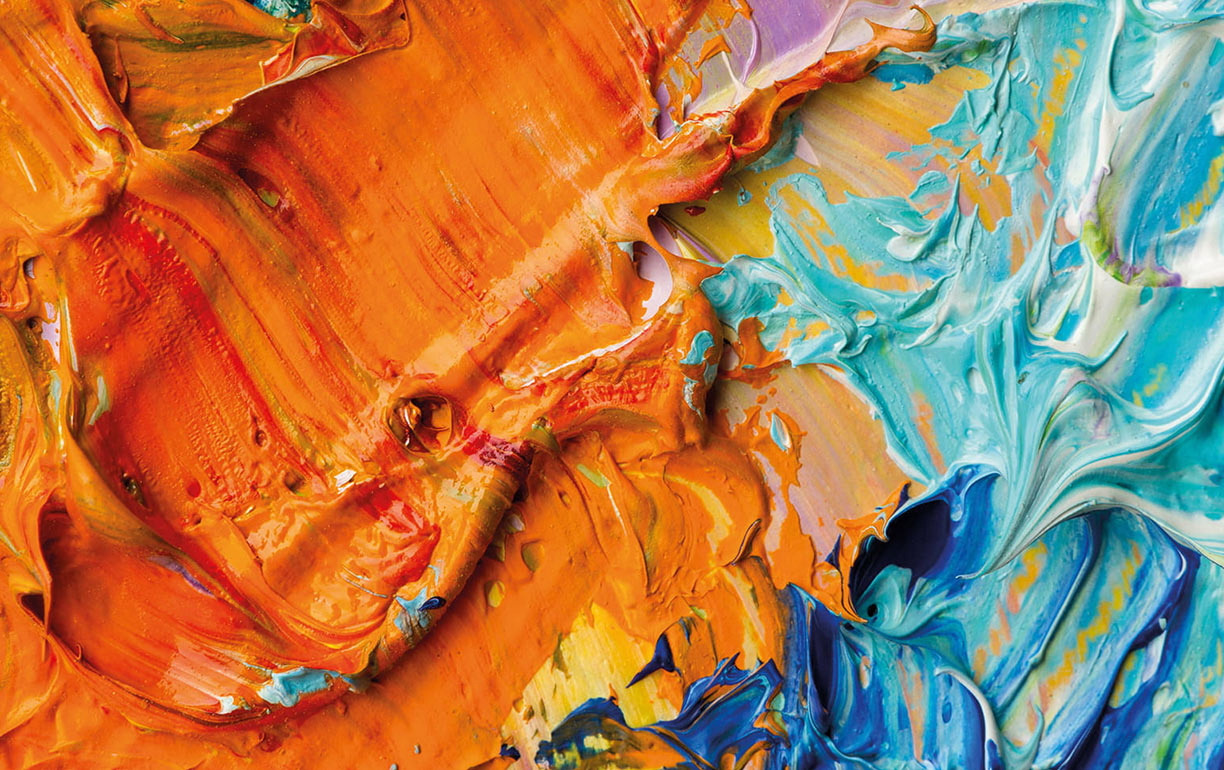
Fine Arts shipments will in future benefit from a special warehouse with modern technical equipment, in which a ventilation system with heating and cooling functions enables targeted temperature control. Vertical window strips on the facade allow natural lighting, which is optimized by a supporting lighting system. Specially trained handling personnel guarantee optimally coordinated processes. Access to the special warehouse is controlled and monitored by sensitive security technology. As an Add-on Service, it is possible to book an individual attendant for Fine Arts shipments, especially on the ground.
Lufthansa Cargo regularly flies high-value and famous Fine Arts by important artists to renowned exhibitions around the world. With its "Vulnerables" product range, the airline has therefore tailored a special transport solution to the needs of this particular industry, thus guaranteeing security, professional handling and seamless monitoring for Fine Arts logistics.
The new construction of this special warehouse is part of the modularly planned infrastructure program "LCCevolution" at the Frankfurt home Hub, the core of which includes, among other things, the new construction of the central high-rack storage system in the Lufthansa Cargo Center and a gradual core refurbishment of the logistics infrastructure. The complete modernization of the Lufthansa Cargo Center is scheduled for completion in 2029.
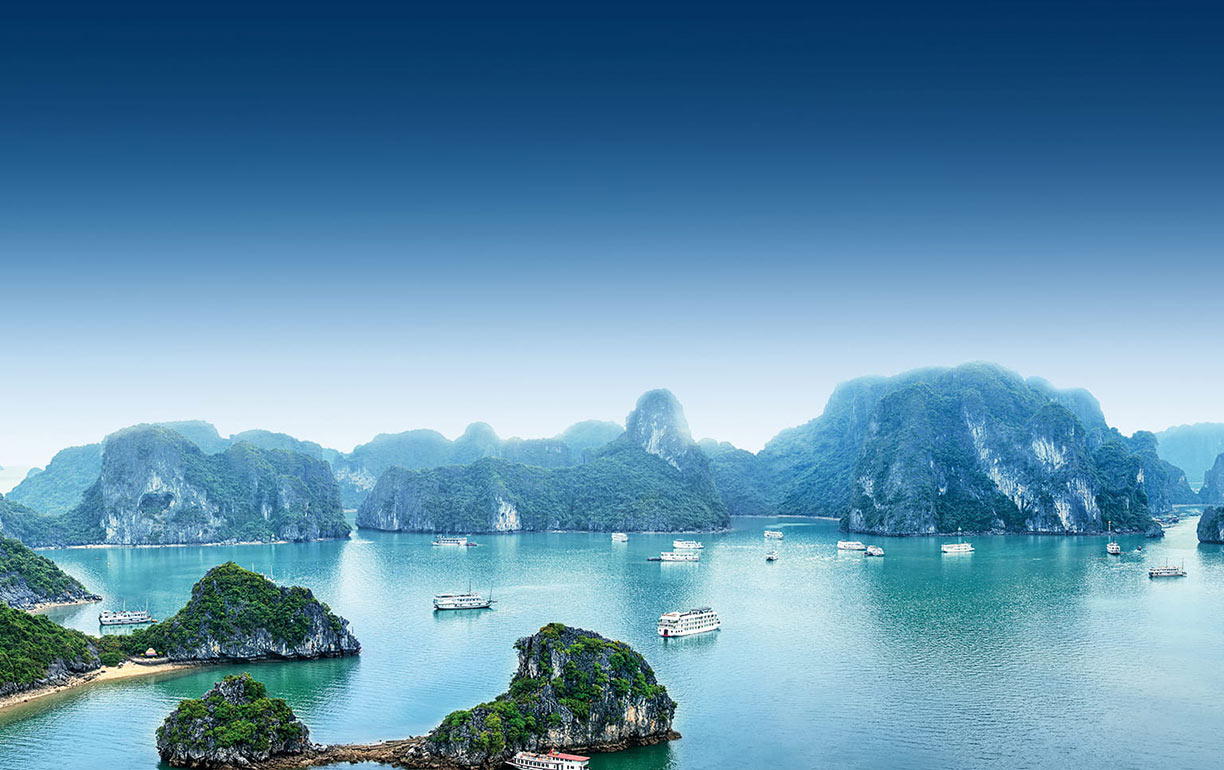
Viet Nam - small country with big future
Vietnam not only has a lot to offer in terms of scenery. The Southeast Asian country is an emerging market with enormous potential. As a booming manufacturing hub, Vietnam showed its resilience and growth strength during the pandemic. Particularly in the manufacturing sector, Vietnam is becoming increasingly important globally and has seen the highest growth in this sector in recent years. Foreign investment has almost doubled in the last decade. The most important ones come from Asia and Europe.
The share of Vietnam's GDP in the world GDP has doubled within the last ten years (from : 0.2% in 2011 to 0.4% in 2021). In this context, foreign trade is one of the most important economic drivers. Of Vietnam's total exports, 29% go to the US and 12% to the EU. The most important export goods are electronics and textiles/fashion - goods for which air freight plays a major role. Sustained economic development is expected to promise significant air freight growth in the coming years, further increasing demand for air freight. The boom in e-commerce is also contributing to an increase in demand in Vietnam.
We at Lufthansa Cargo, we are well prepared to expand the supply of air cargo capacity in the Vietnamese market and to Asia.
On Asian routes alone, there are 38 weekly connections to attractive destinations to choose from. NEW to the schedule is the destination Hanoi (HAN). The capital will be served twice a week from Frankfurt from the beginning of November - with an eastbound stopover in Mumbai/India. We already flies twice weekly from Frankfurt via Bangkok (BKK) to Ho Chi Minh City (SGN), thus doubling our presence in Vietnam.