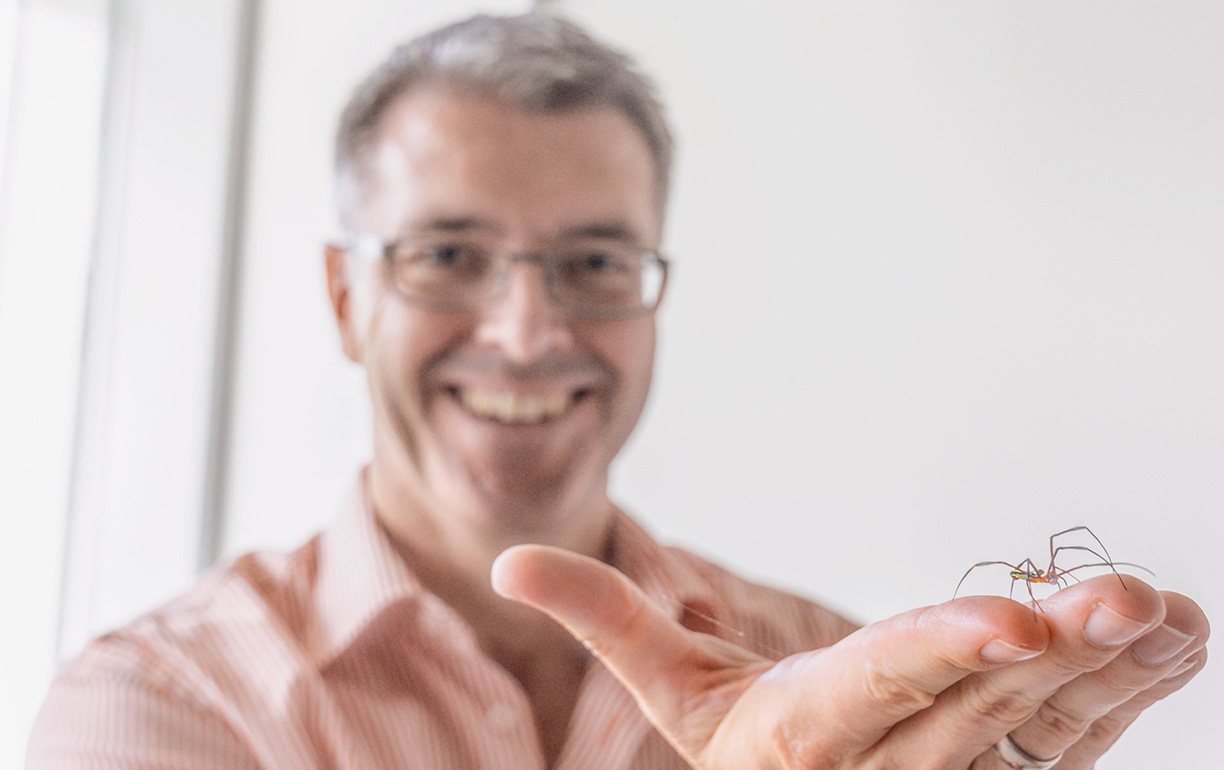
Spider-Man.
Consider airplanes weighing only half as much as they do today, yet still being twice as strong. Picture a world where commerce and industry could do away with plastic completely and no longer add to the carpet of micro plastics already floating out in the Pacific Ocean. And what if defective heart muscle tissue could be accurately reproduced using a synthetic material?
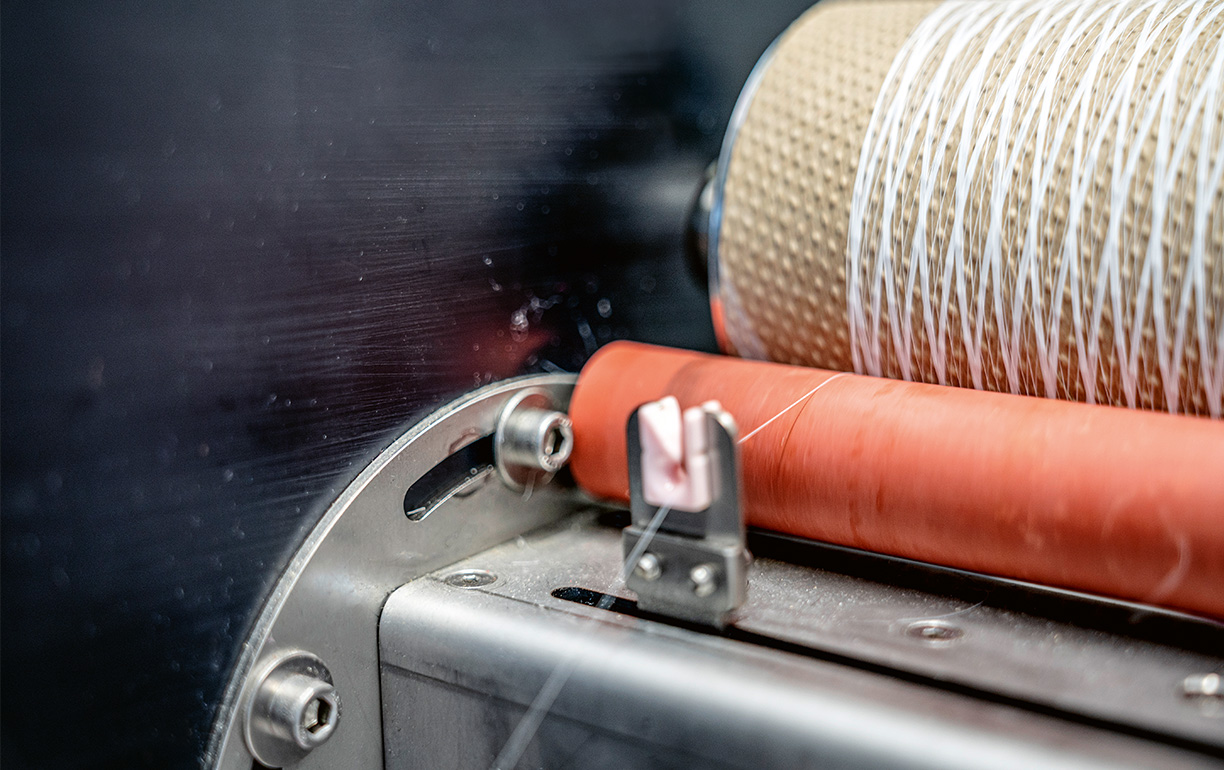
A material like this could revolutionize both the economy and society. And it already exists: spider silk – extremely strong, yet flexible, and biodegradable as well as sterile. And because this material can now be manufactured artificially, new opportunities are opening up for numerous sectors of the economy.
The man who succeeded in developing a process for the production of spider silk on a large scale for the first time – a feat that earned him a nomination for the European Inventor Award of the European Patent Office last year – is Thomas Scheibel. Scheibel is a professor at the Chair of Biomaterials at the University of Bayreuth and the founder and shareholder of the start-up AMSilk, the company set up to manufacture synthetic spider silk on a commercial scale together with partners and market it under the name Biosteel.
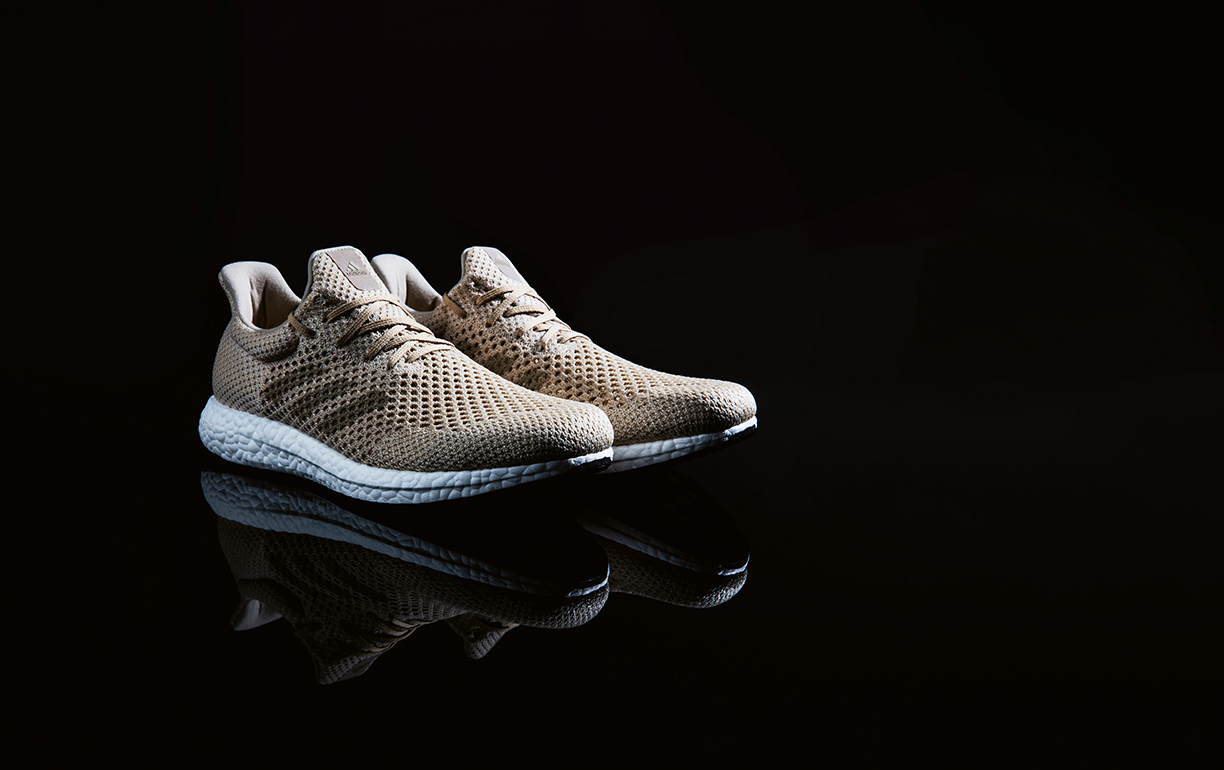
Industry responds enthusiastically.
Some well-known companies have already declared their intention to use synthetic spider silk thread: Adidas has developed a running shoe that is unrivaled in terms of its light weight and its strength, and it will soon be produced in large quantities. And Omega has produced a particularly skin-friendly watch strap made from synthetic spider silk.
Spider silk proteins have already been used in the cosmetics industry for years now. In creams or nail polishes they produce a breathable protective film on the skin. AMSilk recently managed to sell its cosmetics division to the Swiss industry giant Givaudan. The medical technology industry has also recognized the potential of synthetic spider silk: “The material is sterile, which means it can be used on and inside the body without causing the body to reject it,” says Scheibel.
The aviation industry is also enthusiastic: Airbus and AMSilk have signed a cooperation agreement for the development of materials for aircraft manufacture that are based on synthetic silk. Many components of large commercial aircraft are already made from composite materials instead of aluminum in order to reduce weight. In the future the AMSilk material could be used here instead of carbon compounds as this would reduce the weight even further and enhance durability.
The multitude of applications in which spider silk can be used has also aroused the interest of Lufthansa Cargo. Airfreight pallets, for example, still have to be wrapped with considerable quantities of plastic film today in order to secure the load and protect it from external conditions. The cargo airline’s environmental management is therefore looking into the question of whether film made from spider silk, which would be completely biodegradable, could replace the mountains of plastic that are difficult to recycle in the medium term.
In Professor Scheibel’s institute, there already is a machine that can manufacture a film that is unmatched in terms of its thinness and strength. Moreover, the scientist is convinced that the material can soon be produced economically on a large scale. Which means it could then also be used to manufacture cheap everyday products like foils and packaging. “The process is similar to that used to manufacture laundry detergents,” says Scheibel. Once the relevant – albeit considerable – initial investment is in place, spider silk may offer a real prospect of replacing environmentally harmful plastics in the long term, thus solving the global micro plastics problem.
Spider silk proteins have already been used in the cosmetics industry for years now. In creams or nail polishes they produce a breathable protective film on the skin. AMSilk recently managed to sell its cosmetics division to the Swiss industry giant Givaudan. The medical technology industry has also recognized the potential of synthetic spider silk: “The material is sterile, which means it can be used on and inside the body without causing the body to reject it,” says Scheibel. The aviation industry is also enthusiastic: Airbus and AMSilk have signed a cooperation agreement for the development of materials for aircraft manufacture that are based on synthetic silk. Many components of large commercial aircraft are already made from composite materials instead of aluminum in order to reduce weight. In the future the AMSilk material could be used here instead of carbon compounds as this would reduce the weight even further and enhance durability. |
The multitude of applications in which spider silk can be used has also aroused the interest of Lufthansa Cargo. Airfreight pallets, for example, still have to be wrapped with considerable quantities of plastic film today in order to secure the load and protect it from external conditions. The cargo airline’s environmental management is therefore looking into the question of whether film made from spider silk, which would be completely biodegradable, could replace the mountains of plastic that are difficult to recycle in the medium term. In Professor Scheibel’s institute, there already is a machine that can manufacture a film that is unmatched in terms of its thinness and strength. Moreover, the scientist is convinced that the material can soon be produced economically on a large scale. Which means it could then also be used to manufacture cheap everyday products like foils and packaging. “The process is similar to that used to manufacture laundry detergents,” says Scheibel. Once the relevant – albeit considerable – initial investment is in place, spider silk may offer a real prospect of replacing environmentally harmful plastics in the long term, thus solving the global micro plastics problem. |
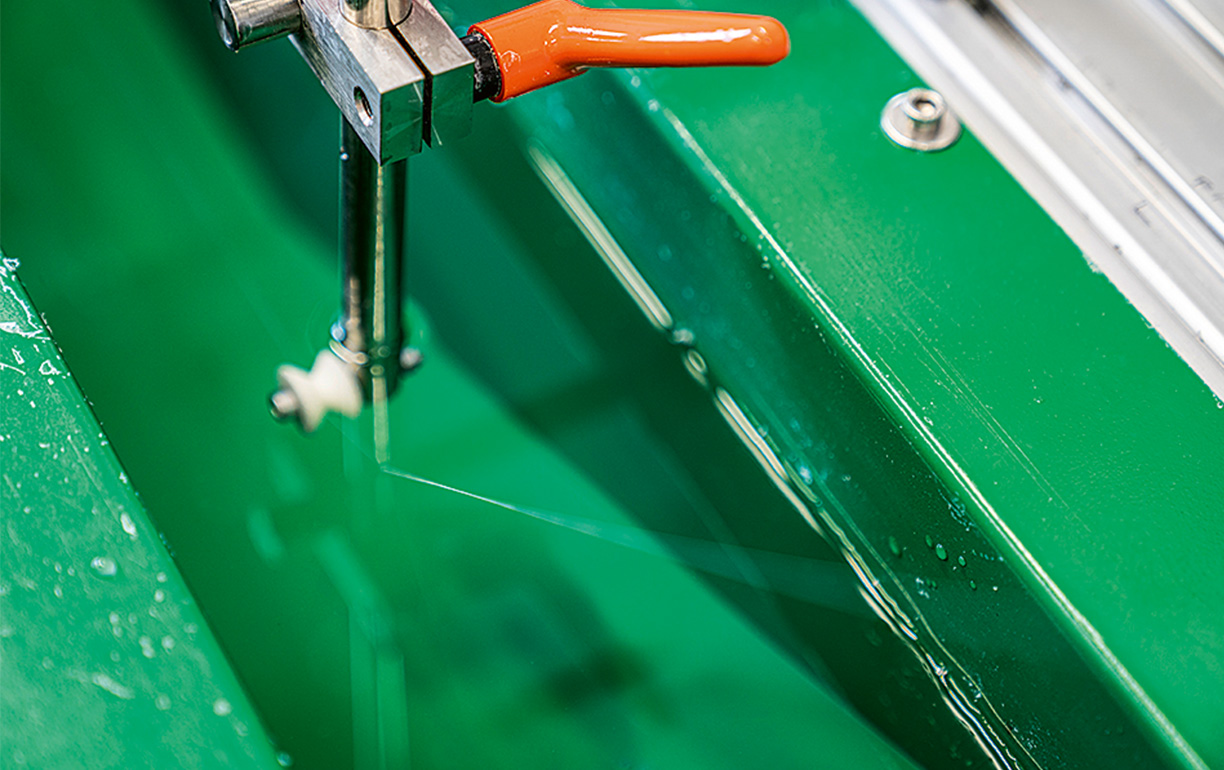
Silk-making took ages to learn.
People have had a fascination for the special strength and elasticity as well as the fineness of spider silk ever since ancient times. The material has also long been used for wound dressings. Since the 1980s, scientists and manufacturers have been dreaming of producing spider silk synthetically – and they have failed time and again over the years. Using natural ways to produce the material in large quantities is not possible – spiders are cannibalistic in nature and would end up eating each other if bred in large numbers.
Scheibel sees two reasons why his earlier competitors have failed in their efforts: “Some of them were grounded in materials science and were focused too heavily on the material itself and the process by which it is produced. Others were biologists, and their focus was firmly on the animal.”
But Scheibel is a biochemist. Prior to devoting his efforts to spider silk, his research concerned the BSE pathogen; this was at the end of the 1990s. “Back then I wasn’t really interested in spiders at all,” the 50-year-old frankly admits. “What I did want to understand was the exact nature of the proteins that are responsible for the special properties of spider silk.” This approach provided the key to the eventual success, but it still required years of meticulous scientific work.
Scheibel and his team have been researching the proteins spiders use to make their silk since 2001. The method that made it possible years later to produce silk in the laboratory using genetic engineering and biotechnology looks simple at first glance: the DNA responsible for the production of the spider silk is copied from the spider’s genetic material. It is then inserted into the genetic material of bacteria. The bacteria then produce the spider silk protein, and this can be harvested and processed into a white powder.
However, in order to learn how to spin a thread from the material obtained in this way, the team had to undertake additional research to identify and understand the chemical and mechanical tricks being performed inside the spider’s body. For instance, the spider thread ends up with its unique properties only because, depending on the thread’s intended use, the spider spins it using different raw materials from separate reservoirs located inside its abdomen.
Scheibel sees two reasons why his earlier competitors have failed in their efforts: “Some of them were grounded in materials science and were focused too heavily on the material itself and the process by which it is produced. Others were biologists, and their focus was firmly on the animal.” But Scheibel is a biochemist. Prior to devoting his efforts to spider silk, his research concerned the BSE pathogen; this was at the end of the 1990s. “Back then I wasn’t really interested in spiders at all,” the 50-year-old frankly admits. “What I did want to understand was the exact nature of the proteins that are responsible for the special properties of spider silk.” This approach provided the key to the eventual success, but it still required years of meticulous scientific work. |
Scheibel and his team have been researching the proteins spiders use to make their silk since 2001. The method that made it possible years later to produce silk in the laboratory using genetic engineering and biotechnology looks simple at first glance: the DNA responsible for the production of the spider silk is copied from the spider’s genetic material. It is then inserted into the genetic material of bacteria. The bacteria then produce the spider silk protein, and this can be harvested and processed into a white powder. However, in order to learn how to spin a thread from the material obtained in this way, the team had to undertake additional research to identify and understand the chemical and mechanical tricks being performed inside the spider’s body. For instance, the spider thread ends up with its unique properties only because, depending on the thread’s intended use, the spider spins it using different raw materials from separate reservoirs located inside its abdomen. |
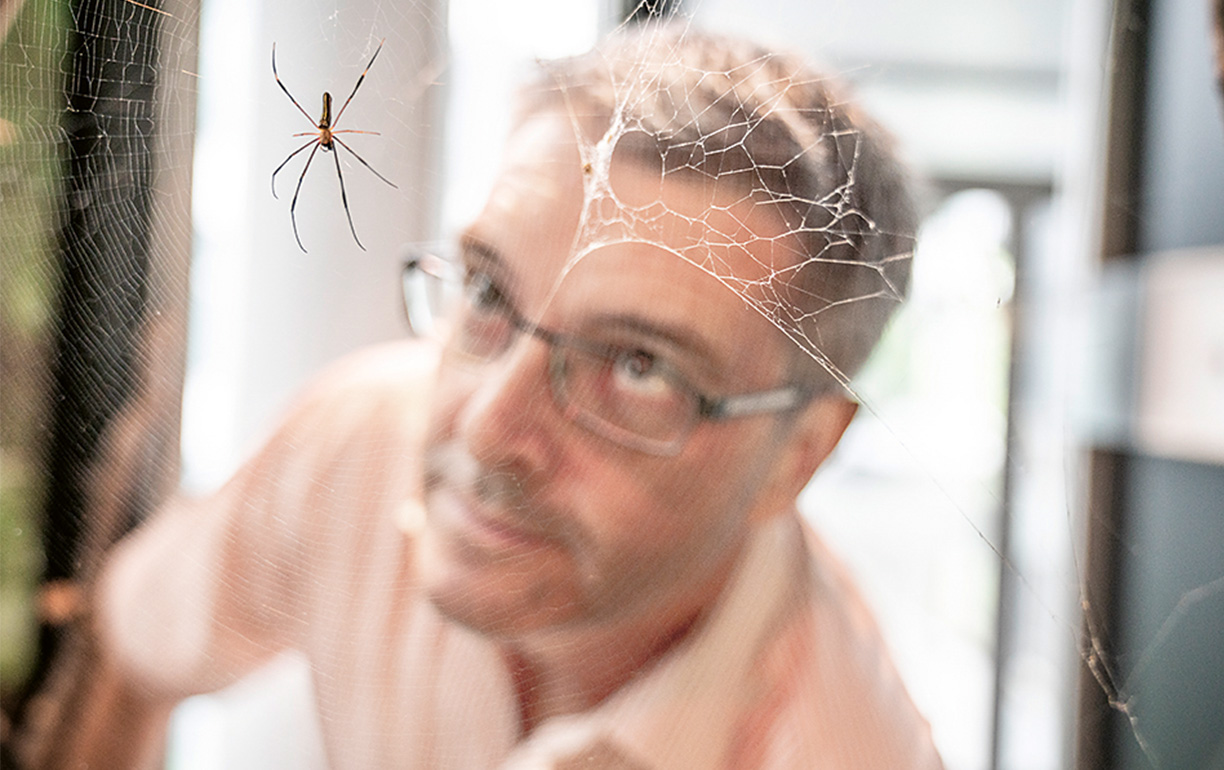
Samples from the jungle.
The amount of tension the spider applies when spinning the thread is also of great importance: the tension ensures that the protein molecules are uniformly aligned, which is what gives the thread the desired strength and flexibility. It took almost ten years before Scheibel and his team members were able to emulate this process in the laboratory. Today special wet spinning plants can produce the thread in large quantities, and AMSilk is in talks with a large number of industry partners regarding the next steps to take.
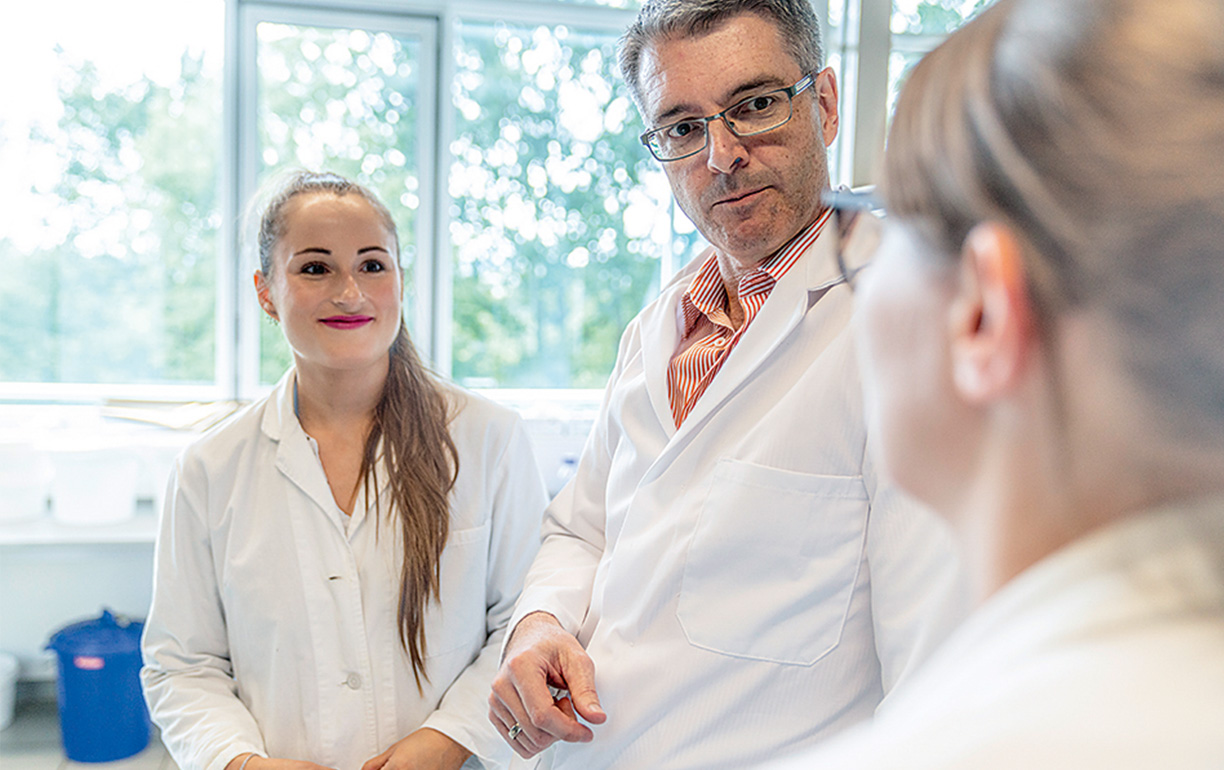
Efforts are also under way to push the research further – and to do this, they have enlisted the help of Lufthansa Cargo: a member of Professor Scheibel’s team is in the jungles of Colombia right now searching for new species of spiders, so that the scientists can investigate the properties of the silk they produced. The aim is to be able to produce even better synthetic silk, and to identify new areas of application. The natural spider silk is collected locally and wound onto spools. This cargo is then flown from Bogotá to Bayreuth for analysis. Constant temperature, pressure and, above all, humidity conditions must be maintained throughout transport. Speed is of the essence here. “Unlike our biotech silk, natural spider silk tends to age as a result of other substances adhering to the proteins,” explains Scheibel. This is why the spools with the natural spider silk are flown to Europe on board a Lufthansa Cargo Boeing 777F as a “Fresh” shipment.