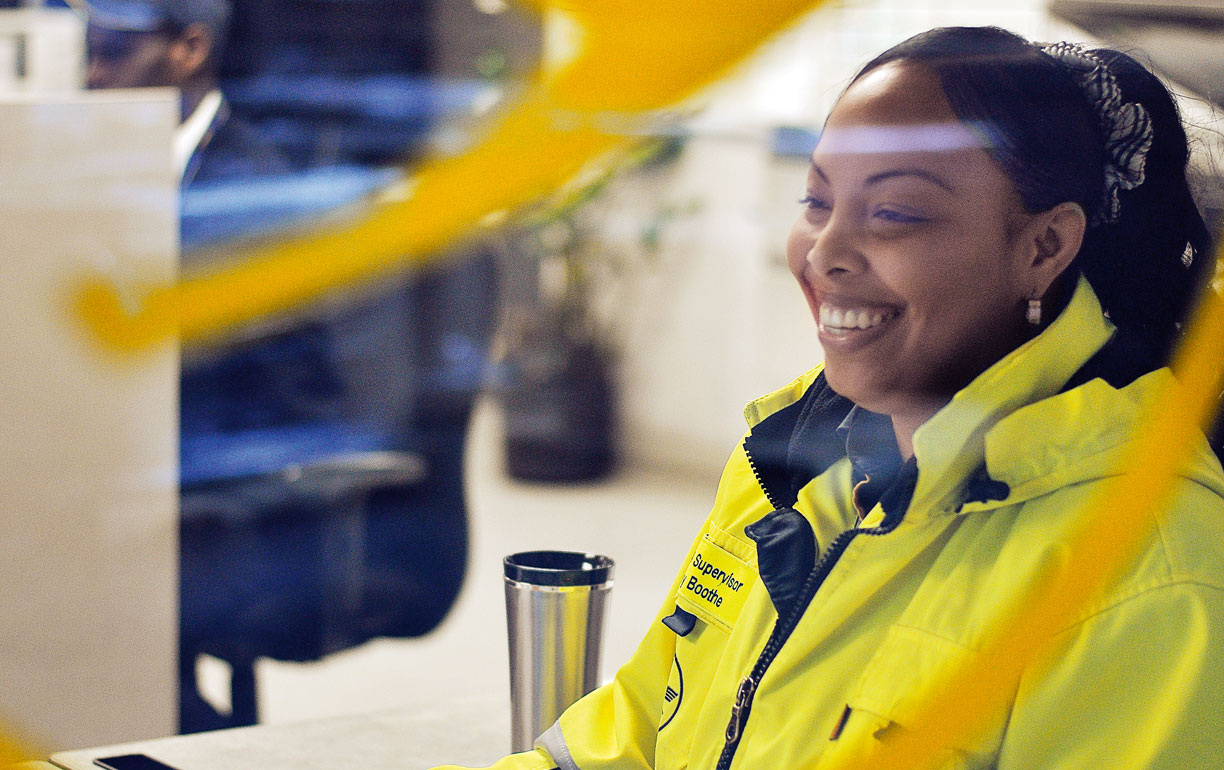
Blueprint New York.
Go to Gemba“ hat Vito D’Anna mit rotem Stift an das Whiteboard in seinem Büro geschrieben, ein Zitat aus der japanischen Management- und Betriebsführungslehre Kaizen. „Geh an den Ort des Geschehens“, lautet die Übersetzung. Was bedeutet: „Beobachte dort, wo du etwas ändern und verbessern willst.“ D’Anna managt für Lufthansa Cargo am John F. Kennedy International Airport in New York das Handling der Flugzeuge und im Warehouse – und strebt als Kaizen-Schüler nach kontinuierlicher Verbesserung. Mehr als 20 Jahre Arbeit bei der japanischen Nippon Cargo Airlines haben den heute 57-Jährigen geprägt.
Kein Wunder, dass Vito D’Anna die Hand hob, als es darum ging, eine „Station One“ aufzubauen: eine Musterstation, an der technische Innovationen und neue Prozesse in Kombination erstmals zum Einsatz kommen, erlebbar für Kunden und Kollegen. Das Ziel: die Dienstleistungen kontinuierlich verbessern – vor Ort und dann an den anderen Stationen rund um die Welt. Die Kriterien erfüllte JFK: Gesucht war eine Außenstation mit Frachter-, Passage- und Road-Feeder-Service-Betrieb, an der Lufthansa Cargo relevante Mengen an Tonnage und Umsatz verzeichnet. Das Groundhandling sollte hauptsächlich unter Lufthansa Kontrolle sein. So wurde der Flughafen im Stadtteil Queens zur Station One.
Um welche Neuerungen und Innovationen geht es? Um „Dock Enroll“ etwa. Mit dem System, von dem anfangs alle dachten, es heiße „Dock & Roll“, können Spediteure ihren Zollstatus online checken und per Vorkasse bezahlen. „Der altbekannte Bezahlprozess dauert zehn Minuten, mit Dock Enroll ist es nur ein Klick“, sagt Mitarbeiter Faraz Shaik, als er am Importschalter ein Bündel Dollarnoten von einem Fahrer entgegennimmt. Noch wichtiger: Dank dem Onlinecheck sinkt die Anzahl telefonischer Nachfragen, die in den USA zuvor pro Jahr bei 280.000 lag.
Copying recommended.
Copying recommended.
Ebenfalls in New York in Anwendung: das Prinzip des Lean Leadership. Dabei werden Verbesserungen nicht in großen Change-Projekten umgesetzt, sondern in der Alltagsroutine. Das erfordert tägliche Teamdialoge, Coaches schulen die Mitarbeiter für die „strukturierte Problemlösung in der Routine“. |
Viel Veränderung bedeutet viel Arbeit. Zumal JFK kein Testlabor ist und alles Neue im Routinebetrieb funktionieren muss. Doch „Change“ ist in der amerikanischen Arbeitskultur ein hochgeschätzter Wert. „Alle hier sind sehr offen gegenüber dem, was wir ändern – und vor allem, warum wir es tun“, sagt Alexander Karst, Direktor für Vertrieb und Handling an der US-Ostküste. Automatisierung und Digitalisierung müssten weiter vorangetrieben werden. „Von A nach B fliegen kann jede Airline genauso schnell wie wir. Wir wollen mit Sicherheit und Qualität am Boden punkten.“ Zuallererst als Fluggesellschaft, aber auch als Groundhandler für Fremdairlines wie Cathay Pacific, Qantas oder die israelische CAL. Als Projektleiterin hält Jule Parulewski vom Global-Handling-Management-Team von Lufthansa Cargo die Fäden in der Hand. „Die Station One soll Mitarbeitern und Kunden unsere Best Practices an einem einzigen Ort zeigen. Sie dient als Blueprint für andere Stationen, an denen das Konzept zum Beispiel auch im Rahmen einer Systempartnerschaft mit Groundhandling-Agenten umgesetzt werden kann.“ |
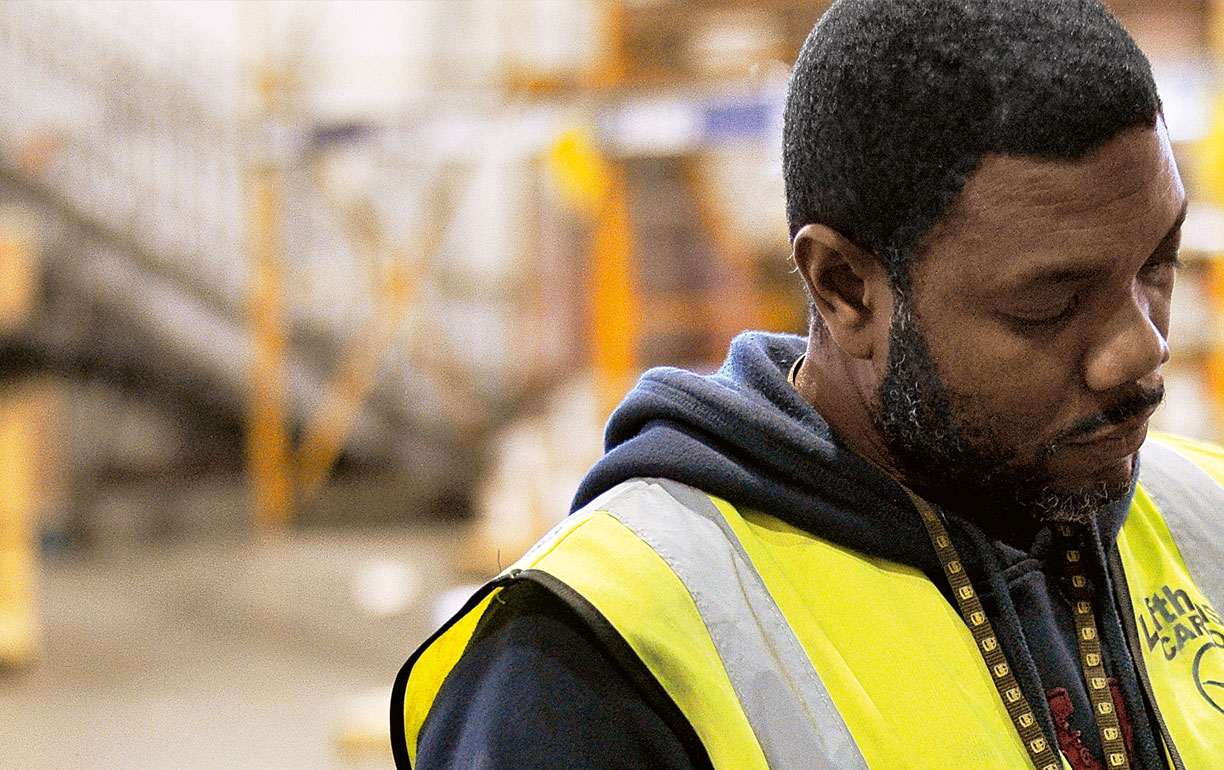
Jule Parulewski arbeitet in Frankfurt. Dennoch überzeugt sich die 30-Jährige regelmäßig in New York von den Fortschritten der Projekte, diskutiert neue Ideen – und packt pragmatisch mit an. Ob und wo am SmartGate Schutzvorrichtungen anzubringen sind, möchte ein Mitarbeiter von ihr wissen. Weil keine Sendung zur Hand ist, zieht Parulewski resolut eine Mülltonne auf die Wiegefläche, öffnet den Anzeigekasten mit einem extragroßen Schlüssel, der aussieht wie ein Dosenöffner, und erklärt das System.
Pro Projekt gibt es je einen Verantwortlichen in Frankfurt und New York, zwei Lean-Experten unterstützen die Zusammenarbeit und suchen stetig nach Möglichkeiten zum weiteren Entschlacken der Prozesse. Regelmäßig sitzen Vertreter von beiden Seiten des Atlantiks an einem Tisch, um gemeinsam festzulegen, was sich wie und warum ändern soll. „Wir verbringen hier viel Zeit mit Jule und ihrem Team“, sagt Kaizen-Experte Vito D’Anna. „Aber manchmal springen wir mitten im Meeting auf, weil die Arbeit ruft.“ Schließlich fertigt sein Team hier um die 90 Flüge pro Woche ab. Es herrsche ein sehr guter Teamgeist zwischen den Station-One-Mannschaften aus Frankfurt und vom JFK-Airport. „Wir haben Spaß auf dem Weg zum gemeinsamen Ziel!“
“Station One shows employees and customers our best practices at a single location”.
“Station One shows employees and customers our best practices at a single location”.
Jule Parulewski, Projektmanagerin Station One
Station one at a glance.
Station one at a glance.
Bereits umgesetzt Dock Enroll: SmartGate: Barcode-Scanning: Effizientes Lager: Supply Chain Management: Lean Leadership: |
In Planung eFreight: Digitale Rampe 1: Digitale Rampe 2: Mobile Volumenoptimierung: Flussorientierte Prozesse:
|
Mehr Informationen zur Station One und ihren Innovationen im Film der iPad-Ausgabe, kostenlos im App Store.
Fotos:
Lufthansa Cargo