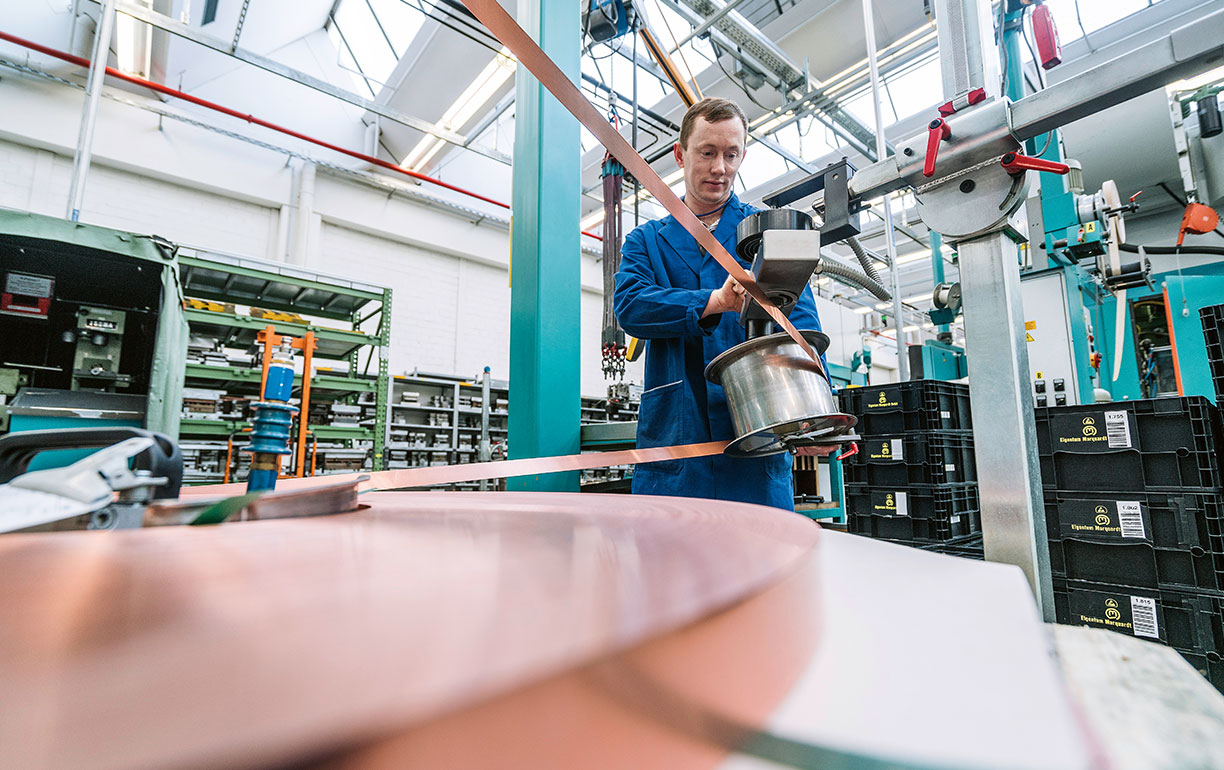
Smart parts, big goals.
Bei kleinen Teilen ist Marquardt weltweit eine Größe. Dank Bedienelementen und Schaltern für Autos stehen die Zeichen mehr denn je auf Wachstum. Die Logistik der Württemberger wäre ohne Luftfracht undenkbar.
Unsichtbare Helfer. In einer oberlichtdurchfluteten Halle erwacht der Begriff zum Leben. Dort werden an einem guten Dutzend Maschinen filigrane Muster in Stahlbänder gestanzt, die selbst nur ein paar Zentimeter breit sind. Eines der Bänder besteht aus einer glänzenden Chrom-Nickel-Legierung und läuft stetig von einer Spule. „Daraus werden Batteriekontakte für das Innere von Autoschlüsseln“, erklärt Andreas Weidner.
”Der 45-Jährige ist verantwortlich für das weltweite Transport- und Zollmanagement der Marquardt-Gruppe – die mit jeder Menge Ingenieursgeist viele dieser unsichtbaren Helfer entwickelt und herstellt. Für Elektrowerkzeuge, Haushaltsgeräte und neuerdings Elektrofahrräder, vor allem aber für Autos: Bedienfelder in der Mittelkonsole, Tasten am Lenkrad und zum Sitzverstellen. Ob Fensterheber oder Keyless-Systeme zum Öffnen und Starten – überall steckt Technik von Marquardt drin. Und das bei zahlreichen Herstellern. „Wir produzieren für die Original Equipment Manufacturer (OEM), aber auch für andere Zulieferer, die die Teile dann verbauen.“ |
Marquardt ist einer der weltweit führenden Entwickler und Hersteller von elektromechanischen und elektronischen Schaltern und Schaltsystemen. Weidner führt das „planet“-Team durchs Stammwerk in Rietheim-Weilheim auf der Schwäbischen Alb im Südwesten Deutschlands. 2.500 Mitarbeiter sind hier beschäftigt, etwa genauso viele Einwohner zählt auch der Ort.
|

Auftrieb dank Automotive.
Rund 300 Marquardt-Mitarbeiter sind in der Kunststofffertigung beschäftigt: Marquardt produziert nicht nur das Innenleben, sondern auch viele Bedienelemente selbst. Spritzgussmaschinen spucken ohne Unterlass kleine Teile aus: weiße Kippschalter oder mattschwarze Elemente, die man sofort als obere Hälften von Zündschlüssel-Gehäusen erkennt – nicht zuletzt am geprägten Logo eines großen deutschen Automobilbauers.
Ende der Neunziger stieg das Familienunternehmen groß ins Automobilgeschäft ein – und bald ging es mit ebenso großen Schritten vorwärts. 2015 betrug der Umsatz rund eine Milliarde Euro. „Der Automotive-Anteil lag bei weit über 80 Prozent“, so Weidner. Heute beschäftigt die Gruppe an 14 Standorten und in zusätzlichen Vertriebsbüros mehr als 8.500 Mitarbeiter. Produziert wird unter anderem in China, Mexiko, USA, Rumänien und Mazedonien. |
Der Frachtkranich zählt zu den häufig genutzten Carriern. „Natürlich freuen wir uns, wenn unsere Sendungen mit Lufthansa Cargo fliegen, denn das steht für Qualität und Verlässlichkeit“, so Weidner. Meist geht es um Standardfracht, regelmäßig wird aber auch das Expressprodukt td.Flash gebucht. Gefahrguttransporte sind ebenfalls keine Seltenheit. „Denken Sie an unsere ausgestanzten Kontakte: Enthält ein Autoschlüssel eine Batterie, ist er Gefahrgut. Und das Thema Transportsicherheit wird bei Lufthansa Cargo wirklich ernst genommen!“
|
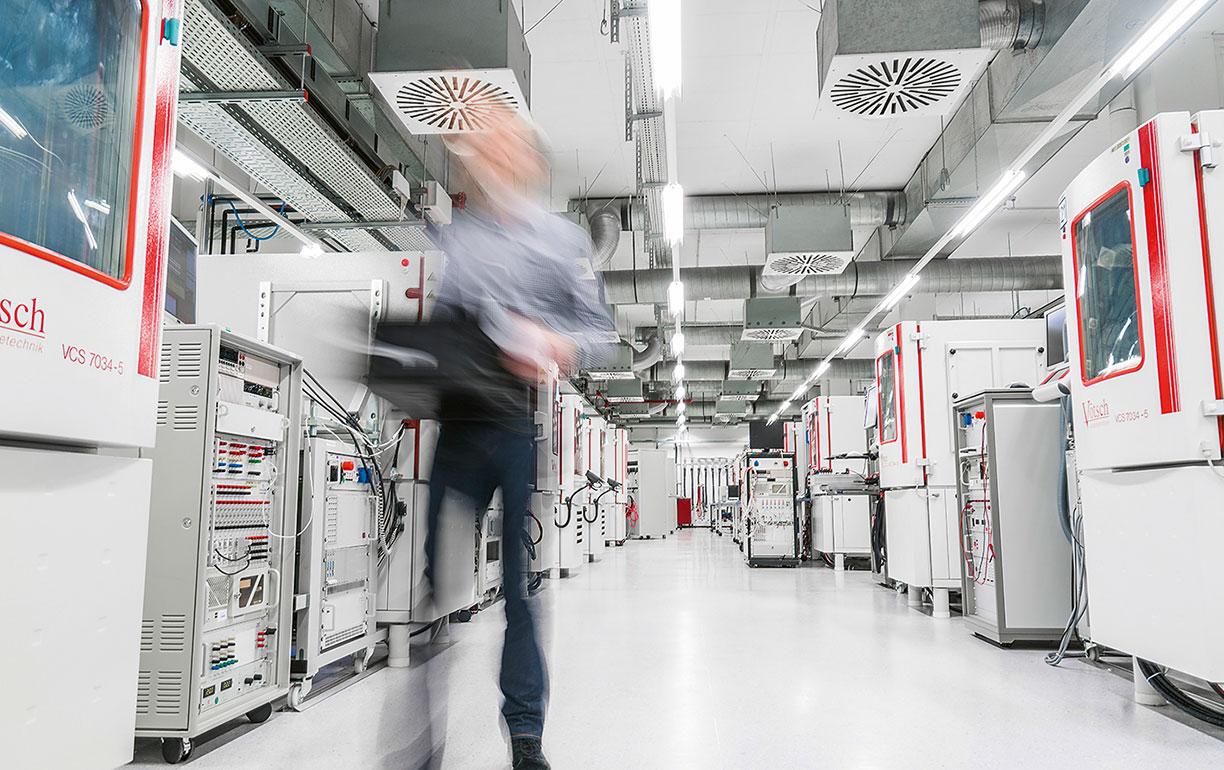
Shipments nach Schanghai.
Entscheidende Luftfrachtrouten für Marquardt führen von Frankfurt nach Mexico City, New York und Schanghai. „Von dort geht es per Lkw weiter zu unseren Werken in den jeweiligen Ländern“, so Weidner. Auch nach Atlanta lassen die Schwaben viel Luftfracht transportieren: Produktionsmaterial für den Standort eines Automobilkunden. In umgekehrter Richtung werden Teile, die in China produziert oder neu entwickelt wurden, von Schanghai und Hongkong nach Frankfurt und New York geflogen.
Der Dreh- und Angelpunkt der Unternehmenslogistik befindet sich aber am Stammsitz: ein 2012 errichtetes 10.000 Quadratmeter großes Logistikzentrum mit automatisiertem Kleinteilelager. „Hier schlagen wir unter anderem Ware aus unserem Werk in Sibiu in Rumänien um, die uns per Lkw erreicht und ab Frankfurt als Luftfracht transportiert wird.“ Dafür hat Andreas Weidners Team 2015 einen eigenen Road Feeder Service geschaffen: ein System mit zwei Zweierteams, die sich in Österreich ablösen.
All das soll nach dem Willen der Unternehmensleitung noch lange nicht das Ende der Fahnenstange sein. Bis 2020 wird ein Umsatz von mehr als zwei Milliarden Euro angepeilt – mit Automotive als entscheidendem Wachstumstreiber. Kleine Teile, große Ziele!
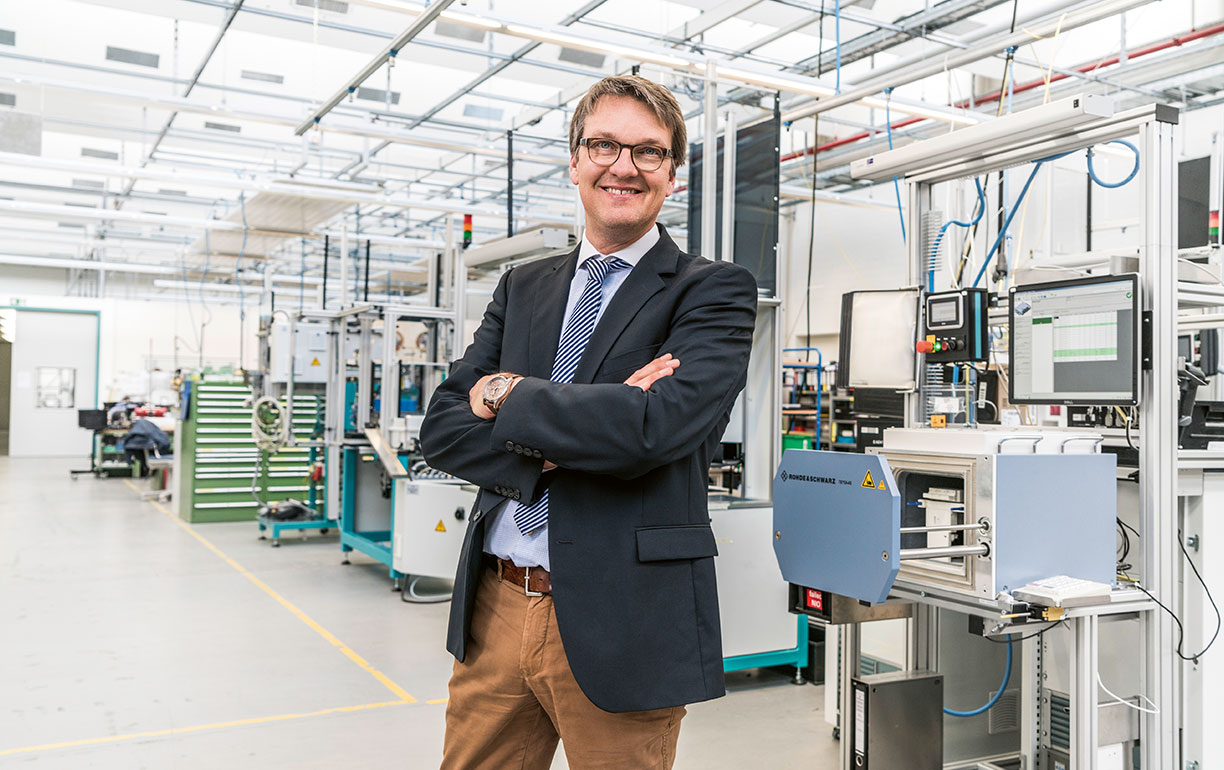
"In 2015 we had more than 4,500 tons of airfreight. In particularly urgent cases, we chartered an entire aircraft."
Andreas Weidner, Leiter Internationales Transportmanagement und Zollwesen, Marquardt-Gruppe.
Erfolgsfaktor Luftfracht: Andreas Weidner ist für das weltweite Transport- und Zollmanagement der Marquardt-Gruppe verantwortlich. 2015 ließ das Unternehmen immerhin 13 Prozent seiner Tonnage im Flieger befördern.
|
|
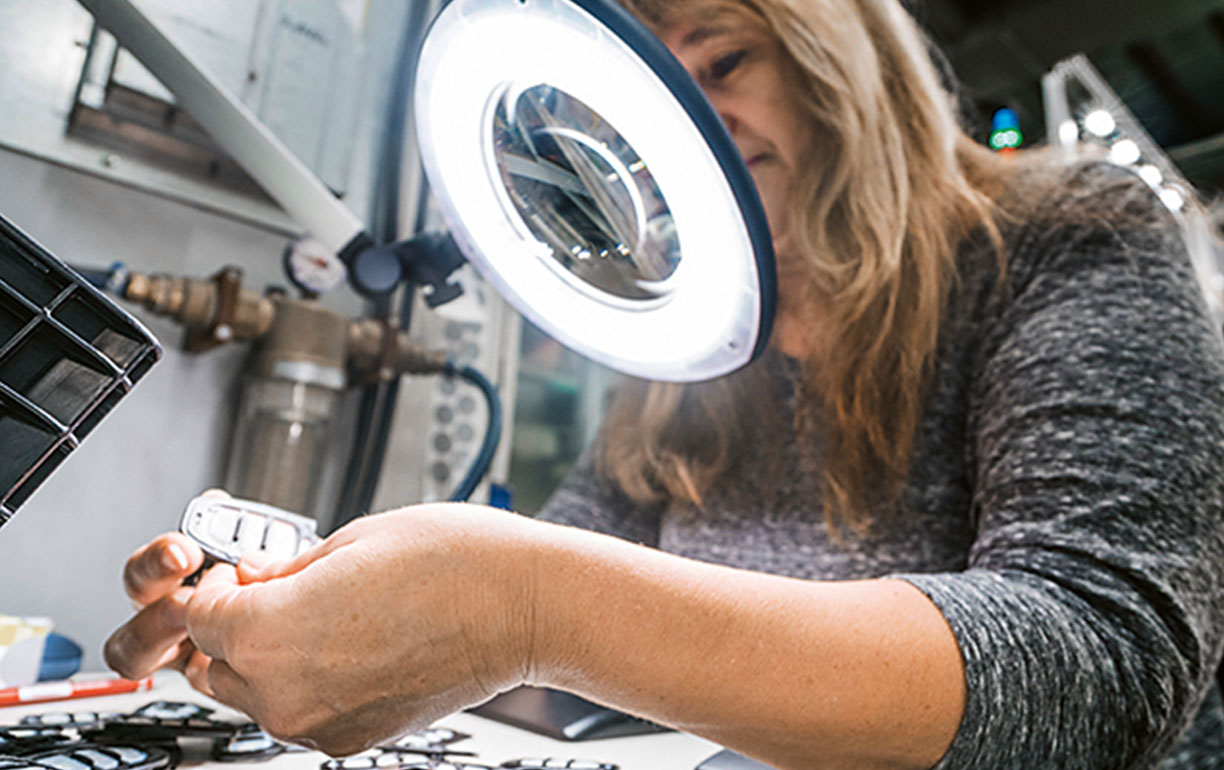
Komponenten für Autoschlüssel, Kippschalter und vieles mehr: Marquardt produziert zahllose Teile für die Autobranche. In Klimaschränken werden die Marquardt-Produkte extremen Temperaturen ausgesetzt und so auf ihre Widerstandsfähigkeit hin getestet.
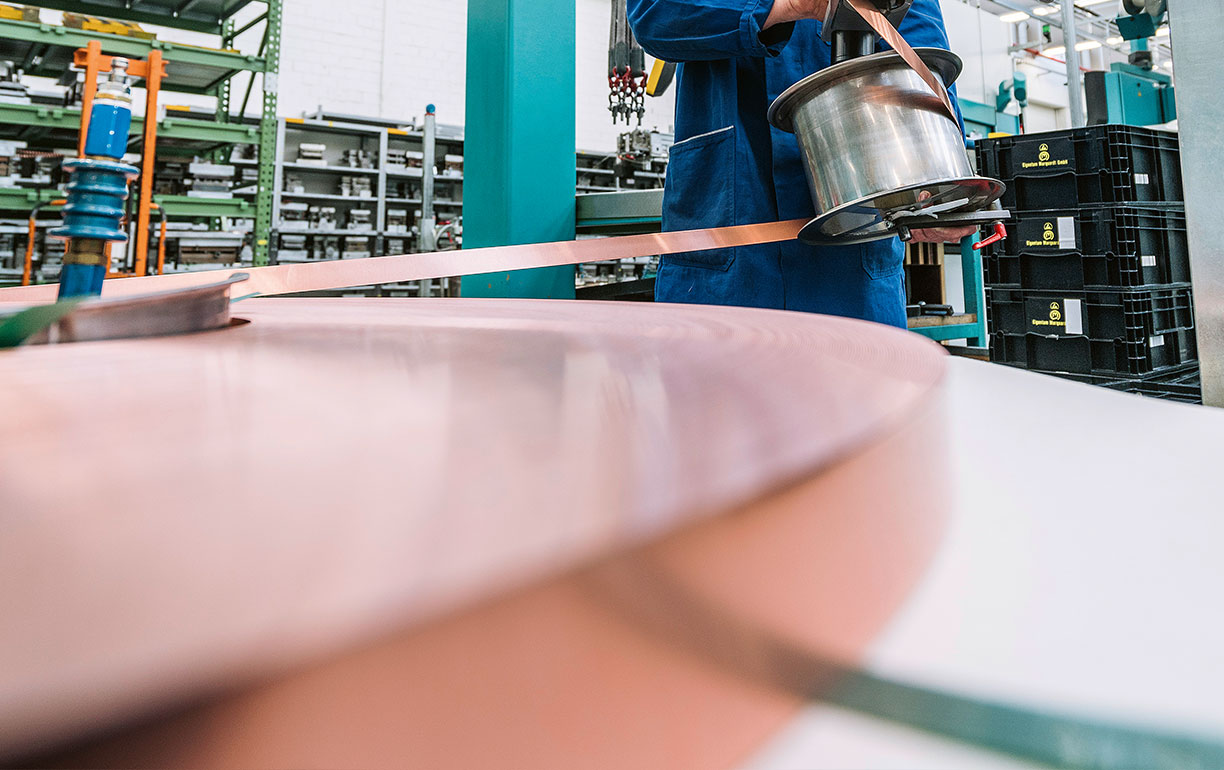
Constant supply:
Aus dieser Chrom-Nickel-Legierung werden Batteriekontakte für Autoschlüssel gestanzt.